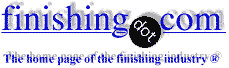
-----
Hydrogen embrittlement problems in Type III Hard Anodize
Q. We currently have a part which is machined from 7075-T651, and which is being anodized per Type III hard anodize, black in color. The part has a cross-sectional minimal thickness of .100".
The problem we are having just recently with our anodizing vendor is the parts have begun failing due to cracking. The part is subjected to 95 in/lbs. of force, and they are now failing due to breaking in half. The parts are extremely brittle, whereas before we had no issue with such problems.
It should be noted that the part in question would withstand 325 in/lbs. before failure, prior to coating.
Any help and/or insight would be greatly appreciated.
Manufacture - Oregon
2005
A. I wouldn't be so sure that the problem is hydrogen embrittlement; anodizing exposes aluminum to oxygen rather than hydrogen. But hard anodizing is a very brittle coating, and fairly thick. If it was .002" on each side, it could have a serious effect on the strength of the material, expecially its fatigue strength. If the shop had tried to anodize the parts unsuccessfully, stripped the coating, and anodized again, the strength reduction could be even more serious.
First, I would suggest making sure that both vendors used the same anodizing thickness. Second, I'd make sure they didn't strip and re-anodize. And third, I'd talk to the engineer; when a part requires strength, hard anodizing is usually not a good coating option.
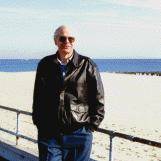
Ted Mooney, P.E.
Striving to live Aloha
(Ted can offer longterm or instant help)
finishing.com - Pine Beach, New Jersey
2005
A. A .002" hardcoat anodize would consume .001" of material from each side or a total of .002" from a cross section. This would reduce your total tensile strength by .002/.100 or 2%. However, hardcoating significantly reduces fatigue strength.
Chris Jurey, Past-President IHAALuke Engineering & Mfg. Co. Inc.

Wadsworth, Ohio
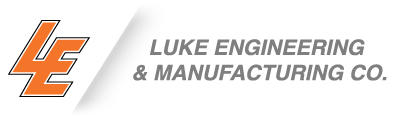
2005
A. Bending stresses are inversely proportional to the square of the thickness rather than the thickness, so it's about a 4% reduction. And if stripped and re-anodized, about 8% reduction, but I'd certainly agree that we're not anywhere close to accounting for the reported 70 percent drop in strength.
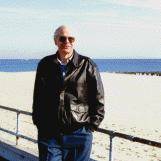
Ted Mooney, P.E.
Striving to live Aloha
(Ted can offer longterm or instant help)
finishing.com - Pine Beach, New Jersey
2005
Q. The reduction in strength mentioned here is right in line with the specs provided by our engineering department.
Our engineering strong points are in mechanical engineering and not in post-processing coatings, however it seems all agree on this side that something doesn't completely add up.
I have personally taken a part this week, before anodizing and used it in the assembly and subjected the part to 315 in/lbs., in which the part eventually flexed and caused permanent distortion of approximately .006", however not breaking or fracturing.
Performing the same test with one of our anodized parts, the part took 69 in/lbs., and then snapped in half. It breaks just like a piece of glass. The exact same part previously, before the change with our anodizer took 315 in/lbs. without any signs of failure or fracture.
Manufacture - Oregon
2005
Q. We are a small anodizing shop that has been in business for over 40 years. Recently our hard anodize (type III) has been getting rejected by our customers due to cracking where the hardware is being installed. What would cause this?
K. James- Redwood City, California, USA
July 9, 2013
A. The coating is aluminum oxide, it is "hard", you squeeze a nut down on it, then it will certainly "crack". The tendency to crack under such pressure is a function of alloy (you did not say), thickness (you did not say), whether work hardened by forging or machining, free acid, current density, temperature. Please come back to us with some information.
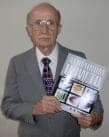
Robert H Probert
Robert H Probert Technical Services

Garner, North Carolina
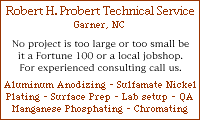
July 12, 2013
A. Are there threaded holes that are being coated? If so, that could be the main problem. If the customer comes along and installs a screw into a coated hole there is a good chance of cracking. It's best to not coat threaded holes if the customer can allow it.
One thing to check is the condition of the bath and also the processing conditions. With the hot weather we had, it's possible that the parameters were changed unless your facility is tightly controlled in terms of a/c. If the bath is in bad shape and a lot of additives are being put in, perhaps even without the knowledge of a supervisor or manager, the coating could crack as a result. Another problem is if too high of a current is used or if poor contact is made. There are several additives that will tend to plate quickly if a high current is used and then later you can see cracking and other defects, particularly if the item in questions is subjected to a load. If you have poor or intermittent contact, that will tend to drive additives to plate more quickly.
I would plan on doing testing in-house before shipping any more parts. Find out exactly how the parts are failing and get everything you need to do the testing there at your facility. If the parts pass your tests but the customer still complains, it could be that the customer is using excessive force due to a new employee or for whatever reason.
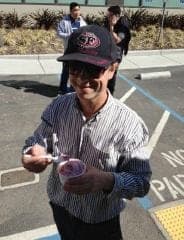
Blake Kneedler
Feather Hollow Eng. - Stockton, California
July 16, 2013
Q, A, or Comment on THIS thread -or- Start a NEW Thread