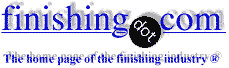
-----
301 Versus 304 Stainless Steel Fabrication
2005
For cost reduction, the idea of using 301 stainless steel versus 304 stainless steel is being proposed at my commercial oven manufacturing company. Does anyone have input on the pros and cons of switching to 301 versus 304 stainless steel in metal fabrication (punching, lasering, bending, welding, finishing? ) of food service equipment? Your comments would be appreciated. Thank you.
Bill Hansen- Menomonee Falls, Wisconsin
301 stainless steel, of course, is not as corrosion resistant as 304. It has lower chromium and nickel and higher carbon. It should be lower cost, but also lower in performance from a corrosion resistance standpoint. It would probably process faster. It is still a good grade of steel, but not AS good.
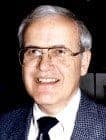

Lee Kremer
Stellar Solutions, Inc.

McHenry, Illinois
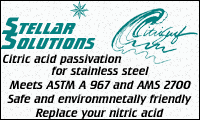
2005
As Mr. Kremer already stated, Type 301 has inferior corrosion resistance to Type 304. The behavior during punching and bending will be different for Type 301, since it work hardens at a much greater rate than Type 304. This means that the press forces will be higher, and the overall formability will be lower. Laser cutting and welding will be a problem for 301, since the higher carbon content will cause sensitization (formation of chromium carbides at the grain boundaries). Sensitization results in a depletion of chromium adjacent to the grain boundaries, which leads to intergranular corrosion.
Toby Padfieldautomotive module supplier - Michigan
2005
2005
The 301 material should process fine. 301 is allowed to be produced with a 6% minimum nickel content. In reality, the producing mills may use 7%-7.8% nickel to help with their processing, especially when rolling to light gauge.
The effective difference in nickel content vs. 304 is minimal. Likewise, the cost deltas may be minimal also.
If corrosion is a concern and you're using polished materials, you could consider a rolled on finish instead of the more typical abrasive polish. The rolled on finish maintains the chromium surface layer.
- Springfield, Illinois
To be honest, if you currently have all of your processes and suppliers using 304, the cost savings is so minimal that you'll spend more just to make the switch!
Bill Anderson- Kansas City, Missouri
March 26, 2009
Q, A, or Comment on THIS thread -or- Start a NEW Thread