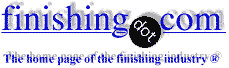
-----
Cadmium Plating Is Peeling
Aloha!
Currently I'm having issues with poor adhesion between Cadmium layer and Nickel layer, normally we used to activate the nickel surface (aging more than 3 days) using acid salts (Metex M629), but we started to got adhesion issues and we started to change our process as mitigation actions.
currently our cycle is:
10 min Alkaline cleaner
15-30 secs Rinse X 2 (conductivity less than 1000 uS/cm)
3 min HCl 30%
5 secs Drag out
15-30 Secs Rinse X2
go to Cad tank
also we tried with
2 min Soak cleaner
15-30 secs Rinse X 2 (conductivity less than 1000 uS/cm)
30 secs HCl 30%
5 secs Drag out
15-30 Secs Rinse X2
30 secs Metex M629
15-30 secs Rinse X 2
3 min Nickel electroless MP Plating
Rinse and Drag out
go to Cad Tank
Anodic Cyanide Activation (with working tank put the parts in the anode bar for 30-45 secs)
Cadmium Plating Process
With both flows we got the same issue with the adhesion between Cad and Nickel MP Layer.
My question is if there are methods to rate or measure the nickel activation?, for example if could be something similar to the copper sulphate
⇦ on
eBay or
Amazon [affil link] test for passivated steel.
Rodrigo Ornelas
Plating Engineer - Nogales, Sonora, Mexico
A. Hi Rodrigo. There are all sorts of adhesion tests, including the quantitative Modified Ollard Test, but I don't Know of any quick spot test like you are seeking.
I'm not sure if I am correctly reading your situation, but if you are trying to plate onto 3 day old nickel you'll need a Wood's Nickel Strike.
Luck & Regards,
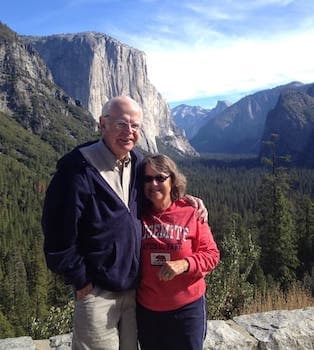
Ted Mooney, P.E. RET
Striving to live Aloha
(Ted can offer longterm or instant help)
finishing.com - Pine Beach, New Jersey
July 2021
⇩ Related postings, oldest first ⇩
2005
Q. We are an engineering company who supply plated parts to a customer in the connection industry through a sub-contract plating plating shop. We are having a problem with Olive Drab Cadmium to AMSQQP416 Type 2 Class 3 over Electroless Nickel where the cadmium layer is peeling off the nickel coating. The part is a connector and the plating can be removed from the outside diameter but not the bore. Our suppliers do not seem to be able to give us any reason for the problem but, as our customers are demanding a rapid corrective action, we may have to visit the plating plant. As we are not experts in the plating field can any one suggest what the likely causes of the problem are and what should we be looking for if we do visit?
engineering - Swindon, Wilts, UK
July 17, 2021
A. The most likely cause I would think is that the electroless nickel was not activated before cadmium plating. Non-precious metals owe their corrosion resistance to a consistent non-porous oxide film that prevents further corrosion, but you cannot plate onto that oxide film you need to plate before it forms or remove it before you plate. Try to find out what can about what happens between electroless nickel plating and cadmium plating. Good luck.
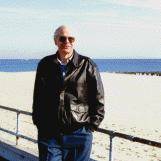
Ted Mooney, P.E.
Striving to live Aloha
(Ted can offer longterm or instant help)
finishing.com - Pine Beach, New Jersey
2005
A. Ted's reply in simple language is the rack has to go from the EN tank thru rinses to the cadmium tank in an ABSOLUTE minimum of time. It might help to go into the Cad tank with a low current applied during entry. If not, then the activation step is required and that is neither simple or foolproof.
James Watts- Navarre, Florida
2005
Hi Jim. Rod asked what time it was so I was just telling him how a watch works first, that's all.
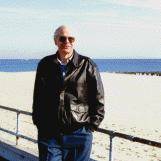
Ted Mooney, P.E.
Striving to live Aloha
(Ted can offer longterm or instant help)
finishing.com - Pine Beach, New Jersey
A. I do agree with Ted Mooney and James Watts that EL Ni surface requires an activation if the Cd plating step is not followed immediately.
In our experience, when we try to deposit a graded coating, consisting of alternate layers Electroless Ni-high P, EL Ni- medium P and EL Ni-low P coatings, by sequential immersion in three different baths, we have experienced such problems. Particularly when the initial layer is EL Ni-high P. We have deposited the EL Ni-high P coatings on one day. We tried to deposit the EL Ni-medium P on the same substrate the next day. To our surprise the deposition did not proceed. When we give a nickel strike using a watt's nickel bath, the coating formation proceeds without any problem. We have addressed this issue in our recent paper entitled "Deposition of electroless Ni-P graded coatings and evaluation of their corrosion resistance" to be published shortly in Surface and Coatings Technology.
I also believe that the formation of a passive film on the already formed layers is mainly responsible for this behavior.
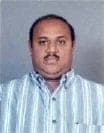
T.S.N. Sankara Narayanan
- Chennai, Tamilnadu, India
(ed.note: The good doctor offers a fascinating blog, "Advancement in Science" )
2005
A. Rod, where in the Spec QQ-P-416 can give you the permission to plate cadmium on E-nickel. To get good adhesion on EN nickel you must have a good knowledge about pretreatment on EN and to know there aren't many job shop who have. In the Spec you are only permitted to plate EN on zinc.
Regards
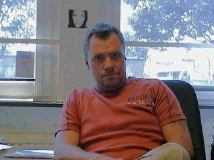
Anders Sundman
4th Generation Surface Engineering
Consultant - Arvika,
Sweden
2005
Q. Gentlemen
Thank you all for your interesting answers, Unfortunately the plating company are still unable to find the cause and we are still getting the problem albeit on just one or two batches out of the 50 or so sent per delivery.
Anders, the requirement for the nickel undercoat comes from our customers specification, they specify Cad to QQ-P-416 type 2 class 3 over electroless nickel to withstand a 500 hour salt spray test.
Sankara, your reply is interesting in that you had the problem between two electroless coats and solved it by using a flash of electrocoating. Our problem is between an electroless and an electroplated coat. Can you see any connections, I wonder? The platers use a medium Phos EN.
Regards to you all
Rod
- Swindon, Wilts, UK
2005
A. Rod,
I can see in the AMSQQP416 is only that electroless can be used instead for cadmium, maybe I'm wrong.
To activate EN deposit you can do it in a sulfuric acid cathodic until the EN deposit starting gassing. Go directly to a rinse and than to the cadmium solution. Remember the sulfuric acid should be very clean from contamination and also the lead anode.
Regards
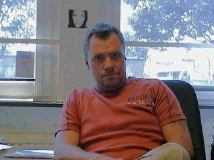
Anders Sundman
4th Generation Surface Engineering
Consultant - Arvika,
Sweden
2005
Q, A, or Comment on THIS thread -or- Start a NEW Thread