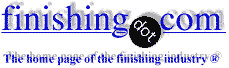
-----
Hydrogen Embrittlement in Armor Steel
I am working with some 46100 (400-500 brinnell) steels used in vehicle armor and am concerned with Hydrogen Embrittlement(HE). These parts are being cleaned with a caustic alkaline solution and then iron phosphated. Can HE be induced with this type of cleaning process? If so, my understanding is that once affected with HE, unless the part is relieved at a certain temperature in an oven, the part will always be suspect? Is this the correct line of thinking? I would be interested in some literature written in plain language speaking to HE and it's effect on metal. Any suggestions?
Victor Dobneyvehicle armor plate - Phoenix, Arizona, USA
2004
There has to be a source of hydrogen to get embrittlement. an alkaline soak does not generate hydrogen. a cathodic electroclean does, but I doubt if you are doing that. The phosphate process is acidic, but it generates very very little Hydrogen, so is negligible. I doubt if you could get a reading using the specialized sophisticated equipment for checking for hydrogen embrittlement. I think that there is only one company in the USA that makes the equipment. Expensive. Why do you think that you have a problem?
James Watts- Navarre, Florida
2004
These parts are supposed to be cleaned with a mechanical abrasive process per TT-C-490 [from DLA] (method 1) so I was under the impression that cleaning with the above method could induce HE into my parts and cause some problems.
Victor Dobney- Phoenix, Arizona, USA
2004
The reason is phosphate requires a clean and active surface which abrasive blasting is the best method of attaining both. If you need more production, take a look at a pressure system vs a siphon system. Control the grit size and pressure and you can get virtually any roughness of finish that you want. I never worked with iron phosphate, only zinc and Mn, and I would not consider any other method.
James Watts- Navarre, Florida
2004
Q, A, or Comment on THIS thread -or- Start a NEW Thread