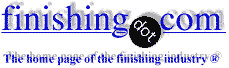
-----
Zinc Electroplating Peeling
Q. Hi,
A steel bracket we use inside of a automatic gearbox is electro-plated zinc plated. This has been fine for over a year now, but recently we have had some returns with the zinc peeling off. Under a electro microscope we can see two distinct layers of zinc plating with the top layer the one peeling off. The supplier apparently has no idea how this can happen. My question is can you plate over zinc plating with zinc to form two separate layers and how can you do this. Both layers have a good surface finish. The peeling takes about 1 year to start.
Auto gearbox manufacture - Yokohama, Japan
2005
A. Mr Simon Warburton.
You have not stated whether the component is hardened , or is high carbon steel. Likely its one or the other if its a gearbox component. I presume you are sure that there are two separate zinc layers clearly visible. Presuming the nature to be hardened or High carbon steel, it is not unusual for a plater to apply an acid zinc coat over the hard to plate base metal for adhesion to base metal purpose as layer number one. It is likely the second zinc plated layer is either an alloy of Zinc+ iron or simply alkaline cyanide free zinc. This is a Japanese technique.
In either case the adhesion between the two layers can improve with proper activation after the first layer is plated. Plated zinc can be activated in 10 percent dilute Hydrochloric acid before an acidic bath. Or in warm 100 gpl caustic before an alkaline bath.
Suggest you have the plater state his technique for purposes of Process validation first. Thereafter its a simple task of working the system backwards to trouble shoot the cause.
Regards,
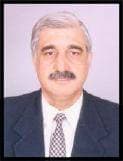
Asif Nurie [deceased]
- New Delhi, India
With deep regret we sadly advise that Asif passed away on Jan 24, 2016
Q. The bracket is mild steel - no heat treatment at all. The supplier is in Germany and the process shows only one zinc plating stage. The specification of the plating is >5µm and we normally see about 10-13um. The brackets that have been peeling the zinc plating thickness for the first layer is 10-13µm and about 7-10µm for the peeling layer. A GD-OES scan shows no contamination or any element enrichment in the interface layers. Experiments have been performed to try to replicate the issue. Process interrupt with parts in the bath 5 hours, process interrupt with parts out of the bath 4 hours and then placed back in bath, finished parts re-worked without the old zinc plating being fully removed by the pickling. None of these experiment parts have had 2 layers when checked under an electro microscope.
Simon Warburton [returning]- Yokohama, Japan
2005
![]() |
2005
A. Mr Simon Warburton ![]() Asif Nurie [deceased] - New Delhi, India With deep regret we sadly advise that Asif passed away on Jan 24, 2016 A. Dear Mr Simon, ![]() Khozem Vahaanwala Saify Ind ![]() Bengaluru, Karnataka, India ![]() 2005 |
Q, A, or Comment on THIS thread -or- Start a NEW Thread