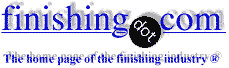
-----
Zinc-plate appearance problems (white, powdery, rough surface)

Q. Sir [Chellappan],
I am facing a similar concern in Acid Zinc plating. Could you elaborate on the process that you followed for flash and re-plating. How much time did you leave between flash and re-plating ?
- Nashik, Maharashtra, India
June 6, 2024
Ed. note: Chellappan's posting was from 2 years ago so he may or may not respond. If he doesn't, your posting will attract much more interest from other readers if you come back and explain what issues you are having and what you've learned and not learned about it.
⇩ Related postings, oldest first ⇩
Q. Came across parts after batch zinc-plating in acid-chloride that exhibit a white, powdery, streaky appearance (Parts are flat ~16 x 16 w/ moderate forming). When compared to "good" batches, "bad" batches seem rougher in texture (along with a overall lower reflectivity). Subsequent rubbing of the finished part surface with your hand exaggerates the powdery condition and leaves a white residue. You can clean off an area of a "bad" part with an acetone
⇦ on
eBay
or
Amazon
[affil link] Warning! Flammable!
-soaked rag which removes the white residue and the zinc coating remains intact.
It's questionable whether the substrate and/or plating process contains the key variables for this problem. Batch process utilizes two rounds of cleaning w/ de-ionized water and finally plating in a acid-chloride bath. Parts and finally a clear chromate conversion coating to passivate.
Anyone ever see this condition and have any ideas? Thought maybe surface roughness of the substrate and/or clear chromate was the culprit.
Thanks for the help.
metallurgist - Baltimore, Maryland
2005
A. Hello Chris. You say you 'came across' these, which leaves me with the question of whether they are new or old parts and whether you are working in the plating shop or these parts were shipped to you. My first guess is it's boric acid. Some plating shops will on occasion just hang a bag of boric acid in a plating tank and almost immediately start plating, with the result that crystals or powder form on the plated parts.
My second guess is your first guess, that it's a clear chromate problem.
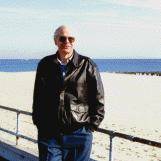
Ted Mooney, P.E.
Striving to live Aloha
(Ted can offer longterm or instant help)
finishing.com - Pine Beach, New Jersey
Q. Ted, thank you for the quick response. To help clarify my original inquiry, we are currently supplying low-carbon 1006/1008 CRSH to a customer who stamps parts and uses their own plater. Our customer and their plater are quite frustrated and I can understand they would want to question the substrate properties (ladle chem., rust-preventative oil, etc..). They've requested we be a main player in the analysis. I've begun working with their plater (via phone) to help them resolve and to this point have only received "good" and "bad" parts along with substrate ID(yet to do SEM/EDS on the powder). Info. gathered thus far leads me to believe there are more problems to worry about than the substrate.
Info gathered:
-All supplied substrate is confirmed to be supplied with the same rust-preventative oil (Quaker Ferrocote 61).
-Supplied substrate is Al-killed 1006/1008 w/ very low residual Si and similar chemistry, however a few shipments had higher levels of Cu (.11% vs .05%). Would higher Cu levels in the steel makeup be an issue?
-Supplied substrate had surface profilometer values measured in microinches of ~30-50 which is seen as typical for most mills at the same gauge (.040"-.050"). Maybe higher surface roughness holds excess solutions/oils through cleaning/plating/chromating?
-Plater uses alkaline cleaning solution w/ two rounds of rinses and plates out a .0002 - .0005 flash zinc in acid chloride w/ a final trivalent coat(clear chromate).
-Plater reports that they will run a batch of parts that will exhibit this condition IMMEDIATELY AFTER THE PLATING PROCESS
(apparently within seconds) and run another soon after, apparently under the same conditions with another batch of similar steel (same grade, etc..) without issues (nice bright, uniform zinc). Keep in mind I haven't determined if "immediately" means as soon as it comes out of the acid chloride tank or right after the chromate is applied
(which I will obviously need to investigate). Could you help me understand the steps between plating and chromating and between chromating and finished product?
-There's apparently no handling involved, as the plater uses a circular rack which can hold ~80 of these parts at one time.
-The condition seen on these parts is strikingly similar to the bottom left photo of letter 18213, however, the entire surface seems to be very very light white in color (powdery and streaky with a rougher surface). It becomes even more exaggerated though when touched or rubbed with any applied pressure.
-The plater has been relying on what has been referred to as a
"time-saver" which we are told is a belt-sander that is used on the steel prior to plating. This works well for them and is a large part why they are questioning substrate.
Being more process metallurgy oriented with only some electroplating knowledge (and knowing not to overstep my bounds), I'm looking for help from the finishing community to direct the right questions to the plater and help set up experiments to determine root cause.
Thanks again for the input
metallurgist - Baltimore, Maryland
2005
A. CAUSES FOR BURNED DEPOSIT,
1.IN THE ABSENCE OF ADDITION AGENTS,THE DEPOSITS ARE COARSE-GRAINED AND SHOW NO REFLECTIVITY,QUALITY IS VERY POOR AND MOST OF THE DEPOSIT CAN ACTUALLY BE RUBBED OFF BY APPLYING ONLY A LIGHT ABRASION.
2.LOW ZINC METAL CONTENT.
3.TOO HIGH CURRENT DENSITY.
4.LOW OPERATING TEMP.
5.LOW BORIC ACID.
ETC,.
ROUGHNESS:- EXCESSIVE ANODE SLUDGE,TORN ANODE BAGS. REDUCE AIR AGITATION NEAR ANODE BAGS.
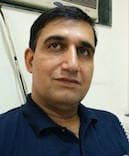
Ajay Raina
Ludhiana, Punjab, India
Q. Hi All experts,
I'm facing blur and rough surface problem on my rack plating (some okay but most have blur and roughness problem).
I've checked the ph between 5 - 5.5 and the temperature is around 29 °C.
Please advise, Lovely thanks.
- Malaysia
February 12, 2013
A. Hi Tim,
Unfortunately, the pics themselves are blurry such that I can't clearly see the blurriness of the plating :-)
Looks to me like water streaks on the parts from poor rinsing.
Luck & Regards,
Ted Mooney, P.E.
Striving to live Aloha
(Ted can offer longterm or instant help)
finishing.com - Pine Beach, New Jersey
Q. Good day,
I have a current customer complaint due to a surface finish on one of our part numbers that they define as "rusty". Before we ship the parts to our customer this condition is not present. Parts normal transportation is by sea (I go ignore if that is a factor for this "rust" to appear) but the customer claims that not all the parts have this condition so we would like to know what to look for at with our supplier that plates the part and focus on the factors that could produce these "physical appearance or rust". I appreciate your help.
- Tijuana, BC, Mexico
July 5, 2013
![]() |
A. Dear Monica, - Cañuelas, Buenos Aires, Argentina A. Monica, ![]() Blake Kneedler Feather Hollow Eng. - Stockton, California |
Thank you very much!! I already started questioning this. I appreciate the feedback.
- Tijuana B.C. Mexico
Q. Hello
I am a buyer and receiver. I don't have direct experience in plating. I order our parts to be plated with the following description: Zinc Chloride Clear Rack Lacquer .0002" meeting plating spec ASTM B633 - Type III Fe/Zn 5.
We have regular problems with white rust, streaking and drip marks that are visible when received from plater. See picture for most recent quality problem.
Is this a prep issue or a plating issue? Or chromate coating not done properly?
Paul Braden- Rockwood, Ontario, Canada
May 29, 2014
A. Hi Paul. I'd categorize it as a vendor issue because parts that look like this should not be shipped to you :-)
I realize the temptation to want to understand the issue and your desire to explain to the vendor what they are doing wrong, but it's very difficult and probably not productive because they probably know a lot better than you and I what the problem is :-(
My guess is that improper drying or lack of drying is involved, based mostly on the second picture where we see marks that look like what you would get if the pipes were set down wet on cardboard or newspaper to dry (what we are seeing as the top would be the bottom as they dry). Although I'm reasonably confident that this is one problem, and that it can cause the white rust shown on the first photo, I'm far from confident that it is the only problem.
I would suggest that you decide what constitutes unacceptable appearance vs. what are acceptable minor cosmetic flaws, then agree with your plater about it, and even build "sample boards" of good & bad parts if necessary. Good luck.
Regards,
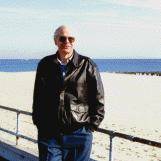
Ted Mooney, P.E.
Striving to live Aloha
(Ted can offer longterm or instant help)
finishing.com - Pine Beach, New Jersey
Q. Dear experts,
We are doing zinc plating (barrel plating) with trivalent white, hexavalent yellow passivation for our machined parts. After plating, these parts are packed in polythene bags and put inside cartons in a closed atmosphere. Some parts are not sold immediately were kept at our warehouse for one year. These parts were re inspected after one year and found passivation fade out and white patches. Please help to resolve the issue.
- Chennai, Tamilnadu, India
May 16, 2015
A. Hi Dinesh. They probably weren't fully dry.
Regards,
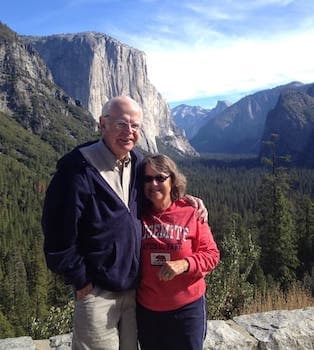
Ted Mooney, P.E. RET
Striving to live Aloha
(Ted can offer longterm or instant help)
finishing.com - Pine Beach, New Jersey
Q. We are using zinc plated on ms steel cover in a timer switch in automobile industry. After a few operations some of the cases white residue starts formation inside the cover and moisture formed due to operational condition (heat raised around 60 °C in closed environment).
What's the problems in the zinc plating.
Please provide solution.
switches - Jharkhand, India
March 29, 2017
Q. I run an alkaline non-cyanide zinc electroplating line and we are having issues with white patches on our metal screws. Our plating solution is kept at 35 °C; our rinse tanks are cleaned regularly; and we use a trivalent blue chromate. Currently our caustic is at 142 g/l and our zinc is a 23 g/l
- Cincinnati ohio
January 17, 2018
Q. We are manufacturing brake parts. We do acid zinc plating but plated part in white powder, and plating color is yellow. I am not understanding this problem.
I think this problem is passivation, and how does it come with burning problems? Please explain this problem to me.
- Ahmedabad, Gujrat / India
February 27, 2019
A. Hi Pintu. Please e-mail some good pictures of your problems to mooney@finishing.com. It's hard to understand your description. Does the 'white powder' wash right off? Are the parts yellow before they go into the passivation bath? Are you sure you are operating a clear passivation bath, not a yellow one? I don't know what you mean 'how does it come with burning problems' -- are you saying the parts are burnt, or are you saying you don't quite know what burning is and looks like, so you don't know if they're burnt? Thanks.
Regards,
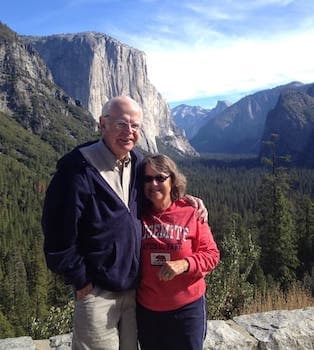
Ted Mooney, P.E. RET
Striving to live Aloha
(Ted can offer longterm or instant help)
finishing.com - Pine Beach, New Jersey
Q. Dear Expert,
I'm facing cloudy white patches/stains surface on my rack plating. The process is cyanide zinc electroplating. The surface is smooth but came out with those stains as shown in figure below:
Anyone ever see this condition and have any ideas? What are the potential cost and solutions? Please help. Thank you.
- Selangor Malaysia
September 14, 2020
A. Hi. What is that thing? ... and what is the substrate material and/or fabrication method? Is it a casting or forging?
It looks like there is a white haze, and even a yellowed area, and the plating looks awfully bright for cyanide zinc -- so maybe it's too much brightener in your zinc plating, which is preventing proper chromating? But I also see deep scratches or cracks and a couple of deep dings, which might indicate that the part is just not sufficiently mechanically prepared for proper plating rather than something specific that you are doing wrong. I appreciate you sending the picture but if you could please tell us what it is and what it's made of it would be helpful. Thanks!
Luck & Regards,
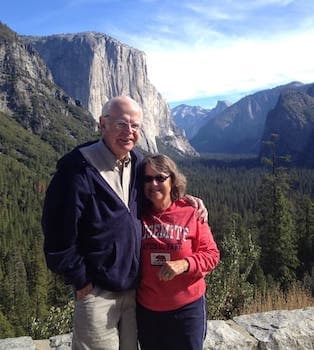
Ted Mooney, P.E. RET
Striving to live Aloha
(Ted can offer longterm or instant help)
finishing.com - Pine Beach, New Jersey
Q. Hello all, our supplier who makes us a 500 x 450 x 6mm steel plate grade S275JR with BRIGHT ZINC PLATE & PASSIVATE TO BS EN 12329-Fe//Zn 5//A (understand this is superceded by ISO 2081). He is not achieving what we require in terms of general finish. No one here has plating experience but it's unacceptable from our side. We can see the ungloved handling marks causing oxidation, leaching from holes, discoloration at the plate edges (measuring low plating, less than 2 mics, in that area with Dualscope), short marks on the plate face ... just general unhappiness with it. The supplier isn't responsive to questions as we don't spend enough there to be considered significant.
I've put a couple of pictures on:
... but my questions to you guys is what is the supplier doing wrong? What can I go to my boss with and present as an argument to change or work with our current supplier to improve the product?
Chris Jones- Milton Keynes, UK
March 27, 2021
A. Hi. If you don't wield the purchasing power with this vendor to get them to spend time answering your questions, you unfortunately don't have the juice to get them to change their ways and correct their quality to your liking :-(
Fingerprints are a sign that they just don't care; decades ago workers didn't generally wear gloves; these days most do, but this shop hasn't changed. And 2 µm thickness isn't acceptable by any standard that I know of.
You only have two choices: accepting the work the present shop is offering you, or telling them the quality is unacceptable for your needs and you must go elsewhere if they can't improve it. It is generally nearly impossible to determine precisely what is being done wrong without a lot of ongoing back & forth feedback.
But an additional issue arose for me from looking at the photos: what is the condition of the plates when you ship them to the plater, and who is responsible for necessary mechanical pretreatment if it's required? Photos can deceive, especially when we try to guess from post-finishing photos what the plates looked like before plating, but you can't get nice plating on a surface which isn't nice :-)
Luck & Regards,
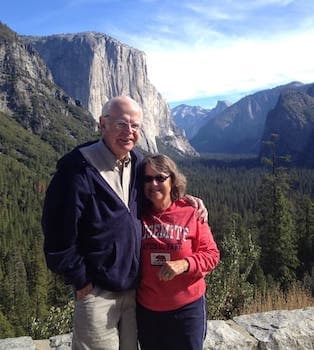
Ted Mooney, P.E. RET
Striving to live Aloha
(Ted can offer longterm or instant help)
finishing.com - Pine Beach, New Jersey
A. Hi Chris,
I saw the pictures. For dullness problem, run Hull Cell
⇦ huh?
panel in the laboratory and adjust chemistry, check brightener in zinc bath.
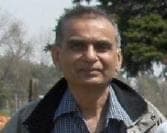
Popatbhai B. Patel
electroplating consultant - Roseville, Michigan
July 5, 2021
A. Interesting. I have some similar problems in my plating shop now. It appears a combination of two problems: Iron contamination and organic contamination of zinc solution. Treating zinc solution with zinc dust ⇦ on eBay or Amazon [affil link] and activated carbon may solve the problem. Lab scale trial may prove or confirm solution. By doing 2 litre treatment first and adjusting the additives. Run Hull Cell. I will find the clues from there on. Good luck.
Jenaro mincholaadvanced electroplaters - Melbourne_australia
February 12, 2023
Q. Some particular customer's Machined parts pre-parts after alkaline zinc plating: white patch coming after plating. In spite of pre-cleaning and double anodic and double picking also is not resolved.
Alkaline zinc plating 8 - 12 microns with Trivalent yellow passivation
- Bangalore, India
September 28, 2022
A. Hi Chellappan. A picture is worth a thousand words. Please try to provide pics of the finished product and the readers may be able to help better. Unfortunately "white patches" is rather vague and could have lots of causes from white rust, to burning, to water staining, to pitting, to brightener haze, to poor chromating. Read on though, where you will see many kinds of white patches resulting from many causes.
Luck & Regards,
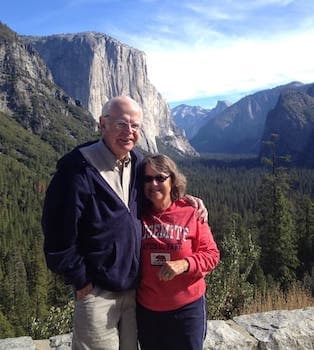
Ted Mooney, P.E. RET
Striving to live Aloha
(Ted can offer longterm or instant help)
finishing.com - Pine Beach, New Jersey
Thank you Sir,
Now I found the root cause. White patch happened due to some thick oil applied after machining by customer and there is huge time delay between machining and plating such that oil got dry and is not removed in regular pre-cleaning method. If we do flash plating and do replating then it comes out good. We discussed already with the customer to use the right RP oil.
- Bangalore, India
Q. Hi Sir,
Today I rubbed the zinc plating surface with thumb and found some particle of zinc got stick to my finger after abrasion.
Micron is 10 and done with both cyanide and acid plating with same results.
Why after abrasion the zinc plating is behaving like this?
- Mumbai, India
September 5, 2023
A. Hi Rajesh,
Please introduce yourself ... are you a buyer of this product or the plating shop producing it?
Drying at too high a temperature and thereby dehydrating the chromate gel is a very common thing. And the fact that you encounter the same problem on parts which are cyanide plated and acid plated tends to rule out a problem earlier in the process. What is the evidence that it is zinc plating rather than the chromate conversion coating which is abrading off? Thanks.
Luck & Regards,
Ted Mooney, P.E. RET
Striving to live Aloha
(Ted can offer longterm or instant help)
finishing.com - Pine Beach, New Jersey
Q, A, or Comment on THIS thread -or- Start a NEW Thread