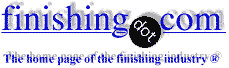
-----
Nickel peeling off with file test
Q. We are having a problem with a BARREL copper then nickel coated product.
After copper nickel coating is applied a filing test is done where we take a file at 45 degree angle and file it. We are finding that the nickel is peeling off.
Just to keep in mind that these product are small round articles made of steel not brass and they are used in windscreen wiper motors and are very heavy (per unit).
We started with the problem where nickel was peeling off nickel that indicated a loss of current.We slowed the barrel rotation down to a slow slow speed that it almost does not turn to help the products to remain in contact. The nickel is very soft and bendable and is about 10 µm thick. The problem seemed to be solved but another was created because it is now peeling off the copper. The process is as follows:
1. Degrease alkaline cleaner
2. sulfuric Cleaner
Articles are now dried
3. HCl pickle
4. cyanide copper plate 30 minutes 10 volts
plenty rinse
5. Acid pickle salt for copper
plenty rinse
6. 10% sulfuric
no rinse
7. nickel plate 8 kg for 30 minutes 8 volts ..very slow barrel speed.
If anyone has a suggestion please let me know.
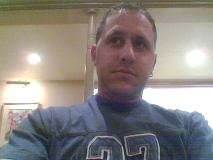
Gary Joseph
Johannesburg,
South Africa
2005
A. Hi Gary,
I would skip no.5, after cyanide copper plating, acid pickle in HCl Acid, quick rinse, and proceed to Nickel plating.This would reduce passivation of copper plate prior to nickel plating.
Excessive brighteners in nickel plating may cause brittle deposits that come off easily from the copper plate.
Barrel plating are actually 'make and break' contact plating as the parts are moving in the barrel. But to a certain extent , the time for 'make and break' contact in the barrel are in split seconds and I don't think it has a profound effect.
For copper plating, as copper deposits are soft, 1 to 2 RPM barrel rotation is not unusual.
For nickel plating, 5 to 10 RPM is not unusual to agitate out the hydrogen during polarization and generally expose all surfaces to have almost equal deposits.
Good luck.
- Malaysia
A. Hi Gary,
I will agree with respect to Cheahs' advice on skipping step #5. But I am curious to find out why you don't add a acid copper flash to your parts. I also would suggest dummy plating your baths if your brightener level is too high and also to remove other metallic contamination. An out of whack P.H. level could also lead to your peeling problems.
One thing I am curious about is why you plate for so long in the cyanide copper bath. In my neck of the woods, cyanide cu. is used as a flash. It seems as if you are applying a great deal of copper or might your bath chemistry or tank setup need tweaking to provide a faster strike/plate.
Try these things and think about other things you may be taking for granted. Let us know what you come up with. It is always fun to hear how a great mystery is solved!
Good Luck!
Barrel Plater - Methuen, Massachusetts
2005
A. I do not see an electrolytic cleaner in your line! This is a must for good adhesion.
Why do you dry the parts in the middle of the preplating process? This is also no good for adhesion.
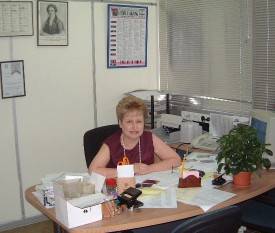

Sara Michaeli
Tel-Aviv-Yafo, Israel
2005
![]() |
Both the above replies make sense. I too don't understand why you use such a long time in the cyanide copper; all you need is about 5 microns to ensure total, non-porous coverage. I am not totally convinced about missing out the copper etch, especially if the post cyanide rinses are prolonged or the barrel is stored in a rinse tank whilst waiting for the nickel tank(s) to become free. Just a thought, perhaps the 10% sulfuric acid has become contaminated with something and you are getting an immersion deposit on the copper; obviously the immersion deposit would be very limited in its nature, what with copper being so low in the electrochemical series. Also, is it possible that the nickel barrel is being overloaded and you are getting quite severe contact failures? ![]() Trevor Crichton R&D practical scientist Chesham, Bucks, UK 2005 Q. Thank you, ![]() Gary Joseph Johannesburg, South Africa |
Q. Thank you all for your help.
We plate for a long period of time because the spec has called for
1-4 microns and we are getting 5 microns in that time.It might just be my way of thinking but I thought I would get better adhesion that way(I do not know if I am wrong or not).I have been advised to put a flash acid copper on but we do not have the facilities for that.
Why would you take out no 5 .. would it increase the chances of peeling? My supply house has recommended it and I just wanted to do everything they asked me to do.. but if you think it would HELP the problem I will remove it.
I dry the parts after the degreasing but we put it into the HCl afterwards to pickle and they are not dried after that.The peeling has been solved by 10% sulfuric before nickel plating. I now end up with the original problem of double plating. I have been told that the work is losing current during the plating process because of the shape and weight.
I have been advise by other platers and supply houses
1. To put heavier danglers in (done) no change
2. mix other articles into barrel (still testing)
3. wrap wire around the danglers and mash it into the
barrel to spread the current( will be done on Monday)
4. To make a spring shaped dangler to spread the current
(Thinking about it.)
The tank is plating perfectly on other parts , brass based and steel based. a Hull Cell
⇦ huh?
is done once a week and there is no contamination detected.
If I use dummy plates can I plate without brightener?
Many platers have battled with this job except one. he is not prepared to help.
All suggestions are needed (I have lost weeks of sleep over it ).
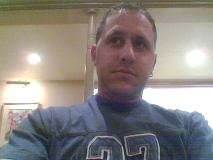
Gary Joseph
Johannesburg,
South Africa
Q. Hi, Trevor
I am getting about 5 microns in 30 minutes. What do you suggest ratio copper and cyanide levels to be to get a faster deposit and at what voltage. Is it true that 10 volts can cause the copper to become stressed?
I have been doodling on a piece of paper, a spring type dangler to help the loss of current that will start at on end and run through the barrel to the other end, I have a good feeling about this. Why would the normal danglers or overloading the barrel cause a loss in current? Does the current battle to travel across the entire work load in the barrel?
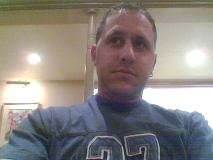
Gary Joseph
Johannesburg,
South Africa
2005
A. Hi Gary,
Have you ever considered a straight-rod dangler? Or maybe it might just be better to rack plate the work. Is this an option for you?
- Barrel Plater, Methuen Massachusetts
A. I think the reason large parts exhibit this peeling problem is that the current is in fact breaking. Mixing with smaller parts sounds like a very good idea if re-separating after plating isn't too much trouble.
The advantage of danglers is that they are one of the only kind of contacts that don't involve some sort of "brushes" for contact. By
"brushes" I don't mean hairy things, but a way of bringing power into a rotating part via a sliding contact. If the straight-rod contact that Michael suggests is stationary to the barrel hanger arms, rather than rotating with the barrel, it can be done without a brush arrangement, but I don't think it would solve the problem without danglers hanging from it, and this will probably lead to snarls.
Some shops do use arrangements with brushes but the barrels always need more maintenance than dangler style barrels. What might work along those lines is thin metal bars mounted on the 6 barrel ribs and running from one end of the barrel to the other, bolted to plates mounted on the barrel hubs; the hub plates do require a spring loaded brush arrangement in the hanger arm to supply the current. The barrel manufacturer I once was employed by made these a few times, including some repeat orders, so they worked well enough.
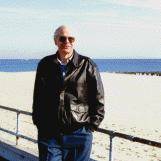
Ted Mooney, P.E.
Striving to live Aloha
(Ted can offer longterm or instant help)
finishing.com - Pine Beach, New Jersey
HI MICHAEL AND TED,
I have been advised to use a straight rod with plate like danglers down.
In the interim I have made a spring shaped dangler from one end to the other end of the barrel.The Spring is off center so it is in the lower half of the barrel.
I have plated one batch and it plated perfectly but it broke due to the turning of the barrel. I have asked them to modify it so that it would not turn but stay stationary in the lower half of the barrel all the time.
This will make sure the current is evenly spread out in the barrel (or so I hope)
Thank you for all the help and I will let you know of any advancements.
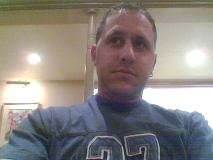
Gary Joseph
Johannesburg,
South Africa
A. Gary,
Whilst I am no expert at barrel plating and have only limited experience with barrel copper, I can say that a good "high speed" copper should be about 75 g/l copper cyanide with 133 g/l potassium cyanide. There should be about 40 g/l copper and 25-30 g/l free potassium cyanide. A barrel will take between 8-10 V when plating at about 0.4 - 0.6 A/dm2. In this case the bath should operate at about 55-65 °C. A new bath should have an efficiency of about 90%, but as it ages this will fall to between 50-70%. The efficiency can be improved by keeping the carbonate levels down. I have also heard, but never done it, that the efficiency can be increased by adding Rochelle salt (potassium sodium tartrate)
⇦ on
eBay
or
Amazon [affil link]
to the bath. This increases the throwing power of the bath, which usually decreases with both increased current density and copper concentration. You can also improve the bath's performance by "pulsing" the current - 8 seconds on followed by 2 seconds off; this will allow the current density to be almost doubled (so it is claimed!)
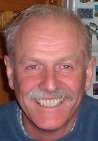
Trevor Crichton
R&D practical scientist
Chesham, Bucks, UK
Q. We are having peeling of nickel off acid copper in rack plating. We have Soak cleaner, electro, sulfuric acid, cyanide copper, sulfuric acid dragin to Acid copper, nickel and chrome.
We had peeling of acid copper off cyanide copper, added sulfuric drag in, problem solved. now nickel is peeling off acid copper.
On smaller parts no peeling. thickness of nickel is over 20 microns, on larger parts nickel thickness ave. 4 microns, peeling. rectifier self adjusts to load.
Any other thoughts of how to solve the problem?
- Durban, South Africa
May 20, 2010
A. Hi, Debbie. Well, the problem is obviously either with the acid copper or the nickel then.
I doubt that the nickel thickness is an issue because, if you have good adhesion, internal stresses, etc., shouldn't be a problem. As for the smaller parts, their adhesion could be from somewhat of a
"shrink wrap" effect. Depending on the substrate size and shape, it may be possible to smash a few, wrap some around a mandrel, or somehow really prove that the adhesion is better or it isn't.
If the adhesion truly is better on the smaller parts, then I would lean towards an electrical cause for the poor adhesion, like maybe the rectifier is periodically blinking off, causing a laminar nickel plating. If there actually is little difference in adhesion for the smaller parts, then it could be a chemical issue related to excessive and poorly rinsed brightener in your acid copper.
Regards,
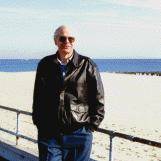
Ted Mooney, P.E.
Striving to live Aloha
(Ted can offer longterm or instant help)
finishing.com - Pine Beach, New Jersey
Q, A, or Comment on THIS thread -or- Start a NEW Thread