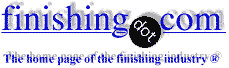
-----
Hardcoat thickness MIL-A-8625 vs MIL-STD-171
2005
Q. In reference to MIL spec
MIL-A-8625 / MIL-PRF-8625
[⇦ this spec on DLA] vs MIL-STD-171
Regarding hardcoat thickness:
In the latest rev of MIL-A-8625F Type III Hardcoat calls for a thickness of .002" ± .0004" unless otherwise specfied.
In , 7.5.1, the thickness references, per MIL-A-8625, with no revision letter noted, but it also says for a thickness of
.002" ± .0002".
I believe the most current rev of MIL-STD-171 was written before MIL-A-8625 was changed to Rev F & earlier revs of 8625 also called for .002" ± .0002" thick.
So, if they reference MIL-STD-171 7.5.1 do I need to hold the ±
.0002" tolerance, or does the current rev of 8625 override that & make that spec, MIL-STD-171 also ±.0004"?
Thanks
- Long Island City, New York
A. Good question, Dave.. seems a bit confusing to me. I would just hold the ± .0002" (a pretty simple spec to hold) that way you are covered.
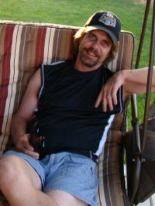
Marc Green
anodizer - Boise, Idaho
2005
Q. PLEASE LET ME WHETHER MIL-A-8625 IS TO BE FOLLOWED OR MIL-STD-171 IS TO BE FOLLOWED FOR HARD ANODIZING ON ALUMINIUM.
RAMESH CN- Bangalore, INDIA
January 10, 2013
A. Hi Ramesh,
It really depends what your customer has asked for, either in the PO or on the drawing. If it states MIL-A-8625 Type III then that must be followed, if it states MIL-STD-171 then that is your specification. If it is not clear, don't second guess your customer, pick up the phone and ask them what they want.
Aerospace - Yeovil, Somerset, UK
January 15, 2013
A. As David and Marc correctly imply above, MIL-STD-171 sends you to use MIL-A-8625 as the processing specification for anodizing of aluminum. So they're really the same, since 171 calls out 8625. Yet David noted that the tolerances are wider in 8625, so there is a slight difference. I think Marc's suggestion to follow the tighter tolerances is reasonable, and satisfies all the requirements.

Lee Gearhart
metallurgist - E. Aurora, New York
January 21, 2013
Q, A, or Comment on THIS thread -or- Start a NEW Thread