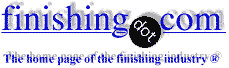
-----
Coating advice for Steel Hardware on Snowboard Bindings
2005
Q. Hello all,
I am new to the board, and am having a difficult time digging up some information for a project I am working on. Any help is greatly appreciated.
We are currently using SS hardware on our snowboard bindings. (salty, wet, physically abusive environment) We would like to switch to carbon steel for cost savings. I was hoping I could get some advice on coatings that would work well for abrasion and corrosion resistance. So far I have these in mind...which would work best, and are there any that I have missed? We are looking for a black finish, and a chrome style finish.
TIN, TYPE II - Hot-dipped
ELECTROLESS NICKEL, AMS2404 CLASS 1 - As plated, no subsequent heat treatment CLASS 2 - Heat treated to obtain required hardness
CADMIUM, TYPE II - With supplementary chromate treatment
The only suitable testing I can find is ASTM B117. I am unable to actually find the specifics of this test online, and this test doesn't seem to test for abrasion as well as corrosion resistance. Would anyone be able to point me in the direction of a testing procedure that might work for me? (If you could forward the specifics I would be eternally grateful)
Thanks again for any/all help!
Sports equipment - Cerritos, California, USA
A. Many years ago analysts used to proudly offer their advice that if GM could save 1/10 of a cent on 10,000 fasteners in 5 million cars they'd save $50 million dollars annually. In the long run that thinking cost GM their century of leadership in the auto industry, and allowed the Japanese manufacturers to become the leaders :-)
Although electroless nickel would probably be the best plating, in this rough, abrasive, service I doubt that any plating will prove fully satisfactory in the long run. Further, I suspect that electroless nickel will save you no money. Cadmium is a cumulative poison that should only be used when it's indispensable, and snowboarding isn't.
ASTM B117will cost you about $40 to download. There are abrasion tests, and electroless nickel will outperform most other plating in them, but what is a realistic abrasion 'rating' to shoot for when you are dealing not with predictable 'wear' but a variable amount of scratching against unpredictables like gravel, other bindings, asphalt, etc.? Good luck.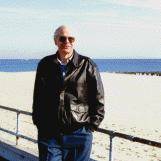
Ted Mooney, P.E.
Striving to live Aloha
(Ted can offer longterm or instant help)
finishing.com - Pine Beach, New Jersey
2005
Q. Thanks for your response. The physically abusive environment that I am speaking of is primarily a result of tightening/loosening the hardware to make adjustments. Most other wear (from hitting trees, other riders, etc) will have to be acceptable. Would there be any abrasion testing standards out there that might mimic this?
Cordell P [last name deleted for privacy by Editor]- Cerritos, California, USA
2005
A. Hi again, Cordell. Look up 'Taber Abrader' or 'Taber Abrasion Test'. This is a wear testing device appropriate for testing the wear resistance of plated parts. Good luck.
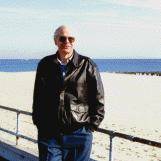
Ted Mooney, P.E.
Striving to live Aloha
(Ted can offer longterm or instant help)
finishing.com - Pine Beach, New Jersey
Well I am a very serious skier (social racer) and not a boarder but I think you should forget about trying to save money in this area.
Otherwise please advise the name of the bindings so I may suggest to my associates what not to buy.
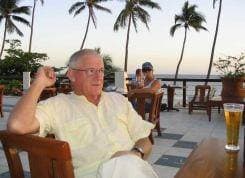
Geoffrey Whitelaw
- Port Melbourne, Australia
Currently, we are the only binding company that is using SS hardware. If we can find a suitable alternative then we will implement it. If we cannot, then we will stick with what we are currently using. It would not be a rash, or untested decision, I assure you. Thank you for the helpful information, once again!
- Cerritos, California
2005
Q, A, or Comment on THIS thread -or- Start a NEW Thread