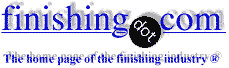
-----
Stainless steel grades used in a car exhaust manifold
Q. I'm having a hard time trying to figure out what type of grade of stainless steel I should use for a custom made stainless steel exhaust manifold. Most people use 304 but I feel because of the heat generated in the exhaust a better grade is required -- but which one.
From what I have read grade 309, 310 or 316 with titanium or even 321 with titanium could do. Can you tell me which one is better for this application? Keep in mind corrosion, heat range, flexibility due to engine vibrations, etc.
Thank you.
- Dorval, Quebec, Canada
2005
A. 400 series, say 410, is usually used for the hot section -- from the engine to muffler. Muffler and subsequent pipes are usually 304.
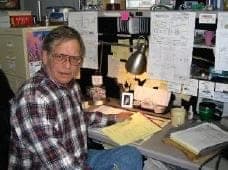
Jeffrey Holmes, CEF
Spartanburg, South Carolina
2005
A. Dear Michel L'Abbe,
You can use AISI 409 grade stainless steel. It is a titanium stabilised ferritic stainless steel. It may form a light protective rust layer in exhaust gas atmospheres. It is readily weldable.
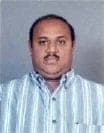
T.S.N. Sankara Narayanan
- Chennai, Tamilnadu, India
(ed.note: The good doctor offers a fascinating blog, "Advancement in Science" )
2005
Carbon Fiber Experimental Muffler Design
Q. I am using a Husqvarna 394 chainsaw engine in a large scale experimental A/C. This engine is 5.7 cu in or 94 cc and churns out 5.2 kW at 9000 RPM. It sounds like what it is - a chain saw.
I would like to build a new muffler to quiet down the beast - perhaps in carbon fiber?
Anyone have any design information or suggestions?
Thanks,
Jack.
Jack Lovelock- New Zealand
2001
2001
A. Jack,
First of all, I know naught about chain saws ... but did piddle about with a straight through muffler years ago on my Volvo 123 GT.
Firstly, I don't think that carbon fiber is of any use. Too damned expensive and it is the RESIN which always counts in a temperature/corrosion application, not the structural.
If you want to make the beast from FRP (fiberglass), try to lay your hands on a good resin (Atlac, Hetron, Derakane) if you can. Personally I wouldn't use it.
Anyhow ... the muffler. You should have an exhaust outlet pipe of XYZ inches or whatever. Try getting some copper pipe of the same diameter. Then get a larger dia. pipe of copper or something chromed, if you wish. Say min. 2" larger.
Drill lottsa holes in the copper. Sleeve over the larger pipe. Close the end(s). Ram fiberglass (ideally FRP mat NOT resin coated!) in between. Length of this adapter? Dunno. Say 12" but try it out @ 6" initially.
The IDEA is to allow the noisy gases to exit through all those holes you've drilled ... the fiberglass mat vibrates as the exhaust gases hit it and turns the sound into heat.
Try it out. Worked like a charm got me aeons ago.
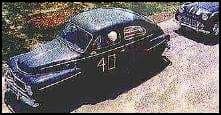
Freeman Newton [deceased]
(It is our sad duty to advise that Freeman passed away
April 21, 2012. R.I.P. old friend).
A. Anything involving copper would be a no no. It would anneal in no time flat.
Tim Goodsell- Figtree. NSW, Australia
February 15, 2010
A. Not knowing your level of experience I apologise if this is at too low a level.
On an exhaust then check the temperatures that would be required. Then choose the impregnation resin accordingly. Usually higher service temperature resins require a higher temperature cure which would affect the form tooling required. Tooling costs for carbon fibre production are usually high anyway, make sure your budget will accommodate such costs.
If you are going to laminate several layers of a woven fabric then keep the layers symmetrical in regards to ply orientation. This will reduce any stresses built into the part and reduce spring back when the part is removed from the tooling.
Also a commonly ignored pitfall may be the mode in which the muffler will be attached and what it will be in contact with when it is fitted. Galvanic corrosion is a problem with Carbon fibre parts.
Ciaron Murphy- Great Britain
2001
A. I may have some guidelines for you on this one. Firstly, I'm assuming that this chainsaw motor is a two stroke because most of them are.
If you want to put a system(muffler) on this engine you really need to go down the right path to begin with or else it really is a waste of time.
You need to build an expansion chamber system for this engine, the new system should boost your power quite considerably if what you are currently running is a straight pipe.
For those who aren't familiar, an expansion chamber system is used on two stroke engines(good one's anyway), it is comprised of a large diameter tube section with perfectly calculated 'cones' on each end, the exhaust tube from the engine goes into one end and the tailpipe comes out the other, on the end of the tailpipe is a stinger(muffler). The exhaust gases enter the expansion chamber from the cylinder and as they travel rearward are 'reflected' by the cone at the tailpipe end back toward the engine, due to the two stroke's cycle nature the exiting exhaust gas draws some fresh mixture along with it out of the tailpipe, this 'reflected' exhaust gas now traveling back toward the engine forces the fresh mixture back into the cylinder and in effect contributes a pressurising effect (+psi) to the cycle. At certain RPM's the exhaust gas reaches an ideal resonance which provides the optimum operation of the chamber, from when this resonance starts to when it finishes is known as the 'powerband'.
On the end of the tailpipe is a small muffler, it has an outside casing with a tube which is sealed on the inside but open at the back of the muffler, this tube has 'holes' in it that are covered with packing(glass mat style).
This is designed to increase pressure somewhat inside the chamber and therefore does not have a flow rate like a normal exhaust, which makes it not only a better exhaust system, BUT A QUIET ONE.
Stewie [last name deleted for privacy by Editor]- Adelaide, Australia
A. The Australian is right, for a 2-stroke you want to use a tuned exhaust. Particularly if you plan on running primarily at a constant RPM. This is used regularly on 2-stroke go carts, they use chain saw engines all the time. You may look there (go cart racing sites) for an exhaust design. The expansion chamber may be welded thin wall aluminum, I think the temperatures will be too high for composite. Usually anything over about 350 F is out.....
The trailing muffler may be made from off the shelf composite tubing, the gas will be cooler behind the expansion chamber.
Connecting the composite to aluminum will require a nonconductive (electrically) gasket to reduce corrosion. With the temperature and moisture in exhaust, the corrosion issue may be a show stopper.
Dave Lynch- Cupertino, California
2002
Q. Just wondering if it was possible to make a full exhaust system out of carbon fibre.Would there be any problems with heat or corrosion, would vibration be a problem because for the application I want to use it where the heat and vibration would be at their most furious.
J NITEdesigner/metal finisher - Australia
2007
Muffler design
2001Q. Sir,
We are engr. students in India.We are interested to make project in muffler design for final year. We want to get information regarding the muffler design for generators. So we need your help in that. Please you send some information which is helpful for us. We need help in following parameters,
- 1] pressure control
- 2] velocity control
- 3] frequency measurement
Please send message as early as possible,
Thanking you. Yours faithfully,
Swapnil Gandhi- Kolhapur, Maharashtra, India
A. The questions you have raised are difficult to understand. Instead of that you should stress on the objective, scope of the work. We have well established sound & vibration lab used for muffler evaluation with FFT analyzer
Ajit K. Kharade- Karad, Maharashtra, India
2003
Q. We have Back pressure detail of our engine, and sound level specs. Will it be possible to design / validate a designed muffler in FTT?
Thanks.
- Bangalore
March 13, 2008
Supertrapp big block muffler
Q. How can I modify a 4 inch diameter Supertrapp muffler to maximally reduce noise levels generated by a 7 liter (427 cubic inch) displacement engine? The perforated inner tubing surrounded by glass wool is at the end of the larger outer tubing. The muffler is attached to a set of headers, and there is a foot of unrestricted 4 inch pipe upstream from the glass wool portion. Is this a functional resonating chamber? Can reflectors or cones be placed there to further reduce noise?
Thanks,
M.M. McDaniel- Laguna Beach, California
2002
2002
A. Hi MM,
I don't quite understand your question. You say that the muffler is connected to headers? WHAT! Surely the muffler is at the rear end of the exhaust system.
Then you say you have an 'unrestricted' length of 4" dia pipe. Ah, if that's true, consider the following approach.
l. Firstly get hold of a shroud (IF available) that is larger by 2" or so than the 4" pipe. Said shroud to have a neck to closely fit/weld/screw onto the 4" pipe.
2. Then get some copper pipe of 4" dia. Have the end flared to fit over your pipe. Say l foot long.
3. Then DRILL lots of small holes, say, 1/8" dia ... maybe 4 per peripheral inch and, say, 1/2" apart longitudinally ... you might well say to yourself, why copper? No particular reason but just you try drilling a zillion holes in your steel and you'd know WHY!
4. Having done that, join up to the main 4" pipe (after cutting off 1 foot from this pipe) ... then locate/fit the shroud ... then get some fibreglass wool and force that into the peripheral gap. Then make up a cover plate of some sort to prevent the wool from coming out.
... another way to reduce noise is to DRIVE SLOWLY !
P.S. I did something like this myself where I was lucky enough to get a twin outlet resonator. Onto the twin outlets I brazed (?) on the predrilled copper pipe and then used a standard chrome plated exhaust 'cover' ... only 6" long. In your case (if such an animal exists) you'd need twin 3" dia. outlets which from a velocity viewpoint would lower the exhaust gases speed by 1702% or so as well.
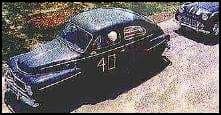
Freeman Newton [deceased]
(It is our sad duty to advise that Freeman passed away
April 21, 2012. R.I.P. old friend).
Using CRCA for a Chambered Muffler for a generator set engine?
Q. Sir ,
I am fabricating a chambered muffler for a 550cc diesel generator set engine in our college as a part of my project. Is it advisable to use CRCA for fabrication?. If not, please suggest an alternative.
Student - Dharwad,Karnataka, India
March 30, 2014
Q, A, or Comment on THIS thread -or- Start a NEW Thread