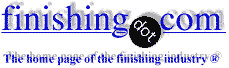
-----
Designing a dip paint tank
Q. I'm having problems with paint adhesion using a crude dip painting process and want to improve my process by designing a new dip tank with the needed features to produce good predictable results. The paint I am using is a silicone based high heat aluminum paint to coat steel finned electric heating elements. The elements have a thin (18 Ga.)steel strip material wound on edge in a fairly tight helix (1 "fin" / .125") the length of the element. The fin material is furnace brazed to the elements using copper so the surface is free from oils but heavily oxidized.
I think the paint adhesion problem is related to solvent entrapment since we dip then air cure for 2 hours then bake cure. The paint seems to have the most adherence problems where it is the thickest and solvent is being trapped, usually on flat surfaces. The baking process seems to volatilize the trapped solvent and lift the paint from the surface forming a "blister".
I am interested in agitation and filtration methods for the dip tank and anything I can do to get better paint adhesion.
Chris Ospital- Ogden, Utah, USA
2004
A. Someone might ask the question concerning whether or not it's going to matter what kind of cleaning system you use, it seems the problem would be that you need to pre-bake (dry-out)the parts before paint to make sure that there is no trapped moisture. I think I would suggest getting another oven to pre-bake the parts before upgrading the dip system.
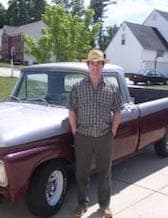
Sheldon Taylor
supply chain electronics
Wake Forest, North Carolina
2004
A. The heating elements have been furnace brazed at high temperatures so they are dry and at room tempurature before painting. The solvent being trapped is from the paint itself. As the surface of the paint dries over thicker areas, the remaining solvent that is trapped under the "skin" has a tougher time evaporting and when heated it vaporizes causing the adhesion problems. I'm looking for tips for a small dip tank design (skimmers, agitators, pumps, etc.) and any help with the processing steps that may be critical.
Chris Ospital- Ogden, Utah, USA
2005
A. Chris, during the last 25 years I've often seen the problems you describe,
The causes I saw (and still see) mostly:
1. Too high film thickness (wet or dry) Try to prevent excessive paint thickness by turning and moving the parts in an appropriate way immediately after dripping.
2. Too short or too ineffective flash-off. Normally 2 hours should be OK. Is there any air movement around the parts during this period? Is the room ventilated with a certain amount of fresh air thus preventing a too high concentration of evaporated solvent? This would reduce the evaporation speed. What about the temp. in the flash-off area? I've seen too high temps, causing the paint to "pre-cure" before entering the oven
3. Paint viscosity: is visc. still ok? Having a big dip tank can lead to excessive turn-over times of the paint. Fast evaporating solvents will go first with as result that the "solvent mix" in the paint changes over the time. Have your paint supplier checked this, or even better, try coating a part in "fresh" paint
By the way: your description of the possible cause of the problem is correct!
Good luck,
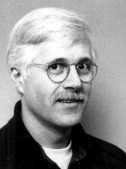
Remmelt Bosklopper
- Enschede, The Netherlands
2005
Q. I want ask the details about Dip Painting process for a wire condenser assembled in a refrigerator. i.e.what should be viscosity of paint? What should be oven temp to be maintain? How much time new paint is used? What is derusting process required before Dip painting? What soln is required for derusting?
Sachin Selmokar- Pune, Maharashtra, India
May 16, 2012
Q, A, or Comment on THIS thread -or- Start a NEW Thread