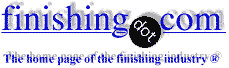
-----
Specs for salt spray solution
Q. Help. I have just taken on an inspection role which requires me to make up a salt spray solution. Is there any instructions or web sites with guidelines on!
Ian Webbautomotive - Birmingham, West Midlands, UK
2005
![]() |
Try ASTM B117 or BS7479, both describe a 5% neutral salt spray solution, its control and basically how to run a salt spray process. Brian TerryAerospace - Yeovil, Somerset, UK 2005 A. Check with your customers' specification, internal specification or you industries requirements. Most common source of information is ASTM B117....and the instruction manual with the salt spray cabinets often gives "ball park" information. You will probably need to adjust the pH after mixing to bring it, most likely, to the 6.5-7.2 pH range. Use very weak sodium hydroxide or hydrochloric acid and add small amounts to large volumes! Also the "type" of water is important....check ASTM B117 and the referenced ASTM D1193 for water quality. Douglas A. Hahnaerospace - Rocky Mount, North Carolina 2005 A. It's funny how times change. Decades ago I was employed by a manufacturer of salt spray cabinets, and we'd get frequent calls from purchasing agents wanting to know where they they could buy the saltwater. We found it comical because the idea of packaging and shipping saltwater seemed ludicrous. But with NADCAP, ISO, and other quality systems now wanting supplier certs, things are different and you not only can buy the stuff, but you almost have to :-) ![]() Ted Mooney, P.E. Striving to live Aloha (Ted can offer longterm or instant help) finishing.com - Pine Beach, New Jersey 2005 A. I guess you are referring to salt spray test. Please refer ASTM B117. ![]() T.S.N. Sankara Narayanan - Chennai, Tamilnadu, India (ed.note: The good doctor offers a fascinating blog, "Advancement in Science" ) 2005 |
A. Ian
The basic spec for salt spray testing is ASTM B117
There is a lot more to the test than making up the salt solution. Read the spec first and consider sub contracting the job.
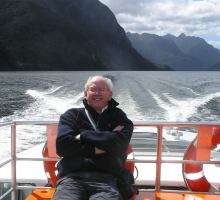
Geoff Smith
Hampshire, England
2005
Q. Does the ASTM call for adjusting the pH? I am having a problem with the salt spray results of panels that were run through the washer and painted at the same time showing significant differences when sent to different labs. I talked to our chemical venders chemist and he said "something that a lot of people don't know about"is that you have to adjust the pH of the salt solution before running the test"(this is the lab where the results were very good), but then the test results come out completely different in a lab where the chemist says he mixes the salt solution according to the ASTM, this chemist told me that the ASTM is very specific and you don't change it to something that "not a lot of people know about", this is from a UL lab and our test results are worse. I'm only raising the query because I was thinking our chemical vendor might be in the wrong, but since it's been mentioned here, I'm going to have to rethink it and try and decide what to do about it. No offense intended to anybody, but ASTM's were created to prevent this kind of confusion, and I don't know if I need to do anything to my washer at this point or not.
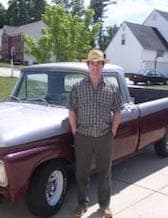
Sheldon Taylor
supply chain electronics
Wake Forest, North Carolina
2005
2005
A. This may have nothing to do with anything, but since you reference UL, I remember that at one time UL called for 20% salt rather than 5%. I don't know if that's still the case, but you might check that everyone is using the same spec for the salt solution.
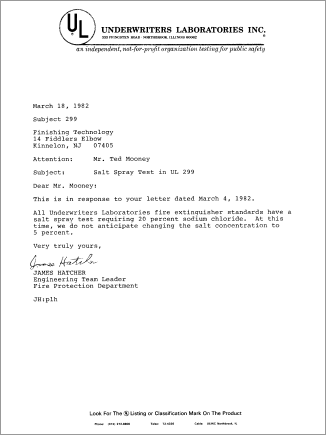
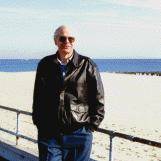
Ted Mooney, P.E.
Striving to live Aloha
(Ted can offer longterm or instant help)
finishing.com - Pine Beach, New Jersey
A. We have always adjusted the pH of our salt spray solution, otherwise we would not meet the requirements of the ASTM for the make up and collected spray pH requirements. Working in aerospace means that we get a lot of visits from OEMs and none has ever criticized us for correcting our solution, but they have picked us up for the odd time that it was missed.
Differences in pH can have quite an effect on the results that we see, especially with thin protective coatings such as Chromate Conversion Coatings on aluminum.
The ASTM is open to interpretation as to whether you are allowed to adjust the solution pH. If you are an OEM then you can make your own mind up about what you want, otherwise put the onus back on your customers to interpret the specification and get them to do the donkey work.
Aerospace - Yeovil, Somerset, UK
2005
2005
A. Well, that's actually right to the point, it seems to me that the percentage of salt in the solution would be one of the variables that make a viable test. If the ASTM states that you can change around the variables, save for different methods (which are clearly defined), it's not much of a standard. I don't have it, so I don't know how it's worded, but I'm sure it defines this particular element(% of salt in solution) since this one element will dramatically effect the test results!
I just found an aerospace checklist on the internet that doesn't give you the salt spray ASTM (you have to buy those-snicker, snicker) but if you read the check list, it is a basic run down of the standard, it does call for a controlled pH and 5% solution, along with a whole list of the other criteria related to the ASTM. If the UL labs were, or are not holding to the standard, that should be a problem shouldn't it?
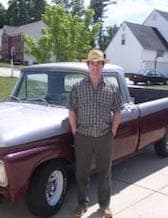
Sheldon Taylor
supply chain electronics
Wake Forest, North Carolina
There is no such thing as free, and time is money; just cough up the $33 for gosh sakes, your company can afford it :-)
Seriously, B117 is the work of thousands of hours of volunteer effort over decades, and every shop and specifier can afford to get it. As for UL, I was involved in a fire extinquisher project way back in '82 and the UL 299 corrosion test requirement was 20 percent salt. I don't know if that's still the case for fire extinguishers, and I don't know if it ever was the case for your product in question.
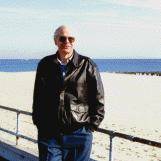
Ted Mooney, P.E.
Striving to live Aloha
(Ted can offer longterm or instant help)
finishing.com - Pine Beach, New Jersey
2005
2005
The thirty-three Washingtons must be like a hairball, I keep trying to cough them up, but just sit here hacking away and nothing happens, not a pretty site! The crud of it is that the location that I'm in was moved last year from a different area and someone lost the encyclopedia (I'm getting misty eye'd here) of ASTM's that engineering had. Wish I was here at that time, I would've treated them like they were gold plated.
We're actually a middleman and are not spec'ing the standards, so there hasn't been a push to replace them tsk, tsk. I know we aren't doing anything that has the requirements of your fire extinguishers, so I would trust that both labs are following the ASTM as it's written, the mystery is just going to have to remain for now.
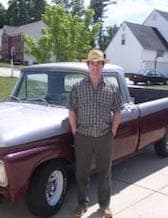
Sheldon Taylor
supply chain electronics
Wake Forest, North Carolina
Q. We are also working with fire extinguisher products and salt spray testing to UL 299. Our present anodizing spec. is MIL-A-8625 / MIL-PRF-8625 [⇦ this spec on DLA] Type II. The Mil. Spec I believe calls for 5% for 336 hours while the UL is 20% for 240. Should anodizing to MIL-A-8625 hold up for the higher salt percentage but less exposure time of the UL test? If not have any suggestions on an anodizing that will meet the UL spec?
Geoffrey AshAssembler - Greensboro, North Carolina
2005
A. I hope you've already found your answer. However, I have found that the company whose cabinet we purchased (Auto Technology) will blend the solution as well. It's not terribly expensive and saves a lot of time.
I find that a 55 gallon drum will last a good two weeks of 24 hour spray.
- Pottstown, Pennsylvania
May 6, 2015
Q, A, or Comment on THIS thread -or- Start a NEW Thread