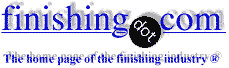
-----
Fasteners Breaking under load
Forging part Breaking strength fails after the yellow zinc plating process
Q. I am facing issues in the Forging part which is being used in Cargo industries. These parts undergo a breaking strength test and pass the test before the plating process. However, 70% of the parts fail after the plating process (Yellow zinc passivation). Need support to resolve this issue.
Harish Mahale- Bangalore, Karnataka
May 13, 2024
by Polyanskiy & Belyaev
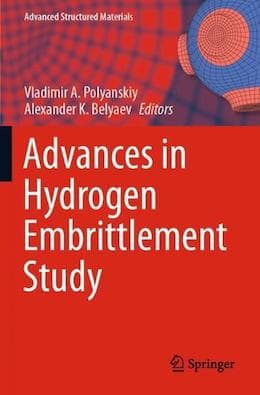
on eBay or Amazon
or AbeBooks
(affil link)
A. Hi Harish.
After plating are the parts immediately baked for hydrogen embrittlement relief? If not, that is almost surely the problem.
Your plating sequence will probably have to change, unfortunately; you will probably have to plate, then bake, then activate and chromate.
Luck & Regards,
Ted Mooney, P.E. RET
Striving to live Aloha
(Ted can offer longterm or instant help)
finishing.com - Pine Beach, New Jersey
⇩ Related postings, oldest first ⇩
Q. Fasteners Breaking under load, Hydrogen Embrittlement? We are a large electroplating job shop in Mexico City, currently we are zinc plating (5 microns) some fasteners that do not require Embrittlement Relief since the steel is a low carbon without any heat treatment(1018 Steel). The only special thing about the fasteners is that they have a flat part between the shaft and the head, and I'm told requires a special manufacturing procedure. The Zinc process is a conventional cyanide zinc plating.
Our client has experienced problems when using the mentioned fasteners, after installed in an aluminum treaded base they break under a torque of 22 lbs/in2.
You can see in the picture where the break occurs, this is a clean break from the shaft and the flat base, like a laminate is being lifted from the base. We have tried also with Embrittlement Relief for 4 hrs 195°C and the results are the same.
Our client tests the fasteners without zinc plate and they don't break, also they have used Aluminum fasteners and they don't break.
Any suggestions? We think it has more to do with the manufacturing process than the plating process. Would an "fluidizing agent or additive" help in any way?
Thanks for your help,
plating shop - Mexico City, DF, Mexico
2005
A. I doubt if 1018 is suffering from h2 embrittlement, especially if a post plate heat treatment makes no difference. You might be having a slight reduction in thickness in a critical spot during the plating prep process. Remember, acid will attack a highly stressed area faster than the rest of the part. I will guess that the plating on the threads is causing you to reach the full allowed torque before the head is seated as it should in the unplated part. (sloppier fit). There is a possibility that it is actually exceeding that torque as it is not a static reading as in the unplated part.
Options might be a redesigned part to use a thicker fragile section, truncate your threads a little bit more or switch to a stronger steel.
- Navarre, Florida
by Michihiko Nagumo
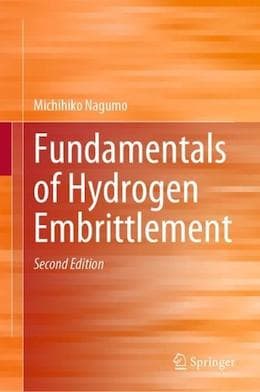
on eBay or Amazon
or AbeBooks
(affil link)
(includes 7 papers / 34 pages on electroplating)
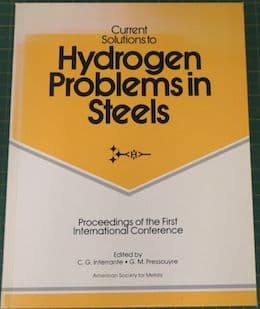
on eBay or Amazon
(affil link)
A. Carlos
You could try the following.
- Plate a small test load with acid zinc. Then test the parts without de embrittlement. And with De embrittlement. Make a note of the difference.
-Use a Torque tension fluid or product that is sold by many US companies which reduces friction at high torque levels.
- Try moving away from Cyanide zinc as it is 70 percent efficient and lots of Hydrogen is generated by 30 percent of the current passed creating Hydrogen.. causing Hydrogen embrittlement.
- From the photographs the bolt looks particularly weak where the break occurred. Does it always break off at the same spot ? Maybe design can take a look.
Check all this first. Look seriously at Acid Zinc Plating.
Hope this helps.
Good luck
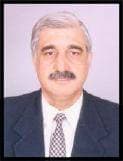
Asif Nurie [deceased] [deceased]
- New Delhi, India
With deep sadness we acknowledge the passing of Asif on Jan 24, 2016
Q. James and Asif,
Thank you very much for your help.
We think the problem has more to do with manufacture and not plating, but the un-plated ones do not break.
James, If the plating on the threads is causing us to reach the full allowed torque before the head is seated, what can we do about it? Would a torque tension fluid help here?
Asif, yes, it always break off at the same spot ? We also have available acid zinc, we have used in this case and the results are the same. Our client argues that because this doesn't happen before plating is applied, the blame is with us!
There is also another client who used 12L14 and now switched to 1022 and forges their fasteners, the torque test is O.K., but they fail another test, where they bend the shaft and it breaks as caramel candy.
Any suggestions?
Thanks for your help
plating shop - Mexico City, DF, Mexico
A. Just a thought, but is it possible that the fact that the fasteners are failing is because the plated surfaces have reduced friction properties and the applied torque is resulting in higher than designed for stresses by developing excessive clamping forces in this critical area. Your unplated fasteners would not exhibit this. Some fastener specs here specify a reduction in torque setting if lubricating oil is used.
Just a thought - best of luck
- Plymouth, Devon, UK
A. Carlos, I personally think that it is a design problem since plating followed by a bake still failed.
Plating causing the problem must (might)then be caused by the greater thickness of the major diameter causing an increase in torque. But, you say that it is torqued to the same value. Is this torque measured by a calibrated torque wrench or by a slip function like you find on many drill motors now. If it is the later, they have a huge range of values. If it is the major diameter causing the problem, reduce the diameter (and mark) a handful of the bolts and plate in with a full batch. If they still break, try less plating if you can still meet QC test requirements.
- Navarre, Florida
A. That is the internal cracks, which are invisible from outside.
Nearly never such cracks are a consequence of raw material irregularities and hydrogen embrittlement.
In most cases the heading pressure was too high during cold forming, that mean too much material when wire feed in or too high pressure in certain step during forming.
The displaced material could no more flow freely.
Extremely high internal stresses were created. They produced the cracks.
With wedge tensile tests such nonconforming products would easily be detected. Such screws would never break in the thread but in the cracked head.
But for such controls wedge tensile tests are far too expensive. Head soundness tests are easy to perform and very cheap.
- Jiangsu, China
2006
A. The fracture appears to be taking place at the forging line associated with the production of the fastener head. Since this is un-heat treated 1018 steel, it will be well below 30 HRC and should not be subject to hydrogen embrittlement. Electron microscopy will probably not reveal an intergranular separation characteristic of hydrogen embrittlement.
If the fastener supplier values the ability to offer the zinc plated version, they may be able to change the head forging process to re-locate the forging line further into the head.
Steve Schatz
- Fort Wayne, Indiana, USA
March 23, 2011
Q. We need to Tin plate a Brass fastener and parts are breaking under load. Can we bake the Tin plated part? What temperature? We are used to bake carbon Steel parts at 200 °C for 4 hours, is it the same for this brass part with Tin plating? What is the fusion temp. of Tin?
Parts need to withstand a Torque of 40 ft-lb, and before plating are in a value of 45 ft-lb, but after plating torque is 33 to 18 lb-ft
The base material is High Strength Brass ASTM 955, (Brass with Silicon or Silicon Bronze) Tin Thickness is 0.0002" to 0.0005"
The part is Forged, machined and then heat treated; Harden at 890 °C then quenched in water, followed by an air blast -tempering at 650 °C
Client requirement is to have a max Rc 53 minimum Rc 38 and parts are being found lower than this value after plating.
Please advise regarding baking procedure and any other important fact regarding this process
Thank you for your help
- Guadalajara, Jalisco
2005
Bolt heads shear off of zinc plated hardware
Q. We use zinc plated hardware for bolting in our process. The tendency is that when bolts are torqued, the bolt heads are sheared off. We found that this happened when we coated the blackodised bolts with zinc coating. Is there any problem with zinc coating process or the method used? Please suggest me how can we use zinc coated bolts for assembly activities.
Sumit babel
- pune India
February 11, 2014
A. Hi Sumit. I think there is a possible minor issue here, and a possible major one.
The minor issue is that different coatings on fasteners exhibit different coefficients of friction and different stick-slip characteristics, and have different thicknesses, such that when you change coatings you may need to re-examine torquing values, the need for lubricants, thread clearances, etc.
The MAJOR issue is that you may have a hydrogen embrittlement problem. What grade (strength) fasteners are you using, who is plating them, are they baked after plating, and is anybody running hydrogen embrittlement tests? Good luck.
Regards,
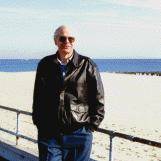
Ted Mooney, P.E.
Striving to live Aloha
(Ted can offer longterm or instant help)
finishing.com - Pine Beach, New Jersey
Q, A, or Comment on THIS thread -or- Start a NEW Thread