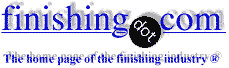
-----
Aluminum commercial polishing problems
2005
I am starting manufacture of high end billet aluminum motorcycle parts in Thailand and having problems with the polishing process. The parts are machined on high speed CNC vertical mills out of 6063 T6 billet aluminum. About 75% of the parts are chromed using five stage hexavalent chroming which includes buffing after the copper coat. The other 25% are polished to high gloss for either anodizing or ceramic coating, a few are left in raw high polish aluminum.
My problem is that our polishing shops damage the parts during polish. We are using 3 and 5 horsepower variable speed polishing motors so RPM can be regulated with plenty of power. We are getting too much surface distortion and burns around the holes in the parts. I am not a polishing expert but think the polishers are trying to cut the part too quickly or using materials more suitable for harder metals.
I am guessing the proper sequence should be something like the following.
1.Large diameter (10" or more) large width (2" or more) spiral sewn wheel using a extra fine grit high grease base brown tripoli buffing compound ⇦ on eBay or Amazon [affil link] (white? in the US) at slow speeds.
2.Small diameter (6" to 8") narrow Canton flannel wheel with super fine grit (jeweler's rouge ⇦ on eBay or Amazon [affil link] ?) at high speed for finishing.
3.A large diameter, very very soft wheel for dry buffing the 25% which do not get chromed to remove the excess grit.
Time per part is not a problem but damaged parts are very costly.
Can anyone give me some pointers and tips on how to start, I have a feeling that even if I get a starting point it will take lots of experimenting to get the process dialed in.
Thanks in advance.
Kevin Rodgers- Bangkok, Thailand
I worked for 5 years at an zinc aluminium die cast factory as an electroplater and polisher. The manufactured parts were linished across seams with a greased 120 grit belt,then into a mechanical polisher with marble chips as the medium.During this period the company expanded their product line and aimed more upmarket.The chromed and gold plated bathroom fittings needed a smoother finish so I polished the pieces using fastcut steel polish on a natural sisal,flat areas lenghtways.and piping the same. 12 inch 3-section wheels at 2850 revs on a 5 horse pedestal machine.I found with this pairing a good consistent surface removal of the affected areas due to marble finishing. It gave a good,quick cut and very low drag across holes and minimal heat. Some parts were further polished with an 8 inch loose leaf,50 or 100 leaf calico mop to soften the sisal marks in the lower current density areas before plating. They then introduced an aluminium component formed from 12 mm round bar with a mill finish. I found the same method the best all around finish for time and money. The aluminium parts were prepared on their own,then introduced to the plating line at the acid copper tank for approximately 15 mins and then into a copper activator and onto the nickel.I believe this to be the best procedure for plating aluminium.Heat from polishing affects the adhesion. The problem with your polishers could be a lack of polish on the wheel if its overheating the surface and maybe to slow in cutting in regard to abrasive and wheel speed. Loo
Dave Coleman- Fnq, Aus
2005
Hi I'm an aerospace polisher based in the UK it sounds to me if your getting burning its down to the polish your using try clear grease in a bar form, the grease or polish acts as a coolant. I personally would use lea compound mops finishing off on slow speed.
Grahame Banks- UK
2007
Q, A, or Comment on THIS thread -or- Start a NEW Thread