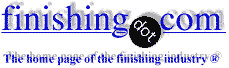
-----
Partially Sealing Sulfuric Anodize - Sodium and/or Potassium Dichromate
2005
There have been several postings about the differences between sealing anodized surfaces with either Potassium or Sodium Dichromate. However, it appears that no one has addressed PARTIALLY sealing an anodized surface. My company currently partially seals sulfuric anodized surfaces to increase primer grip prior to painting the surface. To my understanding, partially sealing is the best way to have good paint efficiency. To the best of my knowledge, partially sealing with Potassium Dichromate is done by utilizing the same process as fully sealing the surface (i.e. immersing part in Potassium Dichromate solution for 20 min.), except partially sealing is done at a lower temperature. Currently, we partially seal using Potassium Dichromate at 176 degrees F, where a full seal would run at around 210 degrees F.
My question is this:
We would like to begin partially sealing sulfuric anodized parts using Sodium Dichromate instead of Potassium Dichromate. What would the appropriate temperature be to partially seal surfaces using Sodium Dichromate to an equivalent amount as our current Potassium Dichromate process, and how would this temperature be determined/arrived upon.
Repair Process Engineer - Atlanta, GA, USA
My best guess is to use the same temperatrue that seems to work with the Potassium.
How do you know that you are only "partial sealing"?
The complete scientific work has not been done yet. If you want to do it you probably need an impedence meter instrument like the old Twin City Testing Company "Z-Scope".I sold only one back in the 60's to Anaconda in Fulton Industrial Park. Find out who bought Twin City and get some information on the use of impedence measurements to determine the degree of "sealability". There is an ASTM specification on this subject.
Then report back to us a technical paper as to your findings.
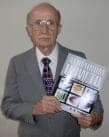
Robert H Probert
Robert H Probert Technical Services

Garner, North Carolina
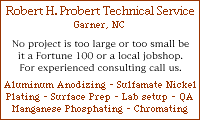
2005
Q, A, or Comment on THIS thread -or- Start a NEW Thread