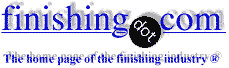
-----
Corrosion Protection for threaded low carbon steel
2005
We are currently making a rod approximately 40" long and threaded 1/2-13 on each end. We currently have the parts nickel plated for corrosion protection. The parts are rack plated in an acid bath and the plating varies significantly over the length of the part from .0002 to .0005. The buildup is even thicker on the threads which requires re-threading after plating. There is currently no requirement on the plating thickness, only bright nickel.
Is there any other coating we could use that would give similar corrosion protection but not build up on the threads. The customer states that their only concern is the corrosion protection. Thanks.
Dale Neff- Los Angeles, California, USA
2 tenths of bright nickel is very low in corrosion resistance. Electroless nickel costs more, but is very uniform and offers much better corrosion protection compared to bright nickel for the same thickness. You also do not get the extremely high buildup on the threads. You can calculate how much extra you need to take off when turning the threads and not have to rethread it. It does not work if you are cutting with a die. It might if you are only putting on 0.0002" per side.
James Watts- Navarre, Florida
2005
Good day,
Bright Nickel does not offer much in way of corrosion resistance compared to other coatings. I suggest you try a zinc electroplate. You will still have the variation of coating thickness but will find zinc is a bit easier to chase than nickel!
Bill Grayson- San Jose
2005
Salt Bath Nitrocarburizing has been utilized for years as an alternative for plating. The physical characteristics of the surface layers produced by plating and salt bath nitrocarburizing provide similar engineering properties. However, significant differences relate to the method of producing the layers, and the resulting physical bonding with the base material. Plating is applied electrochemically to the surface of steel producing a deposition coating. Whereas the thermochemical salt bath nitrocarburizing process process relies on a diffusion of nitrogen within the solid base material. This result is very little growth on the surface. This process also increases wear resistance, corrosion resistance, fatigue strength, lubricity and produces a lustrous black finish.
Vince MareckiKolene Corporation - Detroit, Michigan
2005
2005
You provide no specifics about your racking arrangement, but a properly placed thief/thieves can greatly reduce or eliminate the problem of uneven plating ("dog-boning").
Once you have made some simple tweaks to your rack(s), you should be able continue with bright nickel or switch to another electroplated coating and not be worried about having to re-thread the part. I might recommend trying an alkaline Zn-Ni alloy plate (typically ~12% Ni), but hearing no complaints about your corrosion results, perhaps bright nickel is adequate for the job.
Regards,
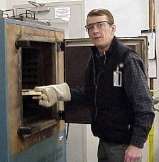
Thomas Hanlon, Materials Engineer
aerospace finishing - East Hartford, Connecticut, USA
Good day,
The problem you mention is very common in all threaded parts that require corrosion protection. Indeed many companies struggle with creating an even coating on threaded parts without the need to rethread after the coating process. The most suitable process I am familiar with for doing this kind of jobs is a process known as "Zinc Thermo Diffusion Coating" (not to be confused with "thermal zinc coating"). The process creates a very uniform coating on threaded parts and has an excellent corrosion resistance. Just Google "thermal diffusion zinc coating" and you'll be able to find some information on the process.
- Scarsdale, New York
2007
Q, A, or Comment on THIS thread -or- Start a NEW Thread