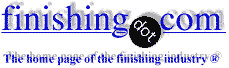
-----
Oakite Chromicoat Effects on EMI Shielding
2005
We are looking to use
Oakite Chromicoat L25 [Chemetall] on one of our aluminum enclosures. My question is will it have any effect on EMI shielding where two overlapping joints come in contact with each other. Currently the aluminum enclosure is painted and the surfaces that overlap are masked to ensure grounding conductivity between them, I am concerned that the coating will cause a decrease in grounding. Does anyone have any technical data to show that there is no effect on conductivity of two mating surfaces?
Thanks,
- Indianola, Pennsylvania
Hello,
This would be a question you should direct to your chemical supplier and or the manufacturer. They should be able to answer your questions easily.
- San Jose, California
2005
2005
Chemical coatings are applied to prevent aluminum from corroding. There are two applications, one is for electrical and the other for mechanical mating of structure. Class 3 (there is no Class 2) coatings are intended for use as a corrosion preventative film for electrical and electronic applications where lower electrical resistance contacts, relative to Class 1A coatings and anodic coatings ( MIL-A-8625 / MIL-PRF-8625
[⇦ this spec on DLA] not discussed here) are required. The primary difference between Class 1A and Class 3 is thickness. Coating thickness is varied by immersion time, therefore the same chemical can be used for both classes. Alodine 1201
⇦ on
eBay
or
Amazon [affil link] was the industry standard for years, but the chemicals used are sold now under other manufacturers, such as
Iridite 14-2 (Allied Research Products).
Oakite Chromicoat L25 is a low-cost liquid chromate conversion coating for aluminum. Applied by immersion or spray, it provides excellent paint adhesion and improved corrosion resistance. Chromicoat L25 may be controlled to produce either colorless coatings or rich golden coatings. Chromicoat T3 is recommended for replenishment of Chromicoat L25 solutions in high throughput applications. Chromicoat L25 can be controlled to produce either colorless coatings or rich golden coatings for decorative purposes. Oakite Chromicoat L25 meets MIL-C-5541 Class 1A Method C
(Immersion), and Class 3 Method C (Immersion). Chromicoat L25 is approved to Boeing BAC 5719.
Now, here is the real secret; the difference between Alodine 600 and
1201 is the thickness and that can be controlled by application
(length of time applied), allowing the user to keep only one chemical in stock. The problem with Alodine 600 is it is thinner and more susceptible to corrosion and therefore the area around the 600 must be painted to the original coating.
- Cathedral City, California, USA
Q, A, or Comment on THIS thread -or- Start a NEW Thread