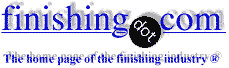
-----
Proper tumbling method for 420 SS
I work for a rotary cutting instrument company specializing in dental drills. My question is about tumbling to clean up surface appearance. I am working with 420 Stainless Steel in small cylinders
(1/16" diam.x 1.5" long). During a welding process to Tungsten-Carbide, a small area of the steel shows surface burning just under the weld.
My quest is to remove this burnt appearance without reshaping or resizing the part. I am leaning toward a batch tumbling operation, but I am not familar with what media to use, or how to make the right slurry in order to achieve a bright, shiny finish. I have access to a turbula tumbler, I just don't know what to put in the jar with the parts.
rotary cutting. - Lakewood, New Jersey
2005
There are 2 ways to go here. You can either use a wet process or a dry process. The dry process involves the use of treated dry ogranic media. This will produce a mirror finish, but it will take a long time and because of its small particle size, there might be some lodging in the tubular section. If you go that route you need to consider ultrasonic cleaning after processing. The wet process means the use of either steel or porcelain media which is non-abrasive. The chemical compound is important and I probably suggest the use of porcelain because it is lighter than steel media. Steel will work faster, but it may distort your parts. Lastly, you might be able to use a magnetic tumbler.

AF Kenton
retired business owner - Hatboro, Pennsylvania
2005
Use an oblique barrel. Use 2 to 3 washes of ⇦liquid caustic soda in bulk on Amazon [affil link] in water. approx. 1 kg caustic in 20 liters of water. Load the parts in barrel and submerge them in caustic sol'n and then tumble them at 40 rpm. After the soln turn slightly black change it and repeat till you get a bright polish. Polishing time will be approx. 6 hrs.
A DOS- India
2005
420 stainless steel dental drills can be easily electropolished in saline-based solution. Instead of 6 hours mechanical tumbling it will take you 20-30 minutes depending on initial surface preparation. Complex form is ok, sharpened knifes can remain sharp if needed. Dental instruments are polished with plastic parts unharmed. The surface becomes passivated and survives without rust in humid conditions. Surface is surgically clean after electropolishing and do not contain any abrasives in comparison to mechanical cleaning. Contact us if you need more information.
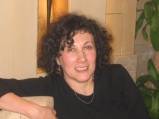
Anna Berkovich
Russamer Lab

Pittsburgh, Pennsylvania
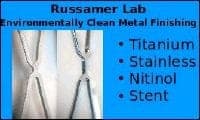
2005
Q, A, or Comment on THIS thread -or- Start a NEW Thread