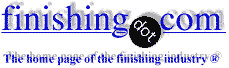
-----
Cryogenic metal treatment and surface wear?
Considering cryogenic metal treatment,can someone explain to me why the RC hardness doesn't vary during/after treatment, yet the abrasion resistance increases threefold?
thanks.
Bill Cardozamachinist - Elizabeth, New Jersey
2005
The best explanation I've heard is that after normal heat treating there is still some austenite left in the metal. Essentially, room temperature is not really the end of the heat treat cycle. If you extend the heat treat cycle to cryogenic temperatures, this retained austenite is converted to martensite, and wear resistance goes up, even if the overall hardness of the surface does not increase. One thing to keep in mind, however, is that increased hardness does not always translate into increased wear resistance. Wear resistance depends on other factors, such as frictional forces and the toughness of the surface. Very often making the surface harder reduces its toughness and increases its coefficient of friction, in which case wear resistance goes down.
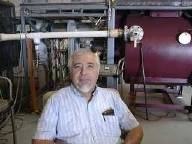
Jim Treglio - scwineryreview.com
PVD Consultant & Wine Lover
San Diego, California
2005
2005
There are three mechanisms related to cryogenic treatment of steels. The conversion of retained austenite (RA)to martensite is one. This mechanism is important and brings several benefits, including a contribution to increased wear resistance. Additionally, it provides for a more homogeneous grain structure, free of (grain) imperfections and voids, which contributes to enhanced thermal properties, (e.g. better heat dissipation). This is because the imperfections act as points of diffusion, effectively "blocking" or de-grading the thermal properties of the metal at those points.
A second mechanism, even more important to increased wear resistance, is the precipitation of eta-carbides in carbon steels. This has been documented by a team of Japanese researchers in a technical paper presented at ISIJ.
In order to understand its significance, I think that it is important to realize that the introduction of carbon to iron is what fundamentally makes steel. Carbon,(C) a non-metal, is chemically dissolved into iron (Fe). Chemically, the largest amount of carbon that can be dissolved into iron is somewhere around 7%. When people talk about "high carbon" steels -- those that are recognized for their high wear resistance properties -- they are often thinking about Tool Steels that may have somewhere between 0.7% and 1.2% Carbon content. So the point is that a little bit of carbon goes a long way in enhancing the wear resistance of steels.
Remember that Carbon -- AKA diamond --is the hardest element. By chemically blending it with iron (Fe), it effectively protects the iron molecules by providing a tough, highly wear resistant molecularly bonded partner.
On the down side, the more carbon that you add, the less ductile that the metal becomes. You could also say that it becomes more brittle or that it loses toughness (in a machine tool sense). So it is always a balancing act of having high carbon for high wear resistance versus not too much whereas the steel fails due its reduced ductility/ increased brittleness.
The whole point of this discussion is that CARBON is critical to wear resistance in steels. When carbon steels (and cast irons, etc.) undergo a cryogenic treatment, free carbon atoms are able to locate themselves within the chemical lattice of the iron / carbon (Fe-C) matrix in a place where they are more atomically attracted. This modification to the carbon microstructure (technically called "the precipitation of eta-carbides") can vastly improve wear resistance of carbon steels, cast irons, etc. In general terms, the more carbon, the better the effect.
Now, why does this occur? Again, it is all the result of TTT (Time Temperature Transformation)process. When steels are brought to a very low temperature (e.g. -300 F) for extended periods, heat is removed. As a result, molecular activity is reduced -- or molecular movement is minimized. (Remember at theoretical absolute zero, which is about -460 F, there is NO molecular movement.) So as heat comes back into the steel, e.g. as it gradually warms up, kinetic activity (molecular motion) increases and carbon atoms actually "tweak" themselves into a more ideal position within the chemical matrix. In a simply stated version, free carbon atoms are attracted to open spots within the iron matrix. This mechanism, ever so slight, can have big implications on increased wear resistance. It is the mechanism that the Japanese team documented and in my view is the one that is most critical to improving wear resistance in carbon steels.
As a final note, the third mechanism is residual stress relief. Einstein observed that matter is at its most relaxed state when it has the least amount of kinetic energy (or molecular activity). With a proper cryogenic treatment, any metal will be relaxed and residual stresses relieved. It is perhaps the least recognized benefit of cryogenic treatment. Parts that "walk" or "creep" during machining are the result of residual stresses in the metal that have been machined away that were keeping the part in a certain plane. So more and more people are cryogenically stress relieving metal parts to reduce the creep and walk factors that causes parts to go out of round or flat and fail critical tolerances. This is most successfully done after rough cut and before final machining. Again, this can benefit any metal and is unrelated to the other mechanisms cited above.
Robin RhodesWorcester, Massachusetts
I would like to know if cryogenic treatments can be used on non-ferrous materials such as copper or noble metals?
Kelly Stinson-Bagbyresearch - Blacksburg, Virginia
2005
Are there notable benefits to aluminum during the cryogenic process?
Sean Triheyracing - Phoenix, Arizona
2007
yes, cryotreatment can be used on non ferrous metals, even plastics
Robert Wells- el paso Texas usa
February 7, 2011
Q. I know about the Japanese study about cryogenic treatment on iron and steel but can you find anything about the process on bronze and brass alloys?
Steve GravesMusic Instruments - Cincinnati, Ohio, USA
January 19, 2013
Q, A, or Comment on THIS thread -or- Start a NEW Thread