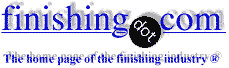
-----
Plating and anodizing engine parts to reduce wear and friction
2004
Hi,
I'm working on a new type of engine and I had some questions about surface finishes, plating and anodizing to reduce wear and friction and I was hoping some of the experts could help me out.
The engine combines certain elements of rotary and piston driven engines. It will operate at lower pressures and temperatures than normal engines and be constantly exposed to moisture. For this reason I plan to use aluminum for most of the parts because most iron or steel would rust and the extra structural strength really isn't needed. However, I have read that aluminum wears rather rapidly and that you shouldn't have the same type of material rubbing against itself. Also I should note that using a significant amount stainless steel or titanium would be too expensive.
There are 2 parts of the engine were sliding friction occurs and that's what I have a question about. Both of these will be lubricated with motor oil. My first question is what is generally the best surface finish to reduce friction? I have heard that smoother isn't always better because in slighter rougher surfaces oil has little cavities it can get stuck in. Is that right or not? I was also considering using an industrial chrome plating or a hard anodizing of some aluminum parts to reduce friction or else using some materials like bronze or brass that might have better wear characteristics. Which of these combinations would likely reduce wear and friction the best and within the best combination which surface would wear the quickest? And if there are any better combinations I am missing please suggest it.
1) Chrome plated aluminum rubbing against anodized aluminum
2) Chrome plated aluminum rubbing against a material like bronze or brass
3) Anodized aluminum rubbing against a material like bronze or brass
4) Two different materials like bronze and brass
Also how thick do they usually make industrial chrome plating and hard anodizing or does it vary? And does plating or anodizing affect the surface finish at all?
Thanks for your help.
Mike Marquardinventor - Kennett Square, Pennsylvania, USA
Q, A, or Comment on THIS thread -or- Start a NEW Thread