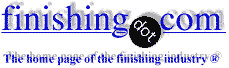
-----
Is acrylic Waterborne coating being over cured?
2005
Q. Hi Guys!
Being back to the finishing industry since a few months, I thought that you guys may help me to solve a problem that I've encountered last week.
I'm actually involved in the glass decorating industry. We are decorating and making organic coatings/finishing on glass packaging for cosmetics and alcoholic industries (principally glass bottles).
Actually I'm facing a problem with one of our acrylic waterborne organic coatings. We spray the coating on bottles and everything seems nice except for ... the color. The color seems to be yellowing during the curing process (reference color is some kind of green with a slight blue shade and turns out to a green yellow yellow after curing process). The difference after curing process is not major, but most of our clients are very demanding on the color exactness. I'm new here, but according to other employees, this is the first time they have such problem with an acrylic paint.
We've asked the paint manufacturer to adjust the paint color according to our specifications or to increase the pigment loading ... and nothing has really changed (the yellow shade was still present). Moreover, paint manufacturers aren't very inclined to reveal their formulation.
Could it be possible that our curing process is either too hot or too long (thus burning part of organic pigments)? Note: The curing process is executed according to manufacturer specifications. Perhaps the paint manufacturer is using cheap extenders? Does anyone have any yellowing problem with waterborne acrylic varnishes/paints?
I haven't made any tests or experiments yet, but I would like to have a second opinion to guide me in my future experiences.
Regards,
Sérigraphie Richford inc. - Pointe-Claire, Québec, Canada
A. An indication of overbake is that the color swings yellow. Have you put a sensor pack into your oven to check the temperature? What about lowering the temperature at different intervals on some test pieces to see if you can obtain the proper color, and then test the paint to see if it has retained it's mechanical properties. Your supplier isn't going to be too interested until you prove to him that it's his problem; if the paint is overbaking at his recommended cure cycle, then it's his problem.
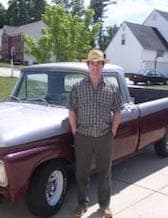
Sheldon Taylor
supply chain electronics
Wake Forest, North Carolina
2005
2005
A. Gidday mate from Aotearoa, the paint you are receiving may be metameric. I have worked extensively within the coatings industry for the past 13 years. I often rely on our colour matchers to achieve such yellows, and as a result you do appear to occasionally get a greenish/yellow. For example if you were making a yellow to another paint companies standard, you can prove that one or the other may be metameric by adjusting the lighting. Usually the colour may look yellow in UV , but with artificial light it may still appear yellow. This is solely related to the pigment the paint manufacturer you referred to is using. By changing the yellow pigment you may get the colour a lot closer. I hope this helps. |
Regan Okeefe
- Auckland, New Zealand
A. The manufacturer usually specifies a temperature for a time period. Is your product in a heat tunnel? If so, this may be your problem. The product may be heating for longer periods at different and inconsistent temperatures. Also, how well are you mixing your received product? Things to think about.
Patricia Amaro- Mexico City, Mexico
2005
Powder coating is too yellow
2007Q. Hi!
Sorry for bad English below! From Sweden!
I have a problem with curing a powder coated aluminum part, 3 mm thickness. I've set the oven's three zones as follows:
zone 1: 195 °C, zone 2: 195 °C, zone 3: 180 °C.
The parts have a run time through the oven of 25 minutes but it never exceeds 165 °C metal temp for more than 4 minutes. If we raise the temp we will have problems with the paint going too yellow, but the manufacturer of the powder requires 180 °C metal temp for at least 15 minutes or 200 °C for 10 minutes.
There is also this problem: When we run the Datapaq with one air gauge and three metal gauges, the gauge that's placed at the top of the part is the gauge that shows the lowest temp in the Datapaq. I've heard that the yellowness in the paint can appear when the ventilation of the oven is bad, and is it possible that the circulation in the oven is bad and therefore we do get the lowest temp at the top of the parts? I would be happy if someone could help me to sort out these problems and explain what to do!
Regards,
Micael
Paintline worker - Jonkoping, Smaland, Sweden
A. Dear Micael,
You do not inform us whether the aluminium powder coated items, once baked, meet the demands of your customers. If they do - then why worry? You could test for the adhesion of the powder to the aluminium by applying a cross hatch followed by tape. If it sticks, then it is okay. As a supplier of powder coating materials we, like all other mfgrs., test the material on 6 x 4 panels under ideal conditions. Our technical data sheets specify certain parameters at which we would like our powders to be cured/baked. I would suggest that not all users will or can adhere to that. Example: The alloy wheel mfgr., 40 mins minimum at 210 °C or keg mfgr. 165 °C for 14 mins. There are many more examples but, if at the inspection point the powder does not crack, has good adhesion with the correct gloss and colour -- forget what the mfgr. tells you. If what comes off the line has no defects continue as you are.
Birmingham, United Kingdom
2007
A. Dear Micael,
I will attempt my best for the limited information you provided. This could be a pretreatment issue but I will assume for the sake of this discussion it is an oven or powder issue. I do not know if this oven is convection or not.
First, you need to provide the temperature that the powder manufacturer recommends. You have not explained if every color yellows or if it is whites or clears. You said the Datapaq indicates you have a lower temperature than the other two probes. Does your color change from top to bottom also? I do not know if your oven is bottom, side or topflow, but you should have even air distribution within your oven to achieve even coatings. Remember that the sole purpose of your oven is to cause a chemical reaction of the powder. The proper amount of heat at a given time insures that the desired decorative, chemical, and mechanical properties are realized.
A powder coat convection oven should be able to exhaust the entire oven air volume several times per hour (typically exhausting 10 times minimally per hour).
Your oven should have some means to keep the heat contained within the oven via an air-curtain, etc. Once you dial in your oven to achieve the proper temperatures and can maintain them, you should try different powder manufacturers to see if you're having the same problems with yellowing with their products. You can also ask your powder supplier to provide their own in-house testing to see if they see the same reactions you are seeing.
![]() Bob Utech Benson, Minnesota |
![]() Ed. note: Bob is the author of: "High Performance powder Coating" on eBay or AbeBooks or Amazon [affil link] |
2007
Q. Hi, and thank you for trying to answer my questions.
I will try to give you some more information on this issue.
Our oven has three gas burners. I don't know if this is a convection or not? The mfgr. asks for 180 °C metal temp for 15 minutes or 200 °C for 10 minutes. And all our powder get too yellowish. And one more strange thing, the cured paint also gets lighter, shouldn't it get darker if it was over-cured? So it gets both too yellow and too light.
Is it possible that the air temperature in the oven gets up too quick and therefore it affects the powder too much before the metal temp is up to what the mfgr. asks for? The oven is a sideflow. I am not sure if the yellowish changes from top to bottom because it can differ on the top at different sides. If you understand my English I'd be happy for more advise. I will send sample powder to mfgr. and ask him to cure it in their oven and see if it differs.
Best Regards
Micael
- Jonkoping, Smaland, Sweden
A. Micael,
Your oven temperatures are average and are okay. Generally speaking, you should bring your topcoat temperature up rapidly because powder tends to flow better and quicker which helps to give a nice cosmetic finish. I have seen a few ovens that have their burners flaming directly into the oven, which could affect the outcome of the finish though I doubt you have this issue. If you had this issue, it would definitely show up when you ran an oven profile. I would like to know if you have ran any tests such as a cross-hatch test, mandrel bend, and M.E.K. test? Do you have only one powder supplier and if not, do your other powder suppliers have this same issue?
![]() Bob Utech Benson, Minnesota |
![]() Ed. note: Bob is the author of: "High Performance powder Coating" on eBay or AbeBooks or Amazon [affil link] |
Q. Hello again and thanks for the answers.
Bob, first, thank you for answering. You wrote that if the burners were flaming directly into the oven I could affect the outcome of the finish, how exactly would that show up on the oven profile? We have done some cross-hatch test and they turned out great. None of the other test has been carried out. We use only one powder supplier and the problem is the same on any color. Is there anyone who have had these problems with the paint going yellow and lighter at the same time? And if what did you find out about what caused it.
Regards
Micael
- Jonkoping, Smaland, Sweden
2007
A. Micael,
If your oven has a direct heat fired doghouse, you may or may not see a discernible observation on a recorder. If the conveyor runs directly in front of the flame and is close enough, you will see a noticeable rise on the data recorder. If the flame is far enough away, you will not.
My guess is the powder is your culprit. You need to get powder from a different supplier and run it through your system. I would bet you will not see the same yellowing. Sometimes powder supply companies use a poorer grade of filler in their powder in order to save them and you money and you end up with this result. If you don't complain, they keep sending you the same powder. You owe it to them to check this out.
I am concerned because you stated you were going to ask the powder supplier to cure some panels in their laboratory and it sounds as though this has not happened. When you don't initiate corrective practices, it sends messages to the entire industry that there are problems associated with powder coating, when really, these are easily solved issues.
![]() Bob Utech Benson, Minnesota |
![]() Ed. note: Bob is the author of: "High Performance powder Coating" on eBay or AbeBooks or Amazon [affil link] |
Pearl white paint turns yellow after 6 months
Q. Why does paint go yellow? This problem occurs within 6 months after painting. This problem comes only with pearl white shade (means three coat system).
Please provide solution immediately.
employee - India
September 22, 2014
Q. I am powder coating yellow and I put it in the oven at 420 for 10 minutes and it is coming out orange. Is this because I'm cooking it too long?
don bender- rock falls, Illinois
January 23, 2018
A. The powder consumable you are using will have a manufacturer recommended cure schedule.
That will be a time at METAL TEMPERATURE not a time at oven air temperature.
To accurately assess your compliance with manufacturer recommended cure schedule you will need to have a thermal data logger to regularly check your compliance with manufacturer specs. Without such a checking mechanism you are "flying blind".
It certainly sounds like overbake or burn but why not just get a bit professional and ensure that you do it right first time every time?
Hope this helps.
Regards,
Bill
trainer - salamander bay
A. I agree with Bill, it sounds like over cure -- the most common cause of yellowing.
Start with powder maker's recommendation, then check that you get this. It's a time and temp thing, and metal temp, not air temp inside the oven. For many applications under 200 °C is desirable to adjust time to suit. You'll need a recording set of thermocouples that you place in the oven to see the temp/time curve for different thicknesses of steel in different parts of the oven.
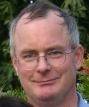
Geoff Crowley
Crithwood Ltd.
Westfield, Scotland, UK
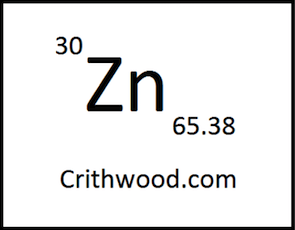
May 4, 2018
Q, A, or Comment on THIS thread -or- Start a NEW Thread