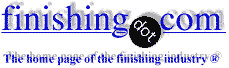
-----
Difference between Bright Tin and Matte Tin Plating?
In the old days and among traditionalists, tin plating was generally considered to be one of two types:
• Alkaline tin plating (sodium stannate or potassium stannate) for matte deposits
• Acid tin plating (tin sulphate) for bright deposits
So be aware that people will sometimes sling the slang of 'matte' to indicate 'alkaline processes' & vice-versa, or 'bright' to indicate 'acid processes' & vice versa -- even though these days people sometimes do what they consider bright plating from an alkaline bath, or matte plating from an acid bath, and there is a third type, MSA, as well :-)
Q. Difference between Bright Tin and Matte Tin?
We are a job shop plater and we have a bright acid tin process, now a Client wants Matte Tin only.
He doesn't know why, only that the drawings call for it.
What differences does these deposits have, besides appearance, in respect to conductivity, solderability, corrosion resistance, etc. and why would a manufacturer specify this particular finish?
In regards to the process we use a Bright (proprietary) acid bath with Stannous sulphate, Sulfuric Acid and additives. What would be the process difference if we want to to supply matte tin? Is this an acid process or alkaline one?
The parts are for electric component use.
Thanks for your help,
Job shop plater - Monterrey, NL, Mexico
2005
A. To achieve a matte finishing you would have to operate a alkaline bath , usually a sodium or potassium stannate bath; the conductive salts would be NaOH FOR THE SODIUM STANNATE OR KOH FOR THE POTASSIUM STANNATE .
But it's possible to achieve a bright finishing using these baths too, if you use a less concentrated solution of these stannate baths (sodium stannate- 9,33 gr/lt NaOH - 2,0 gr/lt) stainless steel anodes 72 °C, and if you plate over a flash of iron gold for approximately 45 seconds you will get a color similar to platinum or rhodium.
- caxias do sul, rs, Brasil
A. Bright tin--melted finish. Matte tin--unmelted finish. Unmelted mainly used for drawing applications (tin provides the lubrication for drawing). Melted (bright) mainly for appearance.
Ian Hunter- Gary, Indiana
A. Alkaline tin is the finishing that you want.
The formula that you need is the follow:
Potassium stannate 100 gr/lt for rack 200 gr/lt barrel
tin 40 gr/lt 80 gr/lt
Free potassium hydroxide 15 gr/lt 23 gr/lt
Temperature 80 to 85 C
Voltage 4 - 8 4 - 14
anodes pure tin
I hope this helps you.
Regards
- Toluca, Mexico
A. There are matte tin baths using proprietary additives designed to function with acid sulphate or MSA based electrolytes. The advantage of these over the alkaline processes is much greater rate of deposition and improved distribution.
I have successfully installed these for both barrel and rack operation.
The matte processes are not the same as running a bright process without additives. If you try to do that, you will not get the grain refining and therefore get porous, rough deposits.
process supplier - Great Neck, New York
A. Hi Enrique,
I am currently running a matte tin process with the same components as your bath. I switched from bright to matte to make it easier to buff (mine is strictly a decorative plate). One of the advertisers on this site (EPI / Electrochemical Products Inc. [a finishing.com supporting advertiser] E-Brite 180/181) has a system that was a direct conversion, I just changed one of the additives. It works fine for me, but my application is different. You might try giving them a call for specific information.
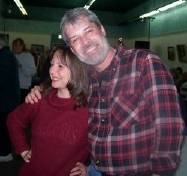
Trent Kaufman
electroplater - Galva, Illinois
A. You can plate matte tin using MSA-based chemistry.
You mentioned that the parts are for electrical components.
Could there be a concern with whiskers growing and shorting the parts?
Bright tin has been blamed for whiskering, and it is being avoided in some electrical applications.
Matte tin is supposed to have less stresses compared to bright tin, and it has less tendency to whisker.
- San Jose, California
A. Hi there,
there is a lot of difference when a drawing says matte tin. Often use tin for an electric application; and with a matte tin will get a better current distribution than bright tin in contact with another matte tin plated parts than bright tin plated parts.
Regards
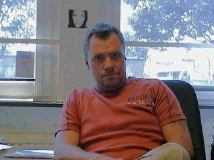
Anders Sundman
4th Generation Surface Engineering
Consultant - Arvika,
Sweden
A. Hi Enrique,
The client wants a Matte Tin process because Bright tin is known to cause Tin Whiskers that may short the electrical contacts of the component over a period of time.
Tin Whisker is known to cause the failure of at least one satellite in orbit.
nepp.nasa.gov/WHISKER/background/index.htm
Google tin whisker , you will find more data on it.
- San Jose
Q. Hello sir,
I am a production engineer in a electroplating company, and we specialize in specification plating on reel to reel parts which are mostly pins and carrier on either side in strip form.
One of our products requires overall Ni-plating of X-microns and Tin at a specific distance from one end of carrier and Gold at a certain defined distance with thickness X-microns respectively on these pins.We can run the same product on two machine lines with some minor changes in set-up of the respective Cells used for plating different metals on the strip.
When this product is run on Machine line-1 with speed Y rpm, z-current applied to Tin cell, which requires plating only at a certain distance and with a defined spread; the parameters observed are precise good and acceptable, and this Machine line only employs Matte-Tin bath.When the same product is run on machine line-2, with the same Tin cell used for specific plating in line 1 is used in line 2, the spread is observed to be more and not precise. This machine line-2 employs two types of Tin bath viz. matte tin and Bright Tin, and these baths use same cell as in Machine Line-1.
My question is why is this variation observed in different lines on the same product when all the parameters such as Temp, pH, Speed and even the Cell used are same.\
Would this be due to that line-1 uses only Matte-Tin Bath and has no contamination with Bright Tin bath as in Line-2?
Please suggest and share your vast experience on this issue.
Thank you
Production Engineer - Bengaluru, Karnataka, India
February 15, 2010
A. Hi Cyril. Thank you for your effort in describing your situation, but unfortunately I still don't understand what you are trying to describe. Are you saying that line 2 has the identical chemistry as line 1, but it also has an unused bright tin step? You are able to adjust rollers and threading such that the strip never enters that bright tin tank?
Luck & Regards,
Ted Mooney, P.E.
Striving to live Aloha
(Ted can offer longterm or instant help)
finishing.com - Pine Beach, New Jersey
How to decide if tin plating is semi-bright vs. matte
Q. I have a question. We have a Sn plating line that is plating matte appearance, but now our customer claims that it is semi bright. As far as I know, "matte" is a dispersing light mode of appearance. Can matte vs. semi-bright be measured?
And can someone help me describe what is the true determination of matte and semi-bright.
R & D plating Eng. - Senawang, KL, Malaysia
May 3, 2012
A. Hello,
A matte tin finish will not reflect any light, whereas a semi bright finish will. A matte finish will also appear white, semi bright will have a grayish hue to it. I don't know of any instrument that will measure the difference. If this continues to be an issue you should contact your chemical supplier to see if there are additives you should be adding on a regular basis. I have experienced this problem before and it was due to high stannic tin, and copper contamination. Once we addressed these issues our deposit returned to the Matte finish the bath was designed to plate.
Engineering - Mesa, Arizona, USA
A. Hi Seven Foot. To some people "matte" tin means alkaline tin (sodium stannate or potassium stannate). That is the chemistry Mark is commenting on. Are you using a potassium stannate process or something else?
Luck & Regards,
Ted Mooney, P.E. RET
Striving to live Aloha
(Ted can offer longterm or instant help)
finishing.com - Pine Beach, New Jersey
Stannate Plating on pewter charms
Q. Dam Good Stuff, Inc. is a social enterprise that promotes Fair Trade and sustainable income. We design and handcraft fashion jewelry for the export market.
We are having great difficulty having custom charms and jewelry components made of non-precious metals that meet the requirements with respect to metal content (lead, nickel, and cadmium) for our customers in the United States and the European Union.
We are currently working with a local supplier that is making products of tin and plating them with copper, silver plating, and antique silver, finished with a lacquer spray. The basic charms are fine, but we don't care for the look of the plating. Previously, we had a supplier that made pewter charms with what they referred to as "stannate plating." We liked this look, as it was more of a matte finish and does not seem to tarnish. Plus, it did not have the copper layer in between the base pewter base and the top plating, so when the plating wore off it didn't look like copper.
In discussing plating techniques with local suppliers here in the Philippines, I was told that the copper plating is put on first so that the final plating will be shiny.
We don't particularly want shiny and we hate how our jewelry looks when the plating wears off the the copper layer, we would like to eliminate the copper lawyer.
My questions are as follows:
1. What is the technical name for "stannate" plating that can be used to plate tin alloys?
2. What alternative plating would you suggest be used tp get rid of the copper issue and yet still meet the requirements of no nickel, lead, or cadmium?
Any help or suggestions you can provide would be greatly appreciated.
Managing Director of Social Enterprise - Makati City, NCR, Philippines
March 30, 2015
A. "Stannate" refers to a common plating bath for tin plating. With proper precleaning and preparation, it can be used to apply tin directly on your objects, and the luster can be adjusted by the plater from completely dull and flat to reflective bright.
However this may require the plater to install a tin plating bath especially for you as his present customers may want a different brightness.
Discuss this with any shop which does tin plating.
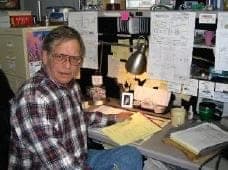
Jeffrey Holmes, CEF
Spartanburg, South Carolina
Q. Thank you all for the beneficial comments. I have two questions about matte tin plating with the formula Gabriel Ramirez gave.
1) What would be the approx. gloss value with this formula on a rack plated item?
2) What should we use as free tin to make the tin value 40 gr/lt?
Best Regards,
- Izmir,TURKEY
September 24, 2019
A. Hi Mert. Sorry, I don't know the gloss value of matte tin but it's supposed to be very far from glossy :-)
The tin content can be adjusted with additions of potassium stannate or sodium stannate (depending on which salt is the basis for your bath).
Luck & Regards,
Ted Mooney, P.E. RET
Striving to live Aloha
(Ted can offer longterm or instant help)
finishing.com - Pine Beach, New Jersey
• Topic 40850 "Bright Tin Plating vs. Matte Tin Plating"
adv.: Supplier of Copper Anodes, Nickel Anodes, Bismuth Metal, & Other Metal Products for Industry & The Arts
Q, A, or Comment on THIS thread -or- Start a NEW Thread