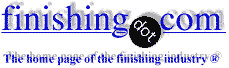
-----
DM Plant regeneration: Hydrochloric vs. sulfuric acid
Q. Dear sir,
We have 600 m3 capacity DM plant. For regeneration purposes we are using HCl and NaOH for the SAC (strong acid cation) and SBA (strong base anion) respectively. Can I use H2SO4 instead of using HCl for regeneration of SAC? If not what is the reason for it? I heard that if we use H2SO4 for regeneration of SAC, CaSO4 precipitation will effect the regeneration. To avoid that, what are the steps required? Please explain. And another doubt, in the regeneration time of SAC with HCl, whether CaCl will do any harm to resin like CaSO4. Please explain.
With warm regards,
copper - Tamilnadu, India
2005
Q. Why cannot sulfuric acid be used in place of hydrochloric acid for regeneration of cation exchanger.
Santi Swaroop Sibasish- Kalahandi, Orissa, India
2006
A. The reason is that some metal ions, most importantly calcium, will form sparingly soluble compounds with sulfuric acid. These can precipitate inside the resin beads, permanently damaging them. I have heard of sulfuric acid being used under certain circumstances. I'd advise doing some bench experiments, as well as running the idea by the vendor that sold you the resin system, before trying it out full scale.
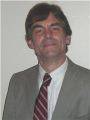
Dave Wichern
Consultant - The Bronx, New York
2005
A. Sulfuric acid can be used to regenerate strong acid resin, however, this requires a different procedure in order to avoid calcium sulphate precipitation and plugging of the resin bed.
You should contact your resin supplier for the procedure that they recommend. Typically, sulfuric acid regeneration requires three acid steps at 2%, 4% and 6%, and a faster flow rate than a hydrochloric acid regeneration. This may require additional equipment.
Also, if you are considering using 93% sulfuric acid, then you must also consider that PVC and CPVC pipe are not recommended for this strength of sulfuric acid.
Lyle Kirmanconsultant - Cleveland Heights, Ohio
2005
A. You can use sulfuric acid provided your DM feed water is softened and acid percentage should be between 5-7% of resin volume.
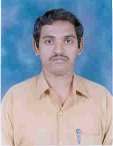
Panjala Mukesh
fashion jewelry mfgr.
Hyderabad, India
2005
A. Some of the reasons for not using sulfuric are not provided in the answers above:
1) Sulfuric acid gives you 1 gram of protons per 96 grams of acid, vs. 1 gram of protons per 36.5 grams of acid with HCl. This will eventually result in more chemicals, not necessarily higher costs, as sulfuric is cheaper.
2) Sulfuric is a very strong dehydrating agent. Any attempts to increase regeneration efficiency by increasing concentration makes the resins shrink during regeneration, not only resulting in higher rinse volumes (very long rinse cycles, to allow the resins to rehydrate again), but also in destruction of the resin by cyclical shrinking and expanding. Resins will break faster, and end up being dumped through the backwash cycle.
3) The most obvious reasons for precipitation are covered by other responses.
- Brea, California
2005
Thanks, Juzer, but is there a typo there? You meant "2 grams of protons per 98 grams of acid", didn't you? That brings the strength of sulfuric acid a little more in line with the hydrochloric acid.
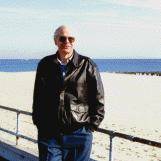
Ted Mooney, P.E.
Striving to live Aloha
(Ted can offer longterm or instant help)
finishing.com - Pine Beach, New Jersey
sulfuric acid regenerant is made a day before regenerating the DM plant; with this we can avoid resin shrinkage, which I am doing practically for last five years.
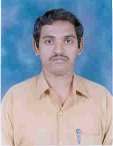
Panjala Mukesh
fashion jewelry mfgr.
Hyderabad, India
2005
I am not clear about the day after regeneration response, and what effect that would have on resin shrinkage?
In dilute acid solutions, sulfuric is actually H+ + HSO4-
- Brea, California, USA
2005
If we prepare dilute sulfuric acid it will be hot, and cannot regenerate instantly; if done it leads to resin shrinkage, so better regenerate after cooling.
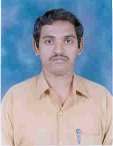
Panjala Mukesh
fashion jewelry mfgr.
Hyderabad, India
2005
A. sulfuric acid is very strong acid so will react with membranes and then the membranes will be corroded, and lastly the membranes will be damaged.
Ashish Sharma- Beawar, Rajasthan, India
2005
Q. But according to Panjala Mukesh, sir, for regeneration your idea taken one day before regeneration occurs but practically this is so much time because after 60 m3 when 18 hours working (or need of DM water) regeneration occurs twice a day am I right or you have some new idea for that?
Amit Pratap Singh- Delhi, India
October 8, 2010
April , 2013
Hi Amit. I assume that Panjala has an acid storage tank.
Regards,
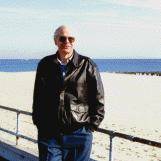
Ted Mooney, P.E.
Striving to live Aloha
(Ted can offer longterm or instant help)
finishing.com - Pine Beach, New Jersey
Q. Can I use H2SO4 instead of HCl for dosing purpose in REVERSE OSMOSIS (R.O.) system?
mitesh patel- ankleshwar, India
September 20, 2012
Hi Mitesh. It seems to me that the above discussion about DI Resins is highly applicable to RO membranes as well.
Regards,
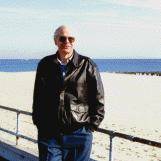
Ted Mooney, P.E.
Striving to live Aloha
(Ted can offer longterm or instant help)
finishing.com - Pine Beach, New Jersey
Q. CAN ANYONE TELL ME WHY WE REGENERATE THE SAC WITH 2 % AND THEN 4 % OF H2SO4. IS THERE ANY REASON THAT CATIONS (DIVALENT AND TRIVALENT) IS REMOVED ONLY BY 4%?
GIRI GANESH- INDORE
January 5, 2014
January 15, 2014
A. The reason for the multi-step sulfuric acid regeneration is that it avoids calcium sulphate precipitation in and around the resin beads. The 2% removes most of the calcium without exceeding the solubility of calcium sulphate in most, but not all cases.
It is more typical to use three steps: 2, 4, and 6% acid. Note that 4% sulfuric acid will not remove trivalent cations well from a SAC resin.
consultant - Cleveland Heights, Ohio
Why is my DI plant inefficient?
March 8, 2014Q. Hi,
We have replaced resins of our DI plant with Jacobi KW8 Cation resins and A4 Anion resins (25 Kg 8 bag each). As per the supplier we have regenerated it with 3 x 25 L HCl and 2 x 25 L NaOH. We are using SIATA control valves from Pentair.
Initially we had a small mechanical problem with the diaphragm valve of the final product water line (during regeneration cycle product water line was not closing properly); now we fixed it.
Now we are facing the problem with the results, the inlet water conductivity is 170 micro Siemens with pH 6.3 and outlet product water is 250 micro Siemens with pH 9.8 (an increase).
pH after cation regeneration: slow rinse water - 4.8, fast rinse water - 8.1
pH after anion regeneration: slow rinse water - 10.3, fast rinse water - 8.6
I would really appreciate if some one can help me out to find a solution for this.
Muhammad
- Cochin, India
March 11, 2014
Q. Snap shot about the DI plant
collection tank --> pump--> multimedia filter --> 2 x ( cartridge filter --> cation --> Anion) in parallel
No of stream: 2
Vessel Size: 21" x 60 "
Control Valve: SIATA Aqua Ionic
Cation: Jacobi, KW8 200 L
Anion : Jacobi A4 200 L
Pump Capacity: 12 - 42 m3/hr @ 57- 44 m head
inlet conductivity is 168 micro siemens @ 6.8 pH ( RO water)
Present condition ( both the stream is operated individually result is almost the same)
1C: Back wash : 5 mins
2C: HCL ( 32% ): 30 mins
3C: Slow Rinse: 20 Mins
4C: Fast Rinse: 60 Mins
5C: Back wash : 5 mins
6C: NaOH ( 48% ): 30 mins
7C: Slow Rinse: 20 Mins
8C: Fast Rinse: 60 Mins
Note:
4c: pH of the Rinse water
time left 60 mins = 1.3
time left 02 mins = 3.8
8c: pH of the Rinse water
time left 60 mins = 12.1
time left 02 mins = 10.8
Service mode:
174 micro Siemens @ 10.9 pH ( after one hour from regeneration)
60 micro Siemens @ 9.9 pH ( after six hour from regeneration)
Plant was not operated for 12 hours and result after that was 250 micro Siemens .
My Suspects:
1. There was a problem with the diaphragm valve, so during regeneration cycle NaOH and HCl escaped to collection Tank, and there was a thick layer of NaOH on the cartridge filter
2. Flow is too high.
- Cochin, Kerala, India
A. It appears that you have a problem with your cation exchanger. Normally, the pH after cation exchange will be <3. If your new cation resin was in the sodium form, then it may not be completely converted to the hydrogen form. This takes 2-3 extra strong cation regenerations.
Other possible causes are many. It could be an ineffective cation regeneration (too much resin that is still in the sodium form), or short circuiting of the flow through the cation exchange resin.
Cation resin in the anion resin tank will also produce high pH, high conductivity product, but the pH after cation exchange should still be <3.
consultant - Cleveland Heights, Ohio
March 12, 2014
A. Dear All,
We successfully use over years battery acid
⇦ on
eBay
or
Amazon [affil link]
(32-34%) to regenerate our DI-Water plant. Important is to analyse the tap water for hardness of it and, as per many posts above, especially for Calcium content.
We have an incoming conductivity of 100-150 microS and archive <5 microSiemens DI quality
- Chonburi, Thailand
March 15, 2014
Q. I want to know that why we use Demin water for rinsing of resin after dosing? Why we don't use raw water for this purpose?
Sohaib Ahmed Siddiqui- Karachi Pakistan
April 11, 2015
Q. Why DM plant Anion exchanger regeneration use hot water with HCl. What happened this system.
Md. Sabbir HossainSummit CCCP power company - Sylhet, Dhaka, Bangladesh
March 17, 2018
Q, A, or Comment on THIS thread -or- Start a NEW Thread