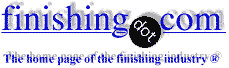
-----
"Bleeding" problems in anodizing cast aluminum
Q. I am a Supplier Quality Engineer.
Recently I am seeing some problem on a die-casting part, Al 390, anodized.
I was told it was an sulfuric anodizing process. We saw some white spots on the surface, and it happened only on the machined surface rather than cast surface. We have been running these same parts/anodizing for almost two years, did not notice this problem ... however, we saw this only when looking at the part with 10X scope....
Appreciate your help/advise on this.
Felix Heng- Singapore
2004
A. Bleed out from porosity in anodized castings is a common problem. Some batches of castings may be more porous than others. If you can't resolve the problem in casting, add a dilute 5% nitric acid step after anodize: anodize, rinse, rinse, dilute nitric, rinse, rinse, seal.
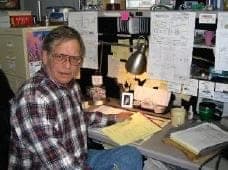
Jeffrey Holmes, CEF
Spartanburg, South Carolina
2004
Q. Hi,
Thanks for you advice. I have received the surface analysis report on those white spots through EDX. It shows high concentration of silicon - 78%, which is one of the impurities of Al 390.
(Compared to the normal anodized surface which has low silicon -9%, high O & Al.)
We looked at the surface under 30x scope, did not see any porosity, unless there are micro-voids that we cannot detect.
Also, what is the best method to check the anodizing thickness? Currently, I was told based on the setup it is about 17 micron.
Felix Heng [returning]- Singapore
2004
Q. Hi, I work for a company that uses aluminum parts (515 casting alloy) in food processing machines.
Lately, we have seen white spread areas on the surface of our anodized parts; we have analyzed any changes in the anodizing process, the finishing processes and the casting processes. All present no change except in the contents of copper; the alloy has 0.6% and it must have a content of 0.2%.
Gilberto Rochafood processing equipment - San Nicolas de los Garza, Nuevo Leon, Mexico
2004
Multiple threads merged: please forgive chronology errors and repetition 🙂
Q. I have a problem during color anodizing on the cast aluminium parts. The surface of the parts which are machined surface when colored after anodizing there appear stains bleeding from the porous surface of the parts? how can I cure my problem?
IFTIKHAR ALISTUDENT RESEARCHER - KARACHI, SIND, PAKISTAN
2005
Treatment &
Finishing of
Aluminium and
Its Alloys"
by Wernick, Pinner
& Sheasby
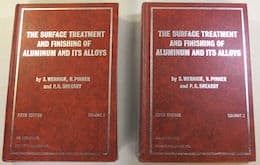
on eBay or Amazon
or AbeBooks
(affil link)
A. Hello, Iftikhar.
It is difficult if not impossible to properly anodize porous surfaces, but I would suggest that you at least try to minimize the problems that the porosity causes by dipping in dilute nitric acid before dyeing and trying a low temperature seal after dyeing. There are many threads here on this subject, including letters 14441 and 43777. Good luck.
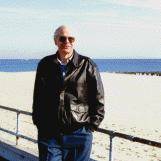
Ted Mooney, P.E.
Striving to live Aloha
(Ted is available for instant or longterm help)
finishing.com - Pine Beach, New Jersey
2005
September 6, 2010
Q. Dear finishing,
I have some finished product quality problems as shown in the title.
The two different products are casted separately with the materials of Alufont-47 and Anticorodal-72 (A357) before going for machining and 2 different coating processes (black anodized and clear anodized). Two coated products, using different coating processes have the following QC problems:
1)the part by black anodized process: some blue-black particle were observed on the cloth when cleaned with IPA.
2) the part with stain mark by hard clear anodized was found some stain-mark on the part surface.
Both parts are ring shape.
Anybody please answer to solve out these problems.
Thank you.
Process Engineer - Singapore
A. When we "seal" anodizing we are hydrating the aluminum oxide molecule and making it larger so that it expands to fill in inside of the anodizing pore. Anodize sealing does NOTHING to the porosity inherent in aluminum castings. Your dye is bleeding from the entrapment in the casting pores. It is not bleeding from the anodizing pores if it is properly sealed. Black dye comes out blue or purple when the thickness is thin, so with silicon near the surface of your castings the thickness is not enough to adsorb enough dye. silicon on the surface can be minimized with proper pre-treatment. Clear anodizing on castings is easy to stain because of the casting pores.
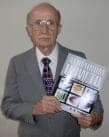
Robert H Probert
Robert H Probert Technical Services

Garner, North Carolina
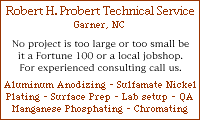
September 8, 2010
Bleeding in machined surface of Anodized Aluminum castings
Q. We are foundry doing Aluminum castings where the wall thickness is ranging from 3-5mm after machining. The shape is like a small CPU box of desk top computer with the dimension of 12 x 6 x 6 inches cube (LxWxH). After machining and buffing the casting is delivered to an anodizing company, After black anodizing there areas where there are white streaks and the the anodizing company called this "bleeding". The cause they said is due to porosities in the surface. Porosities are acceptable by end user as long as there is no "color difference" in those areas, meaning the black dye intensity is uniform throughout the surface.
Can you please advise and recommend how to have uniform black color even there is porosity (probably gas porosities) in the machined anodize surface? Thanking you in advance
Foundry Metallurgist - San Pedro, Laguna, Phil;ippines
February 14, 2016
A. Castings are a particular problem to color anodize. The inherent porosity does lead to the bleeding the treatment house is talking about.
There are a couple of things you can try to alleviate the problem and one the treatment house can try to try and reduce bleed out.
You can try Hot Isostatic Pressing (HIP) to reduce porosity. I can't tell you much about the process, just that my company treats alloys that are susceptible to gas porosity by HIP.
You could try impregnation. This essentially "fills" the porosity holes with a material, such as sodium metasilicate
⇦ on
eBay
or
Amazon [affil link]
. This can reduce the amount of bleed out seen on the parts.
Finally something the treatment house can try. After anodizing and before dyeing they can alternately rinse in hot (60 °C) and cold water in an attempt to remove the trapped sulfuric acid. In castings where porosity is a problem I would repeat the alternate hot and cold rinse at least three times.
Aerospace - Yeovil, Somerset, UK
February 15, 2016
A. 60 °C (140 °F) starts the hydration (sealing) and leaves less room for dye adsorption and interferes with desired sealing after dyeing.
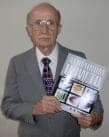
Robert H Probert
Robert H Probert Technical Services

Garner, North Carolina
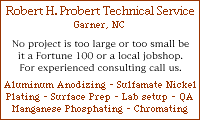
February 15, 2016
A. Hi Robert,
25 years of anodising of castings, never had a problem with sealing at 60 °C preventing dye uptake. Exposure at that temperature is relatively short, maybe 2 minutes maximum. The probability of getting any significant sealing at that temperature and time is slim.
Aerospace - Yeovil, Somerset, UK
February 17, 2016
Granted that "less room" and "slim" are not quantitative scientific numbers but maybe by the time you have 66 years you will understand the problem.
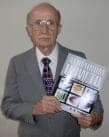
Robert H Probert
Robert H Probert Technical Services

Garner, North Carolina
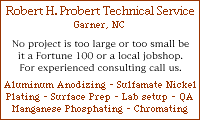
February 17, 2016
We all learn from each other, but it's also true that when we have decades of specific experience in a particular narrow subject, we're not going to put as much weight on someone else's knowledge as our own :-)
You'll find me very open to learning on process issues because my actual hands-on experience is light; but when we talk plating & anodizing equipment issues, I'm a mule :-)
Regards,
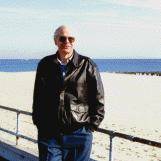
Ted Mooney, P.E.
Striving to live Aloha
(Ted is available for instant or longterm help)
finishing.com - Pine Beach, New Jersey
February 2016
Hi everyone ; my name is mohsin shah; I am a beginner to anodising! I am trying to anodise sand cast aluminium, and I can't, I don't know why. If I anodise solid parts the anodise is very good, but on castings I am helpless. I am trying to do black anodising on aluminum; the part is approximately 16*8*9 inches and has fins on it and is hollow on inside.
When I anodise parts there is like powder on them. Then I try some oil on them and rub with a cloth; they look better but not best quality -- what should I do? And most importantly, black colour is not pure black ... it seems like gray or purple I think,
Mohsin shahMs engineering - Islamabad Pakistan
August 29, 2017
Q, A, or Comment on THIS thread -or- Start a NEW Thread