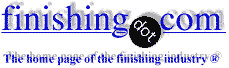
-----
Difference between pre-galvanized and hot-dip galvanized steel?
Q. I am a site supervision Engineer, I am working for an electrical systems CONSULTANT, Riyadh , KSA. I am supervising the Electrical construction work of one of the largest in the Gulf Region. Actually I need some information about one of products which is : The galvanized Switch and Socket Boxes.
My Question is : Some manufacturers use to write " Pre Galvanized switch and socket boxes", Others used to write "Hot Dip Galvanized switch and socket boxes". What is the difference between the two type of steel? The answer is very important for me as a consultant.
So, please your prompt Answer to this question along with any other information about steel types are highly appreciated.
electrical systems - Riyadh, KSA
2005
A. In answer to your question, they may both be hot dip galvanized. The difference is probably whether the material was galvanized before or after fabrication. Most boxes are made from sheet that has been "mill galvanized", which means the coil manufacturer galvanized the sheet on a continuous line. This coating is generally very thin (.5 - 1.5 mils) and during the fabrication by the box manufacturer, any cut edges will be left exposed. Also, any welds will damage the initial coating.
A box galvanized after fabrication will usually have at least twice the coating thickness, and any evidence of fabrication should have the benefit of being coated. And yes, is is usually much cheaper to build a box out of pre-galvanized steel.
Houston, Texas
2005
Q. I am pretty new to this area, but would like to get to know some more details about 'pre-galvanized' and 'Hot Dip Galvanized' steel.
Is there any way we can figure out the two types by looking at the surface? Or by touching the surface? Is there a difference in color or the way the surface is formed?
I would really appreciate if you can reply ASAP. Thanks in advance.
- Kelaniya, Colombo, Sri Lanka
January 4, 2010
A. Hi, Vindya. The distinction relates to whether holes were drilled or edges sheared or parts welded together after galvanizing. If the component has no holes or sheared edges or welds you can't tell the difference because there is no difference (although David Jaye is probably right that the thickness of galvanizing on fabricated components is probably heavier than on plain sheet). But if edges are sheared or holes are drilled after galvanizing, there will be exposed steel.
Regards,
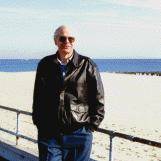
Ted Mooney, P.E.
Striving to live Aloha
(Ted can offer longterm or instant help)
finishing.com - Pine Beach, New Jersey
January , 2010
A. It is very easy to tell the difference between fabrications made from pre galvanized steel and those which are hot dipped after fabrication. The edge finish and weld appearance are some of the obvious ways as already mentioned. In my experience post fabrication hot dipping produces a less consistent finish, tends to contain inclusions leaving the surface rough in places and will leave drip marks and build up in areas where the molten zinc cannot fully drain.
Post fabrication galvanizing will provide superior corrosion protection as the minimum thickness of zinc will most likely exceed that which you will find on pre galvanized material. The downside is that if a high quality aesthetic finish is required (powder coated or wet painted) a significant amount of surface finishing may be required prior to painting. It's worth noting that in the case of pre galvanized sheet, the exposed edges left after cutting/punching still remain protected from corrosion. I can't explain the science behind this but I have experience of this working over many years of outdoor exposure.
Richard Lyons- Ireland
January 21, 2010
Thanks, Richard, that was helpful. The exposed edges are protected from corrosion in the same way that a zinc anode helps protect the steel hull of a ship.
Regards,
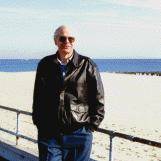
Ted Mooney, P.E.
Striving to live Aloha
(Ted can offer longterm or instant help)
finishing.com - Pine Beach, New Jersey
January 21, 2010
Thanks a lot to both of you,Ted and Richard. This was very helpful.
Regards,
- Kelaniya, Colombo, Sri Lanka
February 7, 2010
A. The difference is very obvious by naked eyes.
Just see once keeping side by side.
- Mumbai, MH , India
April 21, 2010
A. Pregalvanized method: once the sheet metal plated in the continuous galvanizing (melted zinc) bath, before fabrication, the plating thickness will be minimum 12 µm, and the materials plated by this way will be protected against corrosion on cut surfaces due to the cathodic effect between zinc and iron (steel); it's valid and effective up to 2 mm thickness.
Hot dip galvanization method: this method is the process of plating the sheet steel materials by dipping into zinc melt after fabrication, plating thickness by this method will reach minimum up to 45 µm.
thanks
- Istanbul, Turkey
December 7, 2010
Thanks all of you guys, it help a lot to my review/design works in Cable Trays/Ladders.
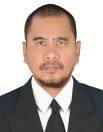
Wilfredo H. Meneses
- Doha, Qatar
February 28, 2012
Using zinc-rich paint on welds of pre-galvanized plates
Q. Hello... I would like to know if anyone can help me with a question about pre galvanised steel and coating zinc over the welds and cut points.
We have a project which is basically fabricating and supplying pre-galvanised 40 x 40 x 1.6 SHS panels plus miscellaneous plates to the Gas Fields, and we need to paint all welds to client protective coatings technical specification "Surface preparation SSPC SP 11, AS 1627 ST3 using Epoxy Zinc Primer 75-100". There is no requirement for 2nd & 3rd coat in the spec; therefore I would appreciate your advice to source a suitable product for use in the elements. Is the product you have identified the most suitable for this application?
I was told by a paint supplier that if we use epoxy zinc rich paint it will react with the pre-galvanised steel and in time it will fail, they said it fight against itself ?
They said to use just epoxy zinc?
Can anyone help me understand it?
Thanks
- Toowoomba, Queensland, Australia
May 24, 2013
A. Dear Friend
In Fabrication line: pre-galvanized structural steel is: "already hot dip galvanized".
For necessary repairing on pre-galvanized steel or galvanized steel, normally we use zinc-rich paints. After repairing with that, match the color with aluminium spray paint.
Please try.
- Sana'a, Yemen
June 4, 2013
Q. I'm supervising the production of some steel products. The case I have a question about is a product which consists of some round bars (Diameter 120-160 mm) and wires (Diameter 3 mm) which are welded together.
The product should be galvanized. According to the standard ASTM A123, minimum thickness of zinc coating is 100 microns for product diameter of 12-16 mm and is 50 microns for product diameter of 3 mm.
If the product is galvanized after the welding process, its not satisfying the coating thickness in all parts; and if each part is galvanized before welding individually, and then welded together, coating evaporation and peeling occurs (because weld area is relatively high).
- Arak, Iran
June 2, 2013
Is 500 hours salt spray resistance possible?
Q. Hi, I want to know if the behavior in cut edges of pre-painted steel EG or HDG is the same as an uncoated sheet? The thickness the steel is 0.7 mm.
Is it possible to reach 500 hours of spray salt test under ASTM B117 with EG or HDG?
Best Regards
Raul
- Esquina, Corrientes, Argentina
May 20, 2014
A. Hi Raul. We attached your inquiry to a thread where Richard L tells us that years of experience have shown him that the cut edges are often not a problem; it is often possible to 'roll' the edges so there is no exposed steel if necessary though.
500 hours of salt spray resistance seems improbable to me. Please remember than salt spray testing is a very very silly way to try to judge galvanizing though. The reason that hot dip galvanizing can be the most durable of all metal finishes (often able to last 75-100 years or even more without maintenance) is that the zinc slowly reacts with carbon dioxide in the air over the months & years, forming a hard, glassy, tightly sealed zinc carbonate surface; it is this corrosion product not the original zinc coating which offers the tremendous corrosion resistance. When you do a salt spray test, deliberately preventing the formation of this corrosion product, the salt spray chamber is testing something that has almost nothing to do with the actual corrosion resistance :-(
Please don't be a party to such foolishness. Good luck.
Regards,
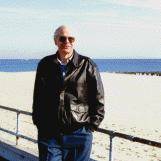
Ted Mooney, P.E.
Striving to live Aloha
(Ted can offer longterm or instant help)
finishing.com - Pine Beach, New Jersey
May 2014
Q. For assembling hot dipped galvanized Unistruts, galvanized accessories can be used?
qandeel hussainfield engineer - manama, bahrain
February 23, 2018
A. Hi Gandeel. Probably not. The problem is that 'hot-dipped galvanizing' has a clear meaning, but after people started calling zinc electroplating 'electrogalvanizing', they also started shortening it to 'galvanizing'. Depending on who uses the word 'galvanizing' and the circumstances, they might mean hot dip galvanizing or they might mean zinc electroplating (usually very thin and not usually good enough for outdoor exposure). If the accessories don't say 'hot dipped' and don't look hot dipped, they probably aren't, and they probably won't hold up.
Regards,
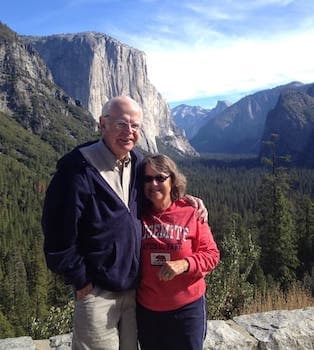
Ted Mooney, P.E. RET
Striving to live Aloha
(Ted can offer longterm or instant help)
finishing.com - Pine Beach, New Jersey
February 2018
Q. Hi,I am krishna working as site in charge in solar and my question is which one more conductive either pre-galvanized or hot dip galvanized?
Kalla krishna- Kakinada,andrapradesh, India
August 6, 2018
A. Hi Kalla. Please remember that pre-galvanized and hot dip galvanized are not 'opposites' or 'alternatives' in the way you are employing those words. It's pre-galvanized vs. post-galvanized, and hot dip galvanized vs. electrogalvanized (zinc electroplated).
But in any case, zinc covered surfaces receive varying chromate conversion chemistry, oxidize to varying levels depending on environmental conditions, and are not reliable contact surfaces. It is one thing to ground zinc plated conduit and junction boxes to minimize the likelihood of electrical shocks, but I think it is quite another thing to depend on them to reliably carry electricity.
Please tell us why this question is of concern.
Regards,
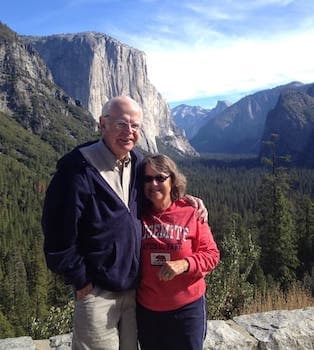
Ted Mooney, P.E. RET
Striving to live Aloha
(Ted can offer longterm or instant help)
finishing.com - Pine Beach, New Jersey
August 2018

Q, A, or Comment on THIS thread -or- Start a NEW Thread