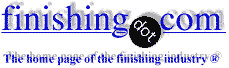
-----
High Current Density Leveler For Sulfamate Nickel?
Q. I'm currently trying to improve a thickness distribution issue with our sulfamate nickel baths. Normally, this does not pose a problem, but our company is now plating a part that consists of a group of closely-packed, 5/8" long pins embedded in a stainless shell and even deposit thickness along the length of the pin is critical. Rack design and keeping the bath pH in the low end of operating specs have helped considerably, but I'm afraid that any additional improvements at this point will only be achieved by means of some type of bath additive. Does one exist? Could there be something we've overlooked here? This is a typical MacDermid/Barrett SN process with SNAP A/M and SNHA added.
Rob Belterelectronics plating - El Cajon, California, USA
2005
A. A good picture of the part and one of it in the rack would make it much easier to comment.
There is no magic additive.
Increasing your air agitation and trying to focus it in the pin area will go a long way towards increasing the amount of plate in the low current density areas. If this is not enough, you will need to go to shields and or robbers.
Cyanide baths are the only ones that I am aware of where you can tweak the formula to considerably shut down plating in the high current density area.
As a final desperation, you might have to switch to electroless nickel.
- Navarre, Florida
2005
First of two simultaneous responses --
A. I know some experts will disagree but, can your bath tolerate some addition of butyne diol. It will increase internal stress somewhat but the deposit will smooth down considerably, specially in high current areas helping the overall contour of the plate. With all its inconvenients I still prefer this alternative to the suggested EN.
Guillermo MarrufoMonterrey, NL, Mexico
2005
Second of two simultaneous responses -- 2005
A. Any known leveler would add enough stress that it would defeat the reason for using sulfamate in the first place.
Raise the pH for better throw. Lower the current density and plate slower for better throw. Get the anodes further away from the cathodes for better throw.
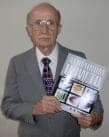
Robert H Probert
Robert H Probert Technical Services

Garner, North Carolina
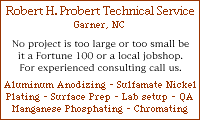
A. I've never measured the throwing power as these variables are changed, Robert, so I can't authoritatively agree or disagree with you. But I've also heard people say you should raise the current density for better throw. The reasoning being that when you plate faster the solution becomes depleted faster in the high current density areas, so the LCD areas have the advantage of a slightly richer solution than the HCD; further, the metal ions may not be able to migrate through the boundary layer quite fast enough in the HCD, lowering the efficiency there, with the result that the LCD areas come closer to being able to keep up with the HCD areas. It may well be absolute hogwash, but I'd appreciate a similarly simplistic accounting for why slower plating helps throwing power. Thanks.
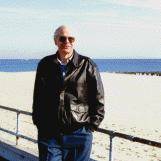
Ted Mooney, P.E.
Striving to live Aloha
(Ted can offer longterm or instant help)
finishing.com - Pine Beach, New Jersey
2005
First of two simultaneous responses --
Robert is correct with the slow plate. My reason is that the high current density area will never reach a point where the diffusion or barrier layer is significantly changed vs the extreme rate of plate in the high current density area. At least for heavy plate.
Raising the pH will definitely make it plate faster, but there are limits to how much you can raise it and not run into other problems.
Moving the anodes further away, if possible, definitely helps.
Higher temperature helped a little bit.
High or extreme agitation worked best for me.
- Navarre, Florida
2005
Second of two simultaneous responses --
A. I cannot explain the theory Ted, you know who my teacher was and he is retired but still available.
Repeatedly I have obtained better thickness distribution (is that
"throwing power" ?) by lowering the current density from 20 amps per square foot to 10 amps per square foot using sulfamate nickel at 10 oz.gal metal, 0.4 oz/gal Chloride, saturated for temp boric acid at 6 oz/gal at 120 F, and good agitation.
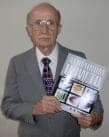
Robert H Probert
Robert H Probert Technical Services

Garner, North Carolina
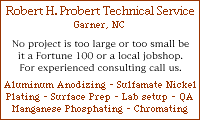
2005
First of two simultaneous responses -- 2005
A. I have to agree with Bob. Low current density, low pH, moderate temperature (and Ni metal at the low end) will all improve throw, but probably not by much from where he is now. It may not be possible to solve this problem with just bath operating conditions. Some sort of mechanical arrangement - robbers, shields, may be necessary It's gong to take some hands-on experimentation. An experienced rack designer might be a good place to start.
Guillermo's suggestion might have merit if there is treeing or roughness at the high current ends.
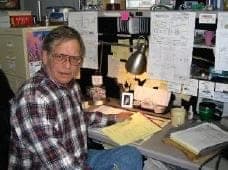
Jeffrey Holmes, CEF
Spartanburg, South Carolina
Second of two simultaneous responses -- 2005
A. Levelling is achieved by modifying the rate of deposition at different local current density areas. Areas of high current density are inhibited and made less efficient, allowing the low current density areas to maintain the same deposition rate. This is achieved by a combination of modifying the diffusion and the convection. In a recess the dominant deposition process is diffusion controlled, whilst an area of high exposure is diffusion dominant. Therefore to get enhanced deposition in a recess, the best way is to increase the agitation, but to slow the deposition down at a high exposure area, you need to reduce the local metal ion content. This can be done by limiting the rate of diffusion through the diffusion layer (aka Helmholz Double layer). This can be done by having a high imposed local current density as it will result in a high anionic charge layer (the first of the Helmholz double layer)and hence the drop in deposition efficiency at high current densities can be explained. If a solution is highly agitated it reduces the diffusion layer thickness, thereby promoting metal deposition and reducing the leveling effects. leveling by controlling temperature and current density can also be achieved, but the effect of these parameters will depend on the type of additives put into the bath, consequently both high and low cd can result in leveling, but only with the correct solution chemistry. Common leveling agents are coumarin (optimum 2 mmol/l), butyne 1,4 diol (8 mmol/l) as suggested by Guillermo, and Thiourea ⇦ on eBay or Amazon [affil link] . One problem with butyne diol is that if the bath is overdosed it reduces the bath throwing power and cathodic efficiency. You can also use acetylene and pyridine derivatives if you so desire. I can see how increased anode-cathode distances may affect levelling, especially in a low conductivity bath, but I would not consider it the prime method of control. In the old days nickel leveling was achieved with the addition of zinc, cadmium, lead or thallium salts, but this practise has long died out (possibly along with some of the operators!). You can also use saccharin (optimum 30 mmol/l), but this is not as good as the others and has issues when used in double layer nickel as it alters the corrosion properties of the nickel.
As far as stress reducers are concerned, suitable ones for nickel are 1,5 naphthalene disulphonic acid and trisulphonic acid, saccharin, quinoline, ethiodide, ethylene cyanohydrin and hydroxypropionitrile. However, if you choose the correct chemistry for your system, you shouldn't need stress reducers. I hope this helps and sheds some more light on an interesting thread.
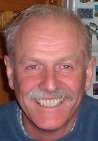
Trevor Crichton
R&D practical scientist
Chesham, Bucks, UK
Q. Thank you for all of your interesting responses- they definitely give me some ideas. I WILL say that we are incorporating shields and robbers on this project
(wonderfully designed, I might add), but I believe we've taken that idea as far as we can go with it.
One idea I have not yet seen from this thread is pulse plating. Would it help? I've read (and heard) a lot of good things about the process, but what tests we've conducted here in our lab (from a demo power supply) have left us somewhat disappointed. Thoughts? Opinions?
Once again, thank you all for your input!
- El Cajon, California, USA
2005
A. Hi there.
There was many good answers and I'm agree with Mr Robert and James to use a lower current density do get a better throwing power but with a low current density also the thickness will be harder. I'm always prefere rubber and shields and also inductive anodes with no direct current can helps to get the nickel there you will have it. To using more additives will change the chemistry to much and the solution can get a bad nickel deposit.
Regards
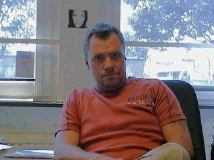
Anders Sundman
4th Generation Surface Engineering
Consultant - Arvika,
Sweden
2005
A. Pulse plating can help significantly, but it will take some experimentation to determine the optimum parameters. I suggest starting with a 50% duty cycle, and peak current amplitude approximately 2.5X what you presently use for straight DC plating. As for pulse frequency, in general, higher is better, but be aware that electrolyte's diffusion layer will have a capacitance, so if you pulse at too high a frequency, the results will not be much different that straight DC plating, as that's what the cathode surface will essentially see. If you pulse too slowly, there's a danger of passivation and delamination of the deposit, unless you maintain a small cathodic bias on the part and superimpose the pulsed waveform over it. Try gradually decreasing the off-time, but again be aware that the capacitance of the electrolyte will make too short an off-time ineffective. If you change the electrolyte's chemistry, optimum parameters will need to be reestablished, so settle on a fixed chemistry before experimenting with pulse plating. I have seen profound plating distribution improvements with this approach, but the ideal current waveform will have to be found, and this, unfortunately, takes a significant effort.
The overarching strategy is to keep the high current density areas relatively depleted of metal ions, and the low current density areas relatively rich.
Good luck!
- Orlando, Florida USA
February 15, 2011
Titration for naphthalene trisulfonic acid?
Q. As the title states I'm looking for a titration to determine the concentration of NTS in a nickel sulfamate bath. Is there anyone who can help me out with this?
Todd Murphyresearch technician - Alpharetta, Georgia, USA
July 24, 2013
A. Dear Todd,
we have had pretty good results in determining NTST with HPLC.
Column: Phenomenex Synergi polar-RP; 150*4.60 mm; 80 ; 4u
Eluent: 0,3-0,4M Na2SO4, pH 4 (1-2 drops of H2SO4)
If anyone has a titration method, I'm interested in it as well! :)
- The Netherlands
July 25, 2013
Q, A, or Comment on THIS thread -or- Start a NEW Thread