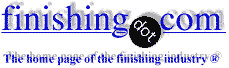
-----
Adhesion problem of Rhodium on Nickel on Brass
I'm having serious problems getting adhesion of rhodium on sulfamate nickel over brass. right now I'm using sulfuric acid to activate no rinse, going in live, but results are not consistent. I've tried everything I know of. If anyone has any suggestions. I've been working on this for 2 months.
Chris finch- Seattle WA.
1999
1999
Hi Chris,
Is there any delay between nickel plating and the rhodium? Best results would be obtained plating the rhodium immediately after the nickel. If that does not work or is not feasible the use of a Woods nickel strike after your sulfuric dip (with good rinsing in between
)should solve the problem. You might also try 5-10% HCl instead of the sulfuric. That might give you better activation. Just remember always rinse well before the rhodium tank to keep the chlorides out.
Dayton, Ohio
Hi Chris ,
For activating EN deposits I would recommend 10% HCl Cathodically
, that is with the workpiece Cathodic .
You should get adhesion every time , but rinse well before the Rhodium ! regards

John Tenison - Woods
- Victoria Australia
1999
I plated Rh onto BE Cu pins for a connector division. they had to pass 1200 F post bake. You said brass as the base metal...? the Rh in my case was plated over a acid gold strike, over electroless nickel (mid phos) over a sulfamate Ni strike or woods strike. The reason for the gold strike was the gold was much more receptive to accepting the Rh. did it add cost? no.............because there was no rework. what works...works. is this a barrel or rack application. barrel plating Rh requires excellent loading in so much that no loss of continuity from part to part can take place. lots to consider.
Todd Huehn- Blain, Minnesota
1999
Q, A, or Comment on THIS thread -or- Start a NEW Thread