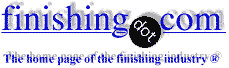
-----
Oxidation removal from electroless nickel plating for solderability
1999
I have a process issue in my plant that your forum could probably help with.
Raw material: Electroless Ni plated, aluminum housing, approx. 4 in x 2 in x 1/2 in.
Process: Operator applies solder to plated through holes prior to installation of "feed through" (ie, connector wire for PCB output). Feed throughs are installed and soldered in place. (Solder used is 62Sn, 36Pb, 2Ag) The solder application is designed to seal the feed throughs. Design engineers spent a lot of time calculating the correct hole to pin ratio to account for thermal expansion and contraction of the 3 mating parts (feed through, solder, and housing). However, due to oxidation on the plating, the solder never forms an intermetallic layer with the Ni, and there is a 30% fallout rate at final leak test.
As a small experiment, I cleaned half of one housing (one an operator told me looked like a better than average surface finish) with a 10% HCl solution. I then compared the solderability of both sides and saw obvious improvement in the cleaned side.
Here's my dilemma: I am not allowed to implement a manual acid clean process for this product, as it is a military product. ANY residual acid will slowly deteriorate the ceramic PCB until the unit is worthless. Fallout of 30% is preferable to one field defective part.
I have two options as I see it:
1) Obtain a small automated piece of equipment that will acid clean, neutralize, and rinse the parts without operator intervention or adjustment, save loading and unloading parts. (Does this machine even exist, or do I contract a company to build it?)
2) Find a suitable solvent that will not affect the other materials in the product, but will effectively remove oxidation from electroless nickel plating.
Does anybody have any help for me?
Jason FullertonConshohocken, Pennsylvania
I resemble any remark about the ability of an automated process to leave any more or less acid than a manual process. There is no such thing as a military specification that will allow an automated process, but not a manual one. What you need is an approved method that will clean the part (as you say you saw an improvement in solderability), manual or otherwise. I would get the approval using the manual process, if it works, then try to automate it, if practical.
I assume you must use only rosin/alcohol as a fluxing agent? I am not sure that oxidation of the nickel is the problem: what does the surface of the nickel look like? How long is it in storage? Are you allowed an RMA flux (probably not)? Are you soldering a glass-hermetic seal into this hole in the aluminum case? How thick is the E'less nickel? It should be at least 0.0002", as a first guess.
Regards,
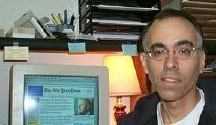

Tom Pullizzi
Falls Township, Pennsylvania
1999
1999
Points of clarification:
1) Military is not disapproving manual process; management is, and I agree with them. If one person cuts a corner and skips the neutralization step, we are in big trouble. The automation is designed to eliminate any possibility of human error.
2) We are using RMA flux.
3) Yes, the feed-throughs are glass-hermetic.
4) Surface of tested part was clean and fresh from supplier, although I can't say how long they held on to it.
5) I'll have to pull the drawing to check plating thickness, but I doubt it isn't enough (military product and all).
Conshohocken, Pennsylvania
I too favor automated lines over manual ones and hate to see repetitive manual drudge work -- but 40 years of specialization in automation of finishing lines leads me to side with Tom completely on point 1. If the operators can't be depended upon to process parts per process sheets where the details are carefully spelled out, they certainly can't be trusted to deal with "fuzzies" like keeping the rinse tank levels right, keeping the automation arms adjusted, and properly reporting inevitable machine malfunctions.
Consider this parallel: if you are very seriously injured in an accident and are taken to a hospital, would you be more comfortable with automated equipment monitoring your functions, or with a doctor standing over your bedside? If you can't trust the operators, it's management that is flawed! When you can't afford a field failure you can't afford to remove humans from the process.
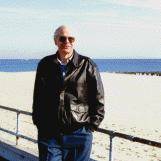
Ted Mooney, P.E.
Striving to live Aloha
(Ted can offer longterm or instant help)
finishing.com - Pine Beach, New Jersey
Q, A, or Comment on THIS thread -or- Start a NEW Thread