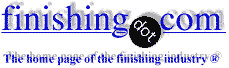
-----
Waste water
1999
Anyone know which flocculating agent is best for alkaline non cyanide and cyanide zinc waste water treatment?
Also is it best to have a conical bottomed tank or a lamella cross flow settler to settle out the solids?
any help on these matters would be most appreciated.
- united kingdom
1999
An anionic polymer is usually considered best for metal hydroxide wastewater.
The best type of clarifier is a matter of opinion only, since I am not aware of any applicable published studies. But my own experience is: the surface area of the clarifier is the most crucial element for two reasons:
First, what you are trying to do is to have the slowest practical rise rate, so that the solids fall faster than the water rises. While slant tubes and lamella plates can help, both by distributing the flow to minimize short circuits, and in decreasing the distance a particle has to fall before agglomerating, they can do only so much; you just must have a generous surface area.
Second, many plating shops, especially as we grow more conscious of reducing flow rates, have a very solids-heavy waste stream; the sludge holding capacity of some clarifiers is too low, but the larger the surface area, in general, the greater the holding capacity.
So, whether the clarifier be round or rectangular in surface, the one with the bigger surface area usually gets my vote.
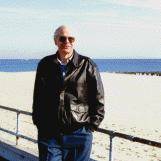
Ted Mooney, P.E.
Striving to live Aloha
(Ted can offer longterm or instant help)
finishing.com - Pine Beach, New Jersey
I have had good luck, with this type of waste, with flocculants that come as emulsion concentrates, rather than solids. These are medium charge density flocs with a low to medium charge density. The company that manufactures the polymer (there are many) will usually be glad to send out a rep to try a number of different flocs out on your waste. A little ferrous sulfate
⇦ on
eBay or
Amazon [affil link] added prior to pH adjustment will help effluent clarity.
Are you doing batch treatment? In that case, a conical bottom tank is a good choice for solids separation. On the other hand, if you are running a continuous flow system, a clarifier is better. The upflow, lamellar style clarifier is a little more space intensive than the side flow type.
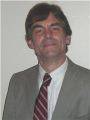
Dave Wichern
Consultant - The Bronx, New York
1999
1999
Hi George ,
I am in favour of the upward flow conical bottom settlement tank , but there are a few rules to design it by , lets set some parameters first .
1 ) to achieve maximum settling you must choose your neutralizing agent carefully , I always use lime as this usually rules out the need for flocculant , sure its a little messy , and produces more sludge , but the sludge itself usually meets the commonly applied
"Leachate" test demanded by environmental authorities .
2 ) the Upward Flow Settlement tank MUST operate under constant flow conditions , that is to say the pump feeding it MUST NOT turn off more frequently than once in 2 hours for a very short time preferably not turn off at all .
3 ) the height of the cylindrical part of the settlement tank must be 2.5 times the diameter of the tank ,& the volume of this cylindrical part of the tank should be equal to 4 hours flow rate of your discharge , the cone angle must be 60 degrees , the sludge should be drawn off at least twice a dat to a concentrating tank fitted with a floating decant valve so that the maximum amount of water is removed before the filter press operates and produces a good solid cake . Using these simple calculations and operating procedures you will achieve your best results
regards

John Tenison - Woods
- Victoria Australia
Points 1 and 2 taken, John, and part of 3 -- but I can't see the advantage of the height being 2.5 times the diameter. It has to be tall enough to allow tube modules or lamella plates, I guess, but ...
the taller the tank, for a given volume, the smaller in diameter; the smaller the diameter, the higher the rise velocity, and therefore the more difficult for floc particles to fall. What do you think I'm missing?
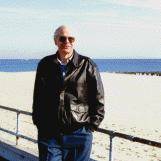
Ted Mooney, P.E.
Striving to live Aloha
(Ted can offer longterm or instant help)
finishing.com - Pine Beach, New Jersey
1999
I am trying to design an efficient clarifier to treat pig ( swine ) waste (remove TSS). I was going to use lamella plates with 3 hr detention time and a design overflow rate of 400 gpm/ft2 Any comments?
David Bromley- Vancouver, B.C., Canada
2001
Q, A, or Comment on THIS thread -or- Start a NEW Thread