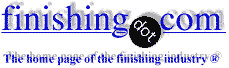
-----
Passivation of 303SS with Nitric Acid Q&A, Problems & Solutions
Q. We've just ran into an issue with passivating a job that we have ran for years. Literally thousands of parts without any issue previously. The material is 303 stainless per ASTM 582, condition A. the passivation requirement is QQ-P-35, 24 hour test not required. The result on our last batch of approximately 170 pcs was a dark etch like finish all over. We sent a 2nd batch to another passivate house and received similar results. The plating houses said there was a "sulfer type smell" during the process. We then sent the material out to a testing lab and it came back acceptable to the specification. Is there something we could be doing during the machining process that is causing this? we haven't changed our process in any way over the years, yet these are the results. Any ideas or suggestions? we just ordered replacement material from a different supplier, but now I'm not sure that it will make any difference.
Ken Gerhart- El Cajon
September 7, 2021
A. Ken,
This is a fairly common issue. 303 is a "free machining" high sulfur grade. Is it the sulfur causing the issue, but there is enough variability within the grade itself that some companies go for years without a problem, until there is a change in material source or production that is often undetected by the company's purchasing department.
Proper processing is important, i.e. using Type II/Nitric 1 if nitric acid is being used. A good alkaline/hydroxide pretreatment is generally useful to remove the surface sulfur prior to any method of passivation.
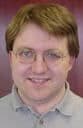
Ray Kremer
Stellar Solutions, Inc.

McHenry, Illinois
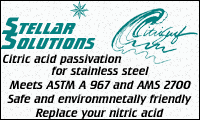
September 20, 2021
Ray,
Thank you for your insight. I will share this data with our plating house(s), and share any results or feedback I receive.
Thanks,
Kenny
Business Owner - El Cajon
September 20, 2021
⇩ Related postings, oldest first ⇩
Q. We have a machining supplier that has not followed the procedure on our drawing calling for sodium dichromate to be added to the nitric acid bath for passivating our 303 St Stl part. If sodium dichromate is left out of the bath, will this effect the corrosion resistance of the part?
Becky Stufft- Plymouth, Minnesota USA
2000
A. Sodium dichromate is an oxidizer that will enhance the passive oxide film that forms during the passivation process. The passive oxide film should be more stable when formed with sodium dichromate that for passivation with straight nitric acid, therefore absolute corrosion resistance should be better when the sodium dichromate is used. Whether it will be significant for your parts will depend on the component and the service application.
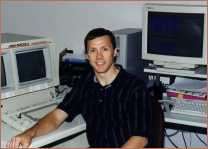
Larry Hanke
Minneapolis, Minnesota
2000
A. Becky:
For 303 stainless it can be critical to have the dichromate in nitric acid. It not only enhances the oxidation of the surface, but it can prevent problems with the surface of the steel turning dark.
adv.
You can also use products like CitriSurf 2250, which works well with 303SS without the problems of nitric acid.
Let us know if we can help.
Regards,
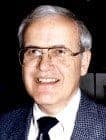

Lee Kremer
Stellar Solutions, Inc.

McHenry, Illinois
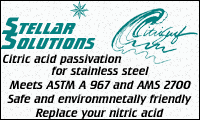
2000
Q. The passivation spec
AMSQQP35
[canceled] gives an option for PH materials of using type II or type VIII passivation. The type II uses sodium dichromate and a weaker solution of nitric acid. Type VIII uses only a stronger nitric acid solution for a longer time.
Is one method better than the other?
Thank you for the help,
- Valencia, California, USA
2001
----
Ed. note: We added your question to a thread where it's already answered, Jay. Good luck.
Multiple threads merged: please forgive chronology errors and repetition 🙂
Etching of 303 SST during Passivation
Q. I am a quality engineer assigned to the purchasing function of a OEM company. Recently we have been experiencing a, for lack of better terms, etching of parts during the passivation process. The material is 303 SST machined bar stock and it has happened on more than one occasion, with different parts, all the same supplier. The problem is not consistent and does not effect all the parts on a "load". Fallout has been anywhere from 20 to 50 percent of the lot. The appearance looks like the parts were actually sand blasted, extremely rough. Both inside and outside features have been affected.
The supplier has made the claim it is our (customer) issue. Needless to say we disagree.
Has anyone out there experienced the same issue? If so what was done to correct?
Thanks
OEM - MPLS, Minnesota, USA
2005
![]() |
A. Do a search of the letters at this site. There are a couple with lots of answers that cover nearly all of the possibilities. Are you using the correct passivation for 303? I will bet that it is 303Se or 303S and not plain 303. It makes a huge difference. James Watts- Navarre, Florida 2005 A. Erratic results during passivation of t303 is always a problem, and it happens just as you describe - a few parts in one lot, perhaps more or less parts in the next. The parts which are attacked are usually damaged beyond use, while other parts in the same lot may be fine. This is caused by sulfur added to make the T303 easier to machine. If you change to T304, the problem will go away. The price you pay is somewhat more difficult machining. ![]() Jeffrey Holmes, CEF Spartanburg, South Carolina 2005 A. By which method were the parts passivated? Nitric acid has a tendency to react with the sulfides added into 303 to ease machining. Once a reaction occurs a granular attack like you describe takes place. - San Jose 2005 |
Multiple threads merged: please forgive chronology errors and repetition 🙂
How do I remove sulfur smell after passivation of 303SS?
Is there a chemical or process for removing the sulfur smell after "gassing" has resulted from passivating (type 2) 303ss?
Tomas Mahar- Bainbridge, New York
2005
![]() |
A. 303 stainless steel contains sulfur and therefore sulfides. When treated in acid, the sulfides are decomposed to form sulfurous gases. To avoid the smell, try dipping the workpiece in dichromate; this will oxidise the sulfurous material and reduce the dichromate to trivalent chromium. ![]() Trevor Crichton R&D practical scientist Chesham, Bucks, UK 2005 A. You need to soak the parts in alkaline solution, preferably pH above 12. This should take care of it. ![]() ![]() Lee Kremer Stellar Solutions, Inc. ![]() McHenry, Illinois ![]() 2005 |
A. I agree with Lee, and would add that the alkaline cleaning stage should also be run before the acid stage to remove the sulfur and sulfides prior to passivation. Use of citric based passivation solutions in place of nitric acid will also help. Oxidation of the surface after passivation with hydrogen peroxide is a more environmentally friendly solution than chromates.
Daryl L. RollCosta Mesa, California, USA
2005
Multiple threads merged: please forgive chronology errors and repetition 🙂
Explanation for reaction of 303SS to nitric acid passivation?
Q. My question concerns an event that occurred about two years before I began working with this company so I only have a description based upon accounts for those I interviewed. I am investigating this because I'm a QA manager and need to ensure that this doesn't happen again.
The job consisted of small parts about three eighths dia. and an inch and a half long. The print only specified a 300 series stainless. The material we used was 303 Stainless Steel that was being passivated in a nitric acid bath. (I'm guessing a similar concentration to what it is now of about 20-40 percent nitric @ 70-90 degrees F)
When two or three parts were tested there were no problems, when a full tray of 20 pieces was processed however, it was reported that the acid began to bubble almost as if it were boiling, accompanied by the smell of sulfur and a black scum that formed on the surface of the tank. To me this sounded like a dangerous situation as the smell from the reaction probably contained some form of nitric oxides. When removed, the parts had turned black. Now, two years later the part I have from that incident is a dark grey covered with a rust colored oxidized layer. The pieces appear rather rough to the touch where they were initially machined smooth.
My question is what kind of reaction was taking place and did it present a danger to the people involved? My guess would be that the acid reacted with the sulfur and phosphorus content in the 303 grade SS but I'm not exactly sure what took place. There were no known contaminants and the specs on the steel were verified, a subsequent material from a different lot resulted in the same reaction. Since then, they have switched to 304 SS and have no problems with that.
My intent is to document the incident as part of a validation of the passivation process used here so that it can be understood what took place and avoid a repeat of similar issues.
Quality Assurance - Westbrook, Connecticut, USA
June 5, 2008
A. Hi, Vernon. Years ago a theory was well presented on this board that certain types of oils on the parts, and not fully removed, are the culprit. I believed the theory at the time it was presented, but I am more skeptical now because I haven't seen any supporting evidence from other readers over the years. But if two or three of your parts processed fine and then a larger batch presented a problem, I suppose it's possible that the larger quantity of parts, or some dirtier parts, introduced enough oil to cause this problem. Anyway, review the FAQ on Stainless Passivation and make of it what you will. I'd love to see someone put a drop of oil in a beaker [beakers on
eBay
or
Amazon [affil link] of nitric and see if it can wreck a part. Good luck.
Regards,
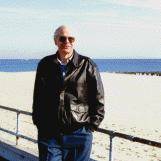
Ted Mooney, P.E.
Striving to live Aloha
(Ted can offer longterm or instant help)
finishing.com - Pine Beach, New Jersey
June 5, 2008
June 9, 2008
Thank you for directing me to the FAQ page. I found the explanation offered by Mitchell G. Lee of Robertshaw Controls to be particularly appropriate. I replicated his explanation; albeit on a far less technical scale, and was able to determine that the machining oil did indeed react with the nitric acid resulting in the symptoms reported to me. While I was already vaguely aware of this fact and had included a note about it in our documentation it was my investigation into this event which allowed me to put two and two together and determine that this experience we had was an actual example of the oil mixing with the nitric solution to create an organic acid and the resulting reaction.
It will now be included in our quality documentation so it can be avoided in the future.
Thank you for providing such a valuable forum for the industry.
- Westbrook, Connecticut, USA
Multiple threads merged: please forgive chronology errors and repetition 🙂
Type 2 or type 7 passivation for 303 stainless?
September 13, 2011Q. I have a question in regards to Passivation. I am using 303 Stainless
Steel for a small electrical connector housing that is machined. I wish
to have the housing passivated per QQ-P-35C.
I am a bit confused whether use Type 2 or Type 7. I understand
the difference is the Type 2 uses the sodium dichromate and Type 7 does not.
Can you offer up a suggestion which Type would be advantageous to 303 and why.
Designer - Illinois
A. Type II is recommended for 303 and other free machining stainless steels per QQ-P-35 and ASTM A967.

Jon Barrows, MSF, EHSSC
Kansas City
September 28, 2011
A. The grade vs. bath type chart in both QQ-P-35 and ASTM A967 recommends only one nitric bath type for 303: QQ-P-35 Type II / A 967 Nitric 1.
You may also want to add citric acid passivation per A 967 to your consideration.
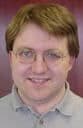
Ray Kremer
Stellar Solutions, Inc.

McHenry, Illinois
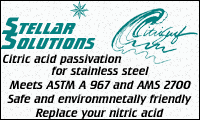
September 29, 2011

this text gets replaced with bannerText
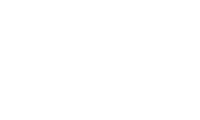
Q, A, or Comment on THIS thread -or- Start a NEW Thread