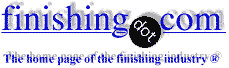
-----
Coatings on Aluminum for Electrical Insulation
Q. Can the boiling method of creating an electrically insulating coating be used on aluminium foil (industrial grade, 99% pure, 0.05 mm thick)?
I guess that I would need to loosen the coils to ensure full coverage; not sure how to do that with 60 m x 0.3 m rolls of 0.05 mm foils?
The purpose is allow the creation of foil coils
2022.help.altair.com/2022/flux/Flux/Help/francais/ReleaseNote/ReleaseNote_Flux2022/topics/Flux2022_NewFeature_FoilCoilWindings.htm
for use in lightweight electric motors. Max voltage: say 48V.
(I don't believe that such thin foil would bear immersion in sulphuric acid for anodisation.)
Thanks for any suggestions,
- Not US
June 1, 2024
Tip: This forum was created to help build camaraderie through sharing tips, opinions, pics & personalities.
The operator & those readers who want that might not engage with anonymous posters.
A. Hi Buk. The comment re. the boiling method is from a "regular" on the site and I have no doubt that it's true. Wernick, Pinner, and Sheasby is more than 1270 pages so it can be hard to find some stuff, but Fig. 82 (in the 5th edition) seems to show a thickness of oxide film of about 1.2 µm for 99.99% pure aluminum and about 0.6 µm for 99.5% pure after 20 hours in 100 °C distilled water.
Hopefully this is enough ammunition to support cutting some pieces of foil and testing them for thickness and dielectric or resistance to see whether the process holds any hope.
Although aluminum foil can be "web processed" and was probably manufactured that way, I think you'd probably have to cut it and hang it on racks for a boiling process to be feasible.
You're probably right that getting sufficient anodizing current through a sheet that is only 0.05 mm thick would be difficult and, if it can be done at all, it would only be by unrolling it and handling it as a continuous web.
Luck & Regards,
Ted Mooney, P.E. RET
Striving to live Aloha
(Ted can offer longterm or instant help)
finishing.com - Pine Beach, New Jersey
Q. Thanks, Ted.
The problem with cutting it up is that I want the full 60 m lengths. The idea here is to slit [https://en.wikipedia.org/wiki/Roll_slitting] the rolls into narrow (some 27 mm wide others 45 mm) strip rolls and attach wires to both inner and outer ends using conductive adhesive. Each of these then forms a coil to be used in a home made electric motor.
Assuming I can make the coil insulated.
The problem with "trying it", is that these coils cost a substantial amount of money (e.g. bsfixings.uk/5kg-aluminium-foil/) and I will need several, so I rather know I can make this work before committing scarce pensioner funds to a purchase.
I can (and will) try this on a few pieces of household (cooking) foil; but I'm unconvinced that these aren't coated in some way (shiny side vs dull) that might screw with the process and/or result.
- NotUS
June 3, 2024
A. Hi again.
Aluminum foil is not coated (although specialty coated non-stick foil is available for special needs). It is rolled down from thicker slabs two at a time; the shiny side is from contact with the rolls, and the dull side is where the two slabs are pressed against each other. Most foil is 99.93+% pure, and the 'heavy duty' consumer foil is 0.02 mm thick. You can get 0.05 mm thick "industrial" foil but I haven't priced it.
Luck & Regards,
Ted Mooney, P.E. RET
Striving to live Aloha
(Ted can offer longterm or instant help)
finishing.com - Pine Beach, New Jersey
⇩ Related postings, oldest first ⇩
Q. Can I dip my aluminum discs in some kind of conversion coating bath and expect a thicker oxide layer to have grown and withstand higher voltages?
Does anyone know what happens if I boil my aluminum in deionized water and get some kind of boehmite layer?
transducer manufacturer - around Boston
2005
A. Hello Jose.
In general, conversion coatings are used on aluminum when conductivity is to be maintained, and anodizing is done when insulative value is sought. Is there a reason they can't be anodized? sulfuric acid anodizing is the most common and probably the least expensive for this purpose, but boric acid anodizing is used for electrolytic capacitors and might suit your needs.
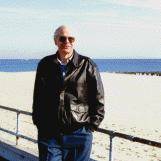
Ted Mooney, P.E.
Striving to live Aloha
(Ted can offer longterm or instant help)
finishing.com - Pine Beach, New Jersey
Treatment &
Finishing of
Aluminium and
Its Alloys"
by Wernick, Pinner
& Sheasby
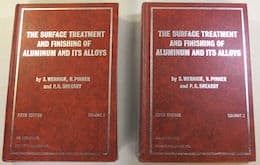
on eBay or Amazon
or AbeBooks
(affil link)
A. Hello,
According to Wernick, Pinner, and Sheasby ⇨
you can get a thin but highly protective coating by boiling aluminum for 20 hours in distilled water. The coating itself would be non-conductive as well as protective, but whether or not it would be thick enough to prevent your voltages from breaking through (this would also be affected by the pressure exerted by your contacts as well) would have to be determined.
As a manufacturer though - definitely take Ted's advice! The boiling water would probably end up being more expensive, and you couldn't be as certain of the quality. Anodizing would be the way to go. Good luck.
Compton, California, USA
Q, A, or Comment on THIS thread -or- Start a NEW Thread