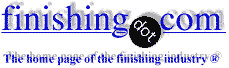
-----
Silver Plating Problems on Lead Frames
Q. I have been in the lead frame plating industry as a plating engineer for 6 months. One of the problems I always encounter is uneven Ag plating (spot Ag plating). What is causing the problem? Is it coming from the anti immersion bath?
Another thing is the "Ag Oxidation". I found the problem tends to happen when we're using higher duty cycle (90%, 70%, etc.) and solve by lowering the duty cycle. Also, especially when we're using copper olin 7025, the problem could come anytime no matter what pulse we use. Could anyone explain what is the mechanism that is causing the problem?
Thanks in advance.
deen
Md. DeenPenang, Malaysia
1999
A. Hi Deen,
how often you change your anti-immersion? And how many stages is your anti-immersion?
Anti immersion could contribute to unevenness. It might drag the contaminant into the Ag bath.
- Penang
2006
A. The anti-immersion process on Cu base material before Ag plating that inactivation of Cu surface and almost solution content Ag ionic and cover on Cu material surface to prevent Cu immersion to Ag plating solution as one of contamination prevention.
C C Chen- KaoHsiung, Taiwan ROC
2006
Q. I am facing uneven plating like as Mr Deen.
We purely use copper material, we use brighteners, we use anti-immersion chemical with proper control to avoid the chemical dragout to Ag bath. We also use 1 ms on and 2 ms off plating pulse with 800 to 1200 ASD current density.
We have studied on current distribution cables to verify it resistant.
All seems okay
We still encounter the uneven Ag plating.
- Singapore
February 8, 2012
February 10, 2012
A. Hi AH, Deen,
Possible causes of uneven Ag plating are:
1. Inadequate of surface active agent (conditioner) to enhance Ag deposit uniformity at high current density.
2. Inappropriate/inadequate solution flow from sparger/nozzle.
3. Improper anode-to-cathode ratio and/or too short anode-to-cathode distance.
4. Metallic or organic contamination.
5. Poor pretreatment (water break) prior Ag plating.
6. High free cyanide in Ag bath.
Regards,
David
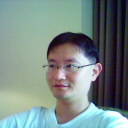
David Shiu
- Singapore
Q. Hi, I am working in electroplating copper lead frames company. Recently, I found a quality issue on my product. The lead frame is selective silver plating. There is some tiny brownish spot on the Ag plating area. After sent samples for EDX analysis, results shows that there are chloride,oxygen,copper on the Ag surface. The plating process is degreasing -> acid dip -> Ag strike -> pre-dip -> Ag plate -> Ag stripper .
I have no ideas where the chloride and oxygen come from since there is no any chemical contains chloride and oxygen used in the production line.
Do you have any ideas?
plating process engineer - Singapore
November 16, 2016
? Hello Ky, can I ask you why there is a pre-dip between Ag strike and Ag plate? What are the constituents of that pre-dip?
Mark BakerProcess Engineering - Phoenix, Arizona USA
November 21, 2016
Pinhole in silver plating on etched copper leadframe
Q. Hi All
We now having unplated Ag on pad surface. What is recommended action to be done? "Unplated" meaning one small hole or void on plated surface which is exposing base Cu material. Thanks you.
- Melaka, Malaysia
December 28, 2017
A. Hi Aris,
The void could be due to air bubble sticking on Cu surface, improper Cu descaling prior to Ag plating, Ag anti-immersion parameter out of control (if you use Ag anti-immersion predip before Ag plating), etc.
You might share "void" photo for better comment.
Regards,
David
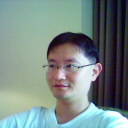
David Shiu
- Singapore
January 17, 2018
Q, A, or Comment on THIS thread -or- Start a NEW Thread