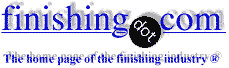
-----
Want good salt spray hours from phosphating without oil
Q. Good Morning.
Dear All,
Request to suggest for a top coat (inorganic based) which can give good corrosion protection for castings (without oiling is customer requirement). Lead time from Zn Phosphating to customer usage is almost 15 - 25 days.
- Chennai, India
January 30, 2023
A. Hi Sriram.
I suppose you can dip the castings in a chromic acid passivating solution if they do not need to be RoHS-compliant. Your posting seems to leave us with the same problem that has been running through this thread though ... we don't know what you or your customer intend to subsequently do with the parts :-(
You could perhaps apply a silicate or zirconium top coating ...
... but the parts will then no longer absorb oil or wax the way they are supposed to; and if they will be painted rather than oiled, it seems like you will have lost much of the purpose of the phosphate. Or does your customer intend to strip this inorganic coating, whatever it may be, before painting or oiling?
Luck & Regards,
Ted Mooney, P.E. RET
Striving to live Aloha
(Ted can offer longterm or instant help)
finishing.com - Pine Beach, New Jersey
Good Afternoon,
Dear Mr Ted Mooney,
Thanks for your inputs. We use phosphating only to protect the castings (Machined) from rust (High humid atmosphere in the region). Once the parts get assembled inside the axle, its not visible outside and as such functionally phosphating is not required (Except for rust prevention during storage). We will discuss with our customer and try out the option and evaluate the suggested process.
Thanks and regards
- Chennai, India
January 31, 2023
A. Hi Sri Ram,
As you know, Zinc Phosphating is an age old technology and gives minimal corrosion resistance without top coats.
There are alternative green technologies which use Polycarboxylic acids.
These technologies provide a greenish crystalline finish which resist corrosion without oils and other top coats for a minimum of 48 hours as per ASTM B117.
Balaji Viswanath
- Bangalore India
February 3, 2023
⇩ Related postings, oldest first ⇩
Q. We have a customer requirement for a component with Zinc phosphating thickness of 7 to 10 Micron and salt spray test to cross 72 Hours.
We have tried with various chemicals and we are able to meet only 30 Hours with 7 to 10 Microns.
Is it possible to meet 72 Hours with 7 to 10 Microns thickness.
If it is possible please send me process sequence and chemical details.
Thanks and Regards
PLATING SHOP - Chennai, TamilNadu and India
2005
A. Salt Spray life is mostly dependent on the rust preventive which is applied over the phosphate. Any of the major suppliers can give you a heavy wax or oil which will meet 72 hours.
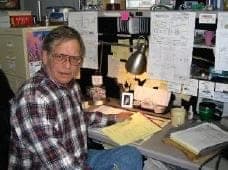
Jeffrey Holmes, CEF
Spartanburg, South Carolina
A. Mr Mohanan
It is possible to examine this approach.
Plate 7 microns Alkaline Cyanide free zinc. Chromate.
Paint .
SST will exceed your needs -- 120 hours.
Regards
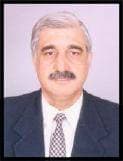
Asif Nurie [deceased] [deceased]
- New Delhi, India
With deep sadness we acknowledge the passing of Asif on Jan 24, 2016
A. Hello Mohann;
You need to use a water soluble topcoat, the kind they use over zinc plating, over your phosphating, it may work.
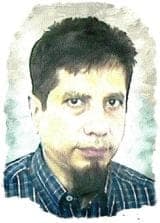
Khozem Vahaanwala
Saify Ind

Bengaluru, Karnataka, India
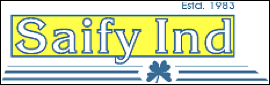
A. The phosphate coatings are basically a conversion coating. Your chemical supplier can give a chemical to get a coarse crystal conversion or a fine crystal conversion coating. If you go for a coarse crystal formation, the coating is porous, which will corrode fast. This type of coating is generally preferred for preparation before painting, so that the paint can adhere well with the pores.
For a plain phosphating you should go for a fine crystal formation. You need to convert these phosphate coatings with an additional chromating conversion, which is very simple dip in a chromate solution. This fine crystals will have very low porosity, and can have about 12 to 24 hours salt spray resistance without oiling.
An additional good quality of rust preventive oil in combination with zinc phosphate and chromate can give up to 96 hours salt spray resistance.
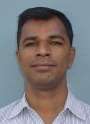
V. G. Rajendran
- Trichy, Tamilnadu, India
Q. We are doing zinc phosphating process. Our product is corroding only in later stages. What are all the reasons for corrosion of products on later stages.
K.Dharmaraj- Coimbatore, Tamil Nadu, India
2007
A. Hi Dharmaraj. Unfortunately there may be no way to approach the problem from that direction -- because failure, early or late, can come from numerous problems with the substrate, the pretreatment, the phosphate process per se, the post-treatment, handling & packaging, shipping, exposure conditions, or mis-specification. Please describe what you are doing and exactly what you mean by "corroding only later stages". Thanks!
Regards,
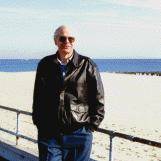
Ted Mooney, P.E.
Striving to live Aloha
(Ted can offer longterm or instant help)
finishing.com - Pine Beach, New Jersey
Multiple threads merged: please forgive chronology errors and repetition 🙂
Salt spray test hours for zinc phosphated panels?
Q. I want to know that what is the SST Range of Phosphated panels. I use Tri-cation Zinc Phosphate and Stages are as follows:
Cleaning
W/R
Derusting
W/R
Phosphating
W/R
Chrome free Passivation
Paint Shop - Faridabad, Haryana, India
May 26, 2010
A. A phosphated panel that has not been painted or does not have a protective coating applied will corrode very quickly in a salt spray chamber, probably less than three hours.
George Gorecki- Naperville, Illinois
A. Phosphating is a pre-treatment and not a finish. Hence, it cannot offer much resistance to corrosion in salt spray test.
One of the important attributes of phosphate conversion coating is its ability to prevent underfilm corrosion.
Measurement of the extent of spreading of corrosion from the scribed region of the phosphated and painted panel compared to its non-phosphated counterpart will give an idea about the quality of the phosphate coating.
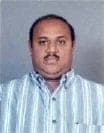
T.S.N. Sankara Narayanan
- Chennai, Tamilnadu, India
(ed.note: The good doctor offers a fascinating blog, "Advancement in Science" )
A I have done the salt spray test on a tri cationic cold zinc phosphating, and have the certificate from a testing body that my panel lasted 23 hours under salt spray chamber.
Shankar Omprakash Khandelwal [deceased]- Coimbatore, TAMILNADU, INDIA
It is our sad duty to pass along the information that the knowledgeable Mr.Shankar was lost to Covid/Corona.
He was awarded with honorable medal by then Indian president Ms. Pratibha Patil. R.I.P.
June 19, 2010
! Hi, Shankar. Thanks!
This begs the question of what wax or oil or rust preventative or top coat was applied to the phosphate, either deliberately or inadvertently, which may account for the salt spray survival time? I think if you degrease the panel after phosphatization to remove those greases and oils you may find that you don't even get 1 hour in a normal atmosphere, let alone in a salt spray chamber :-)
Regards,
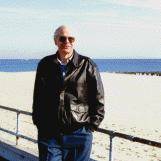
Ted Mooney, P.E.
Striving to live Aloha
(Ted can offer longterm or instant help)
finishing.com - Pine Beach, New Jersey
Q. I would like to know how many hours salt spray test will pass for Phosphated parts (ED coating - semi finished part)?
Product designer - Tamilnadu, India
July 7, 2011
A. Hi, Sathis.
I'm not sure if I understand the question, but you've read estimates here from 3 hours for zinc phosphate to 23 hours for tricationic. If you can phrase your question in terms of the previous responses, with what type of phosphating you are applying, and additional details, maybe an estimate can be offered -- but I personally think that Mr. Sankara offered a very insightful answer, i.e., that testing a scribe mark in a phosphated and painted panel is the proper way to judge the quality of the zinc phosphate pretreatment, whereas salt spray testing at an intermediate stage in the process may not be particularly useful.
If I am reading that the component has an ED coating, however, the salt spray hours could easily go to 100 or beyond. Good luck.
Regards,
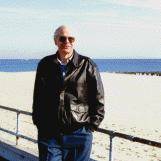
Ted Mooney, P.E.
Striving to live Aloha
(Ted can offer longterm or instant help)
finishing.com - Pine Beach, New Jersey
Q. We would like to know the life of zinc phosphated components in neutral salt spray test and normal atmosphere.
VIJAY GUNJALphosphating optr - Aurangabad, India
August 12, 2011
A. Hi, Vijay.
George Goreki estimated 3 hours in salt spray. If all of the oil has been stripped, I'll estimate a day in normal atmosphere; I've seen flash rusting even sooner than that.
As noted, phosphatization is not a final finish; and because of that, arbitrary and inconsistent factors may have more influence on the corrosion resistance than the quality of the phosphatization :-(
This then frames the question as whether there is much value in such testing or you're just throwing away money & resources by conducting such tests. :-(
Please try to tell us your situation, and please study Mr. Sankara's response and try to profit from what I feel is its wisdom. Thanks and good luck!
Regards,
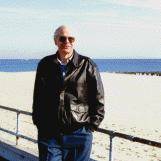
Ted Mooney, P.E.
Striving to live Aloha
(Ted can offer longterm or instant help)
finishing.com - Pine Beach, New Jersey
Q. Hello All,
I am a Master of Science Student in Chemical Engineering Department. I am researching corrosion protection on steel to which Zn Phosphating was applied.
These materials stay for 5 hours in salt spray test, and test is passed. But when I transport these materials, corrosion seems on material.
Do you have any idea to solve these problems ?
Best Regards
- Bursa, Turkey
May 7, 2013
A. Hello Duygu,
The panels were put in a salt spray chamber AND transported or the panels you put in the salt spray chamber are a sample of the ones that you transport?
I agree with Ted, phosphating is a pretreatment, a finish could be if you treat it with some anti-corrosive product (water-displacement oil, for example), or paint it (epoxy, KTL).
If your panels last 5 hours in salt spray chamber, I suppose they can last several hours in normal (dry) atmosphere.
Please tell us some more details :)
Regards,
- Cañuelas, Buenos Aires, Argentina
Q. What oils are recommended to apply after zinc phosphate coating to withstand 72 hours of salt spray test.
Alok Gaur- Mumbai, Maharashtra, India
May 26, 2016
A. Hello Alok,
You can use some heavy water displacement oil, there are many vendors capable of help you out of this requirement. Only, as I recall in my process, you must have more than 10 g/m2 of phosphate in the surface you want to protect. If you can use hexavalent chromium, I recommend a phosphate sealer before you apply the oil. You can't lose!
Hope I could clarify something! Best of lucks,
Daniel
N Ferraris S.A. - Cañuelas, Buenos Aires, Argentina
Q. Hi I want to know how many hours of salt spray life of zinc phosphate coated material. We are phosphate coating mild steel rod and dipping time is 45 minutes.
Thanks
- rudrapur udham singh nagar, India,
July 2, 2019
A. Hi Harish. The way I read the helpful answers offered, 72 hours is a good target if you are doing the phosphating correctly with quality materials and are applying a proper rust-preventative. How many hours are you actually getting? Remember that the purpose of a salt spray test is to learn whether you are currently doing the process right, not to extrapolate real-world life where the corrosion mechanisms are very different.
Regards,
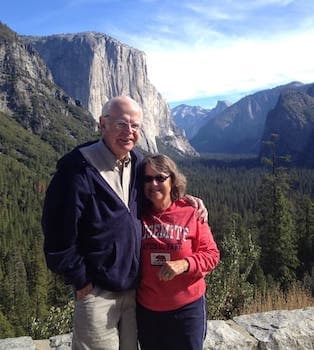
Ted Mooney, P.E. RET
Striving to live Aloha
(Ted can offer longterm or instant help)
finishing.com - Pine Beach, New Jersey
Q. Hi,
We are following below process in out Mn/Zn Phosphating:
Degreasing-->Water Rinsing-->Activation-->Phosphating-->Water Rinsing-->Passivation-->Dewatering-->RP Oiling
Now as we know phosphating layer should provide corrosion resistance itself, so can we eliminate RP Oiling operation??
We have taken trial of the same and found rust in approx. 12 Hours in Mn phosphating part without RP oil.
Please help how we can improve rust life without RP oil.
Thanks,
- Ahmedabad, Gujarat
January 13, 2021
A. Hi Keyur. Hexavalent chromating will help, and you can apply a clear wax instead of oil, and our friend VG advises us below that a small grain size will help because it's less porous.
But can you tell us what you are trying to accomplish -- i.e., why you want/need to operate in that fashion, and what you want the salt spray test to tell you? Will the parts eventually be painted, or are they internal machine parts which will eventually be bathed in oil?
The twin issues here are that phosphate is not designed or intended to be a final finish, and salt spray testing is not intended to predict corrosion resistance in the real world -- with the result that even after all your efforts the salt spray hours your un-oiled phosphate survives might remain little more than just a random number :-(
I worked with a firearms manufacturer who sometimes stripped the oil off of parts and then re-oiled them. Parts that were stripped of oil could sometimes flash rust in 20-30 minutes; but sometimes something would come up and they didn't get re-oiled that day but they did not rust even in nearly 24 hours. That shop didn't concentrate on trying to figure out all the tiny variations that might account for the 24-hour survival ... they focused on getting them re-oiled immediately. I'm afraid that you may find randomness rearing its head, such that just when you think you've got a big improvement going, a part will only survive 3 salt spray hours :-(
Luck & Regards,
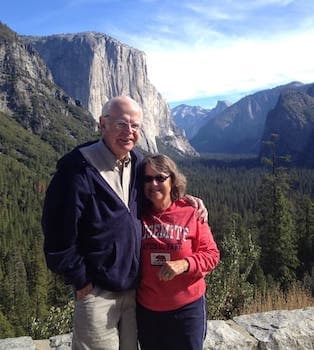
Ted Mooney, P.E. RET
Striving to live Aloha
(Ted can offer longterm or instant help)
finishing.com - Pine Beach, New Jersey
A. Manganese phosphate is rather thin and will provide little protection by itself. Zinc phosphate is much thicker and will be better, but both are better with a thin organic coating of water soluble wax.
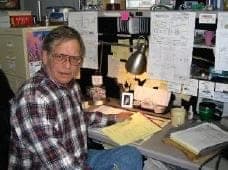
Jeffrey Holmes, CEF
Spartanburg, South Carolina
Q, A, or Comment on THIS thread -or- Start a NEW Thread