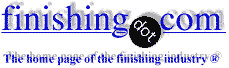
-----
Need painting process for 99 inch enclosures
We are going to manufacture 99 inch enclosures for server and networking racks. I want to know what kinda finish is required in these enclosures and what should be the pre-treatment and painting process for such jobs. We are mainly in powder coating business. We want some appealing aesthetic look on our enclosures. can someone help?
Second question,we are using CRC sheets for our enclosures and also for inner profile, can we go for extruded aluminium for inner profile? and if yes then why and what are the advantages and disadvantages?
UL - New Delhi, India
2005
My knowledge may be dated, Manish, but 19 inch enclosures have been a standard for decades while I've never heard of 99 inch enclosures. Is this a repeated typo perhaps?
This is a metal finishing site and your questions seem to extend well beyond that. You need an industrial designer to come up with the appealing aesthetic look for your enclosures, which may include engraving or brushing and/or attachment of nametags/logos/insignia, etc. And you need an electrical engineer to decide whether aluminum can be substituted for CRS.
Once you know the look you want, and the material of construction, then you can consider the finishes. Aluminum can be anodized as a final finish in lieu of paint, if you like, while CRS would require phosphatizing and painting, or perhaps electrophoretic lacquering.
Get back to us when you're a bit further down the road please. Thanks and good luck.
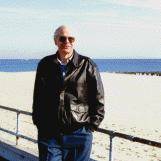
Ted Mooney, P.E.
Striving to live Aloha
(Ted can offer longterm or instant help)
finishing.com - Pine Beach, New Jersey
2005
I am sorry Mr.Ted, It was misprinted at 99 inches.You are right it is 19 inches enclosure.
I have one more question to you. We have a 10 tank hot tri-cationic phosphating spray system.We use both TIG and MIG welding while fabricating our enclosure.The carbon scale deposition during welding process in inside corners of the closure has become headache for me. It doesn't get removed during our phosphating process and there is no phosphating coating comes over this. Will this create rusting at that part in future as it is not phosphated? What is the solution for this problem.I don't want to go for de-rusting process because that will require 2 more tanks and I have no scope of adding a single tank.
Can you help in this regard?
UL - India
2005
The welds could be sandblasted instead of chemically treated, but that might be even more complex and time-consuming--it's hard to tell from here. But you have to do something! The weld areas will be 'hot spots' that tend to anodically corrode anyway; if they remain un-phosphated, your process won't work.
As for the details of how to best apply those 10 available tanks, though, now you are into an area where a specialist in pretreatment chemistry can offer you a lot more expertise than I.
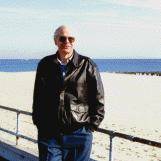
Ted Mooney, P.E.
Striving to live Aloha
(Ted can offer longterm or instant help)
finishing.com - Pine Beach, New Jersey
2005
Thanx Ted for your valuable support. Yes its in my mind how to use ten tank process for such problem but thats the last option I have . I want to go for some other option which can work without any hard work. Sand blasting and acid descaling I don't want. Though there are some chemicals available in the market which can be sprayed at that portion which will not only remove the rust or scale but will also protect it with some coating.
You are quite experienced with finishing job work so I expect a suitable answer from your side and I am sure you are the only person who can get me out of this problem. If I use one of my tank for descaling then its going to increase the cost as well as it needs 2 water rinsing stage also as the coming next stage is alkali activation. If I use only one rinsing stage then, there is quite possibility to change frequently the activation bath(twice or thrice a week).
I have one more question to you . I have worked with one of the CED paint shop (Set up Jeorge & Kosh ,USA) and it has also 10 tank hot tri-cationic spray phosphating system.Our third stage was de-rusting stage. My question to you that why can't we have first de-rusting stage then water rinsing and then degreasing and then the next stages? What's wrong in this sequence?
- India
2005
Q, A, or Comment on THIS thread -or- Start a NEW Thread