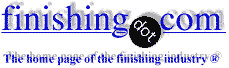
-----
Electropolishing of cobalt alloy medical device
2005
Hi All
I am a student involved in a research project in conjunction with a medical device company trying to develop an electropolishing process for small tubular medical implants made from a cobalt-chromium alloy, and have a number of questions that I hope you experts can help me out with! I use an electrolyte consisting of 85% phosphoric acid and glycerol, voltage control at around 7V, temperature around 70°C, mild mechanical agitation.
1. I have heard, and have some limited experience that electrolyte age affects polishing quality, and would like to monitor this. Which is the best method (and most common and reliable economical industry practices?): pH, conductivity, titration for specific elements, specific gravity, viscosity, amp hours? My electrolyte will typically go from clear to green to black.
2. Many of my problems occur at the contact between the anode rack (I have used various geometries including plates and rods of both 316L and titanium at different times) and the product (which is entirely submerged). If the product is stationary it creates wave-like ripples at the contacted surface. If I continually rotate the contact I frequently get "volcano"-like features ("hills" with a burst-blister appearance in the centre, although they are sometimes irregular). Intermittant conact provides a combination of the two. Any suggestions for avoiding these features, or an explanation for the volcanoes? I can't lower voltage if all else stays the same because I am very near the etching region as it is.
3. The edges of the product frequently get attacked and have a bread-knife type pattern I have called mouse-bites (although these are smooth features, unaccompanied by pitting or etching). Increasing the temperature and voltage to 90°C and 10V improves this to some degree but creates other problems like pitting and localised attacks. Does anyone know why this happens and have a solution for it? It also typically occurs on the surface at which contact is made.
I would appreciate any help with any of the questions.
Engineer - Cape Town, South Africa
Try 75% commercial phosphoric acid (the 85% grade), 25% conc sulfuric acid, 100F, 50-100 asf, copper contacts ( tight), control metal below 3% wt in solution, specific gravity 1.7+, no intentional agitation.
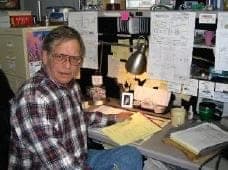
Jeffrey Holmes, CEF
Spartanburg, South Carolina
2005
2005
I am not as experienced to be called "an expert" at least not in this alloy, but I humbly offer you the following comments,
Good anodic electrical contacts is critical. Titanium or Stainless steel are not very good conductors for this task. Maybe you should try copper just as Mr. Holmes recommends. However you hear very worried about the bath metal content (Some copper will dissolve). I wonder if anybody have tried gold or platinum contacts. These might be noble enough to avoid its dissolution. Most of your problems sound like you have to improve electrical connections. Anyway, please keep us informed on how you solved the problem.
Regarding volcanoes, I wonder if they are what is so-called "Bull's eyes" which are caused by gas bubbles... The wave-like ripples sounds like also be caused by gas bubbles, which deteriorates the diffusion layer in its path when ascending to the surface. Bad electrical contacts also sometimes cause excessive gassing.
You don't mention anything the times you used... Sometimes increasing current-density/Voltage and decreasing time helps.
The quality of the raw material also plays some role. There might be metallurgical differences regarding the direction in which the metal was either cast, annealed, machined or mechanically formed. Metal grains and inclusions can be of different composition/size/shape in certain zones of the part and it manifest as irregular finishing during electropolishing, specially at the edges. I am not telling you this is the case, but you should check this, just in case.
Finally, the preparation technique of part before electropolishing is a commonly overlooked aspect. Are there pre-finishing steps, like sanding or buffing? Do not think that electropolishing will clean the part. Extensive cleaning, descaling and careful handling must be done on the part, not just a simple detergent immersion. Check your alloy chemical compatibility with strong acid/alkaline cleaners. Handle parts with clean, intert, and powder free gloves or handlers. Avoid any grease and dirt, even that form the skin. Certain contaminating particles cause polarization in the surface during electropolishing such as the abrasives from previous work, rendering pitting, deformities or excessive gassing (Gas bubbles).
I wish you good luck and keep us informed on your findings.
- Hermosillo, Son. Mex
Q, A, or Comment on THIS thread -or- Start a NEW Thread