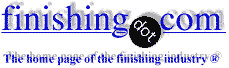
-----
Rust protection for etched carbon steel
Gentlemen, here's our situation: we are currently working some carbon steel 10-10 parts for one of our customers, they need the parts to be etched and stand at least a 48 hour rust protection. This product is used in an electronic device and does not allow any protective coatings such as wax, lacquer or oil.
The etching solution we are using for these parts is a 25% muriatic acid with Activator 1424 at room temperature for 1-2 minutes, then lots of rinsing.
We are finding that some of the lots show signs of rusting before 24 hours after being processed.
We have tried vacuum packing in sealed containers; some anti-tarnish but they requested we refrain from this since they did not know how it would affect the function of the part once it was assembled. Any suggestions?
Carmen Ma. Rosaplating shop - Bayamon, Puerto Rico
1999
Carmen- A possible solution to your corrosion problem may be an amine based rust inhibitor. These are aqueous solutions that impart a very thin amine film(undetectable to the human eye) that can provide very good rust protection.
You don't specify how the 48 hour rust protection is tested - salt spray?humidity? Have your chemical vendor process some parts and then run them through testing at your customer. Good Luck.
Dan Brewerchemical process supplier - Gurnee, Illinois
1999
If these parts are rusting, then there must moisture on the surface. It won't take much water to rust carbon steel, even a slight condensation on the surface. Your first objective (after a thorough rinse, of course) is to make sure that the parts are dry, very dry. This may require assistance, such as a forced warm air flow or solvent rinse. Vacuum packing or storing in dry nitrogen are options for keeping them dry.
The previous post suggestion is a good one, if you can convince your customer. Another alternative that I will suggest is a triazole inhibitor. I believe that these have been used in the electronics industry, even for parts to be soldered. Consultation with a good supplier of inhibitors may lead you to the best solution.
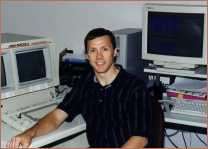
Larry Hanke
Minneapolis, Minnesota
1999
Gentlemen, thank you for your responses.
To Dan Brewer: the 48 hour rust protection is just about the time the part is in transit, at their plant, before finally being assembled into the final product. They are using a dry nitrogen chamber to store the parts before the next in-house process and then to final assembly. We've had shipments returned to us the next day after delivery due to rust signs on the parts, even after passing Quality inspection, ours and theirs.
To Larry Hanke: we installed an air blower to cool the parts after spin-drying them; after this, they are packed in plastic bags(provided by the customer) and vacuum stored in canisters (provided by the customer)and still some of the shipments are arriving at the customer's plant with rust signs. We've talked to them about the plastic bags keeping moisture in, and have suggested changing the bags to some other moisture prevention bags, they are looking into it! We are running their process, according to their specs and still have problems.
Carmen Rosaplating shop - Bayamon, Puerto Rico
1999
Q, A, or Comment on THIS thread -or- Start a NEW Thread