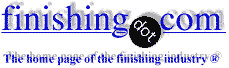
-----
Problem holding Zinc concentration in alkaline Zinc plating bath
Current question and answers:
March 9, 2021Q. Hi Everyone!!
Need help in understanding required amount/ Area of Zinc to be maintained in generation tank for proper replenishment of Zinc metal in plating tank. Process information is as below-
1. Process: Alkaline Zinc Plating, where Base is Potassium Hydroxide.
2. Plating capacity/ hr: 107 sq. meter (Average)
3. Zinc consumption/ hr: 5.32 kg (approx. with 7 micron average thickness)
4. Size of Zinc slab: (48 x 24 x 5) cm
5. Total volume (including plating tank and generation tank): 28500 ltrs (of which 6000 is volume of generation tank)
Currently we have capacity of 90 Zinc slabs in generation tank and operating condition is maintained b/w 25- 35 °C, but we are facing problem of continuous decrease in concentration of Zinc. So please help me in understanding no. of Zinc anodes required in generation tank to achieve 5.5 kg of Zinc metal per hour (Please note that Zinc slabs are covered with fine MS sheet from top also so contact point of one Zinc slab in present condition is 2304 square centimeters).
- New Delhi, India
March 2021
A. Hi Pankaj. There are several terrific articles available, like "E-Brite Ultra Alk Alkaline Non-Cyanide Zinc Plating Process" from EPI [a finishing.com supporting advertiser] and https://www.columbiachemical.com/wp-content/uploads/Article-ZincGeneratorTanksForAlkalineZincPlaters.pdf -->
which detail what the zinc and starter concentration should be, how to easily verify the ratio with a Hull Cell
⇦ huh?
, how to calculate the required size and zinc capacity of the generation tank, and several alternate ways to design it.
You apparently recognize that good galvanic contact between the steel and the zinc is required in order to generate the galvanic current necessary to dissolve the zinc fast enough. So I would suggest first comparing your numbers to what those two articles or others suggest in order to determine whether what you have should be adequate to maintain concentration. If it should be, but it isn't, then I would suspect that perhaps something is amiss with this "fine MS sheet" arrangement you speak of, but which I am not picturing. A sketch or photo to mooney@finishing.com for posting here might help.
Luck & Regards,
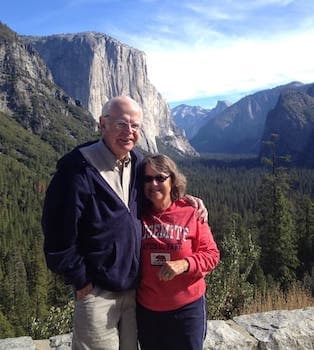
Ted Mooney, P.E. RET
Striving to live Aloha
(Ted can offer longterm or instant help)
finishing.com - Pine Beach, New Jersey
A. Hi Everyone!
You are using more zinc and less produce zinc to galvanize reaction.
Make sure potassium hydroxide concentration and temperature within limit and enough zinc slabs into regeneration tank.
Your generation tank produces less zinc than your process tank.
Need mixer in generation tank; make sure potassium hydroxide concentration is within limit; check that temperature in generation tank within spec. Descale your steel baskets where you add zinc slab.
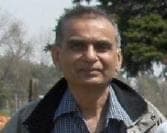
Popatbhai B. Patel
electroplating consultant - Roseville, Michigan
March 12, 2021
March 21, 2022
A. Hi, Pankaj Chaudhary.
I think your system started should be fine, but suddenly there is a problem with the concentration of zinc.
I want you to try to check what you can visually first.
1.Chemical flow from the overflow of the plating tank. Is it convenient flow to the solution tank?
The pipe size too small? It should be large, at least three hundred percent of the return pipe from the filter. (The design should not save this pipe).
2.Placing the steel basket in the solution tank, does it block the flow of chemical? If the basket arrangement is not good, ingot zinc or balls will not dissolve well, resulting in the zinc flow back to the plating tank is not concentrated enough.
3. Chemical return pipe From filters to plating tanks --
At the outlet pipe, is the solution evenly distributed?
If you spread only one point the concentration in the plating tank at each point is not the same.
Therefore, you need to split the end of the return pipe at more than one point. (The more the better)
4.Easier. Do it now --
When was the last time you checked for blockages in your filter?
Employee - PHANTHONG, Thailand
⇩ Related postings, oldest first ⇩
Q. We have non cyanide, alkaline zinc bath and we have a lot of problems to maintain concentration in this bath. The volume of "working" bath is about 5000 liters, the volume of dissolving bath is about 2000 liters. We have about 2000 kg of small pieces of Zn in 130 iron baskets (7cm*7cm*110cm) in the dissolving bath.
We have 5 rectifiers (18v, 800A each)
My questions are:"What is the white sand, that I have found in Zn-dissolving bath"; "Is this normal, that during the work concentration of Zn is falling"
Dimitrij Usplating shop - Kranj, Slovenija, Slovenija (EU)
2004
A. You should have more than enough zinc dissolving to maintain the concentration. Your problem should be in keeping the zinc concentration down to a manageable level with that setup.
What concentration are you running the NAOH at and what temperature is the plating solution running at? Are you dissolving zinc and then adding the solution to the plating bath or is the plating solution being continually replenished by 'enriched' solution?
Dougie Lightfoot- Fife, Scotland
2004
Q. Concentration of NaOH is between 90 and 100 g/l, temperature of plating bath is about 25° C, Zn is dissolving in separate bath and is continuously pumped (filtered) in the plating bath. Flow of the pump is approx. 4000 l/h. Another problem is sludge (white sand ZnO?), that we have in dissolving tank (really a lot). Every two months we have to clean the bath and Zn pieces.... Also we have to change filter candles every three days and that cost us a lot...
Dimitrij Us [returning]plating shop - Kranj, Slovenija, Slovenija (EU)
2004
A. I agree with the other reply that you should have sufficient anode weight to maintain the zinc concentration in solution if you are using the correct level of sodium hydroxide (caustic soda ⇦liquid caustic soda in bulk on Amazon [affil link] ). Generally, depending upon individual supplier chemistry the range is from 12 to 20 ounces per gallon (sorry, my clients and I have been referring to things this way not in metrics for 30 years) maintaining a bath zinc metal of 1.6 to 2.4. You should maintain some type of agitation in the zinc generating tank and keep the temperature at 70-85° F. Lower temperatures may cause some precipitates to form.
The sand could be impurities from your anode material. The preferred zinc anode material for alkaline non cyanide baths is 99.99% pure.
I hope this is somewhat helpful
Gene Packmanprocess supplier - Great Neck, New York
2004
2004
A. Dimitrij,
For how long time has you used your alkali zinc solution?
It could be carbonate from the NaOH you see. What types of anode sheet did you use? please tell me more so I can solve your problems.
Regards
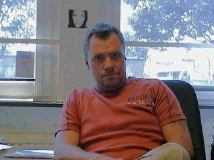
Anders Sundman
4th Generation Surface Engineering
Consultant - Arvika,
Sweden
Q. Dear Mr.Sundman
We are using this bath from February this year. Anodes (in bath) are made of Nickel-plated Iron. The sand in dissolving bath is not a carbonate. Amount of carbonate in bath is (for now) low enough, and it is not causing us problems.
Dimitrij Us [returning]- Kranj, Slovenija (EU)
2004
A. I obviously don't know the characteristics of your particular solution but your NaOH seems far too low. It should be up near 140 g/l. Doesn't your solution come with a technical data sheet and supplier back up?
Haven't experienced the 'white sand' problem before but I agree with Gene that contaminants from the anodes is a likely source. Na2CO3 shouldn't be a problem unless the concentration rises above 100 g/l (although newer chemistry can cope with this figure). It wouldn't come out of solution anyway unless the temperature fell below 5 °C (41 °F).
Dougie Lightfoot- Scotland
2004
2004
A. Hello Dimitrij
I came in just now and do agree with most of what has been said so far.
Factors that affect Zinc Generator performance are listed and you could check these out.
- Caustic should be around 125 gpl and above to ensure effective dissolution of zinc. 140 is really good if your supplier has the right system that works at this level..
- The iron used for the baskets should have been treated as follows before first use.. .. Clean. Light pickle to remove rust if any. Rinse. dry. Then use a blowlamp to heat the basket till it develops a bluish film all over, It has been seen that this film helps dissolution of zinc in caustic solutions and this is how we do it . Baskets treated this way work very well..
- The purity of the zinc is definitely important. 99.99
- Lack of caustic will tend to polarise the dissolution and cause a white coating over the anodes.
- Light air agitation helps dissolve zinc.
-Temperature above 20 centigrade is recommended.
- A low energy Mild steel heater can be used in winters to control temperature around 25 Centigrade.
- Check the white powder for zinc content. If it is zinc that is oxidised and won't react with caustic then it is a sign your caustic was low.
I hope this helps.
Regards
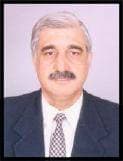
Asif Nurie [deceased]
- New Delhi, India
With deep regret we sadly advise that Asif passed away on Jan 24, 2016
A. Dimitrij,
All answers here are good enough to solve your problem I think. You should analyze your zinc anodes to see if they are 99,99 zinc.
Regards
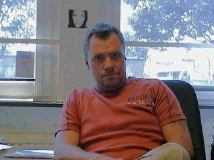
Anders Sundman
4th Generation Surface Engineering
Consultant - Arvika,
Sweden
2004
A. Hello,
It was interesting to read information on solution to the problems with Zn bath. I read at many places that purity of Zn anodes is of high significance in Zn plating process.
Mr. Dimitrij, I would appreciate if you could let me know what kind of Zn solution do you use..is it sulphate/ chloride.. When you say you are running a alkaline bath, what is the pH of your solution?
Many Thanks.
With Regards,
Pankaj Gupta- Baton Rouge, Louisiana
2004
Dear Mr. Pankaj
I have newer measured pH of the plating bath, while concentration of NaOH is about 120-140 g/l. So high enough, that we can say that the pH value is more than 13...
In alkaline bath, there's no sulphate or chloride ions (maybe as impurity), since Zn is dissolving in NaOH solution (that goes just when Zn is in contact with another metal, that has such potential, that Hydrogen can build...) in zincate ion... a form of tetra hydroxy "complex" zinc ion...
Best regards!
Dimitrij
Dimitrij Us [returning]- Kranj - Slovenija (EU)
2004
2005
A. Dear Dimitrji, Dear Asif,
With interest I've followed the suggestions to eliminate the problems Dimitrji had in his production. In fact I do absolutely agree to the suggestions of Asif.
Q. But what is very new for me is the recommendation to heat up the anode (iron) basket to develop a thin oxide layer for a better dissolving reaction of the zinc-anodes. We also had a lot of problems of dissolving zinc and especially with developing of sludge. The anode purity was one we could figure out to dissolve problems at customers. The other was to plate the iron baskets with an activation layer (nickel) for a better dissolving, but this is in fact quite expensive, especially if you have to buy them.
Asif, you have written that your dissolving reaction is very well, what does it mean (how many g/l/h)? Also, is there a certain temperature which you use to activate the baskets? Did you do this process in a oven (with or without external supply of oxygen?)?
Thanks in advance,
Best regards,
Dominik Michalek- Mexico City, Mexico
2005
A. Dear Dominik
Just saw your posting . Here are the reasons for what was suggested.
Mild steel basket with a bluish oxide layer on them , in contact with zinc, immersed in a caustic solution set up an excellent electrochemical couple that speedily dissolves zinc.
This light bluish film of oxide is required to be created once, when new baskets are about to be installed. A gas blowtorch with the light blue flame stationed on steel moved lightly and uniformly will form the film.
Light agitation be it mechanical, solution recirculation or light air only in the generator helps prevent solution stagnation and anode polarization.
We now design alkaline zinc tanks with the zinc generator as part of the working bath. One end of the bath contains static anode baskets. With zinc in them. The filter draw a solution from the non working end which is the generator end and discharges the filtered solution into the other far end, setting up a nice circulation.
We use mild steel anodes to pass current. Maintain caustic around 125 to 135 and the zinc stays above 12 gpl most of the year. North Indian winters call for low energy heater to maintain 22 °C when ambient falls to 5 °C.
There is no advantage with Nickel plating anode baskets. Its an older technique that has been discontinued with the newer brightener systems. The mild steel baskets get a little too active in summer and we have to remove some anode to keep the zinc from climbing past the 20 gpl mark. Yes the system works well.
I hope I was able to provide all the answers ?
Regards,
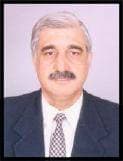
Asif Nurie [deceased]
- New Delhi, India
With deep regret we sadly advise that Asif passed away on Jan 24, 2016
A. Do not use air agitation as it will add to carbonates, I ran a 6800 gal alkaline Zinc bath, I used a plate filter with a 5 micron poly pro cloth on top of plate, this should filter out the sand you refer to,the cloths can be rinsed off to clean and reused for a long time. Mechanical agitation in the generation tank should help dissolution rate. Run the filter intake from this tank to discharge in the process tank.The filter should be changed 3 to 5 times per week. A turnover rate of 1 to 2 times per hour worked for me. A bit of filter aid will help to put a pack on the plates and do a better job of filtration. Maintain your caustic levels and analyze the bath twice per shift.
Hope this helps.
Good luck.
Patrick DusingZinc Plater - Elk Grove, Illinois, USA
2005
2005
A. I would like to add one more comment to this interesting discussion:
When analysing for NaOH, add BaCl2 to make sure that the Na2CO3 precipitates. Otherwise you can get a high incorrect result for NaOH.
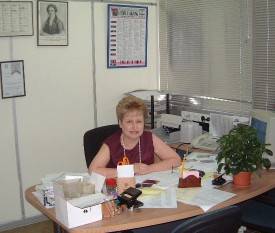

Sara Michaeli
Tel-Aviv-Yafo, Israel
2005
Q. Hello to all, that have answered on my problem. It seems, that we manage to solve the problem. We added agitation in dissolving tank. While there was not enough free space to install a mechanical stirrer, we have installed a pump and pipe with jet injectors mounted on the pipe. We have now two pipes on each wall of the tank. Results are (for now) excellent.
Before we started with 16 g/l Zn at monday and finished on friday with 7g/l Zn. During all the time baskets were fully immersed in electrolyte. Now we have steady concentration of Zn (16 g/l) and baskets are mostly half-immersed.
It seems, that the problem occurred in (much too) high local concentration directly around the Zn pieces in baskets...
I hope that only this was the problem and that in future I will have no reasons to bore everyone with my problems...
When this solution of the problem shows no results in longer period, than we will meet again on this forum :)
Bye!
P.S.
Allow me to apologize to all of you for my poor English language. Years and years have passed since I study English :)
- Kranj, Slovenija (EU) [returning]
Ed. note: The years have been kind to your command of the language, Dimitrij; your English is better than a lot of Americans.
2005
Thanks for a compliment.
I hope, that your compliment will not scare all the others, to give an answer :)
I need some answers regarding to my problem badly....
- Kranj, Slovenija (EU)
2005
Q. Hallo again!
In my last post, I promised, that I will not bore you with my problems... But...
Yes. Problems with Zn concentration are here again.
The solution with pump and jet worked well just one month or two. We have again a lot of sludge in dissolving tank and Zn concentration behaves funny.
Let me describe this:
We start on monday with 16 g/l, concentration is falling till Wednesday, on this day concentration reaches minimum, about 8,5 g/l, from this point it starts to raise, and at the end of the week
(Saturday morning) we have about 11,5 g/l... And so goes each week! Funny really!
Yesterday, I was in one galvanic plant. In this plant, they have rack line. In Zn (alkaline) bath, they have 5 working places, and they are working with 1000 to 1600 Amps per rack-holder (that is twice as much current that we have on our barrel). They have 22000 liters of electrolyte and dissolving tank is SMALLER than ours! They have just
300-500 kg Zn pieces in this tank (we have 2200 kg) and steady concentration of 13 g/l during all day, all week!
If you look at my first post, you can compare this data with data of our plant. What you can see is that they work with double current and three-times more electrolyte.
How is possible, that they have enough Zn, when they have two times higher current and much less Zn in even smaller dissolving tank?
ANSWER:
DISSOLVING TANK THAT THEY HAVE IS MADE OF IRON AND IT IS (ELECTRICALLY) GROUNDED!
The guy, who runs this plant has said to me, that their first dissolving tank was made of plastic (PP). They had problems with concentration all of the time. But, when they put some iron plates (sheet metal) on the walls of this PP container and grounded them, Zinc started to dissolve good! I wonder if anyone of you can find the reason for this?
We can speculate, that velocity of redox reaction of Zn dissolving depends of velocity oh hydrogen forming. That's why a lot of people plated iron baskets with Nickel due to smaller potential difference between H and Ni, comparing H and Fe... But can anybody exactly explain or
clear up this redox reaction, potential difference and ground potential?
Will work for me, if I connect iron baskets (filled with Zn pieces) with ground potential?
Dimitrij
- Kranj, Slovenija (EU)
A. Dimitrij,
It should work as long as there is no electrical circuit. I think this is the theoretical part of it which I will try to verify next week by doing some lab tests. I also will try to measure the potentials which are running through and will post the results asap here at this page.
Asif, I have tried several tests in the lab and in the field at customers your recommendation of bluish oxide film on the anode baskets. The initial dissolving reaction was very very good and very fast (1-1,5g/l/hour), but after a certain time and especially after work breaks (weekends and holidays)the dissolving reaction slowed down, it even stopped completely. After a fresh "oxidizing" of the mild steel anodes with a acetylene/oxygen burner the dissolving reaction was as fast as before. For our application (rotogravure industry)is this kind of dissolving technique not suitably. We run almost the double of zinc metal content in the bath as in conventional zinc plating baths.
As I said above, I make some lab tests with grounded iron sheets and some tests out in the field and will post the results here.
So long,
- Mexico City, Mexico
2005
2005
Q. Dear Dominik!
I have already measured the potential difference between iron baskets and "ground"...
I have connected all the baskets with a wire.
During the construction of our plating line we put quite a lot of steel "tape" under the concrete and leave some points to connect some of the equipment to the ground potential.
So I connected the baskets to the "ground". Volt meter connected between the iron baskets and ground showed about 1V. This is normal, when we consider the redox reaction:
2H(+) + 2e ---> H2 (gas)
Zn - 2e ---> Zn(2+)
Also, there is a normal (just chemical) reaction between Zn and caustic, which leads to a soluble form of a Zn-hydroxy complex.
I think that two things can get bad:
1. velocity of reaction in first step (building of hydrogen); when that slow is, than not enough Zn is dissolved
2. forming of a Zn-oxide, or another compound of a Zn, which is not soluble and precipitates; forms sludge in dissolving tank
For "speeding" the first step, we can use "oxidized" baskets (Fe2O3, FeO, Fe3O4), or Ni-plated baskets, or specially plated baskets whit NiS. Reaction is in first two weeks really fast.
But what is with the second reaction; when we have Zn already dissolved, what happened then?
Everybody says, that ZnO builds, when we "over concentrate" electrolyte (when concentration of Zn2+ is greater than 35 g/l); that's why we must have a good flow through dissolving tank.
But the question is, if also can get something else wrong.
I have noticed (same as you), that during the "not working" period (over the weekend) something must happened;
Let me describe that:
On Monday we had 14 g/l, Tuesday 10 g/l, We 7,8 g/l, Th 9 g/l, Fr 10 g/l, Sa (stop working) 11,2 g/l. From saturday (14.00) to Monday (8.00) we were not working, Zn pieces were mowed out from the electrolyte. Next week comes the same story. From monday to Wednesday, concentration is falling, from Wednesday to Friday, concentration is rising. We are working on 24 hours/day, all the time with 500-800 Amps/barrel....
Really funny, isn't it?
- Kranj, Slovenija (EU)
A. What temperature does the solution fall to over the weekend and what temperature is on Monday, Tuesday ......etc.?
John Martin- Wales
2005
Q. Dear John.
The temperature of plating solution is during the work maintained on
25 °C. Over the weekend, temperature falls on 20 °C (in winter time on 15 °C).
- Kranj, Slovenija (EU)
2005
A. Is your temperature definitely held at a constant 25? I've never seen an installation yet where that was achieved. Obviously if the temperature was lower during the early part of the week then the dissolution rate would be slower. Removing the baskets from the bath may also be part of your problem. Restoring the dissolution process to its previous rate can often take some time after it has been stopped for a while by removing the baskets from the solution.
Also, solution dragout from barrels can be horrendous. Is the NaOH concentration constant? You may want to consider raising that to help to dissolve more zinc.
- Wales
2005
Q. Dear John!
Well, at the beginning of the work, we have lower temperature than 25° C. But after all 5 barrels are in bath, with current around 600 to 800 amps., then 25 degrees are reached less than in one hour.
Let me explain; efficiency of the electrical current in alkaline-non-cyanide Zn bath depends of many conditions, but we can assume, that it can not exceed 85 to 90%. So where goes 10 to 15% of electrical power, that is given on the barrel? Well old scientist, named Newton once said, that energy can not come by itself and can not disappear, but it can transform itself from one form to another. And so it is here... Electrical energy from the rectifier also heats the bath. We have heat exchanger installed in our bath and believe me that we can not work without it. In three hours we have more than 30 degrees, when heat-exchanger is turned off (I know that, because few months ago in winter time the pump, which provides a circulation through heat exchanger broke down). The circuit through heat exchanger is designed in such a way, that we have a constant temperature of 25 degrees +- 1 (maybe1,5).
So the temperature is for sure not a reason for bad dissolving and a lot of sludge in dissolving tank.
NaOH is analyzed every day. From my first post, we increase caustic level to about 130 gpl. I fight against drag-out with an old Prominent pump (I found it in our warehouse), so it continuously pumps 50% NaOH from to a dissolving tank. It is set-up so that 40 liters of 50% NaOH is pumped in 24 hours.
Dimitrij Us [returning]- Kranj, Slovenia (EU)
2005
2005
A. Dimitrij,
I've read ALL that has been said about your problem and it's very interesting. You already have all the basics to set up a proper zinc generator tank.
What maybe has not been addressed is drag-out. With caustic level at 130 g/l you'll have a lot of dragout in a Barrel operation !
Maybe you are drag-in out too much solution that your tank generator can't keep up with it. You compared your operation with another plant running a bigger zinc plating tank with a smaller generator tank, remember they are running a Rack line, not a Barrel line.
There could be huge differences in dragout according to part configuration, dwell times or drip times, barrel hole's sizes, etc.
You are constantly adding adding back NaOH, maybe because of dragout.
We ran a 16,000 liter line with 2,000 zinc generator tank, and we ONLY pump the solution from this tank for 15-20 minutes a day ! This is a rack line.
Increase your drip times, rotate the barrel to drain more solution, use a drag-out tank and return this solution, etc.
Have you estimated how much zinc you are actually plating everyday?
(Zinc deposit on parts)
Maybe if you compare this figure with the zinc actually being used (grams plated + dragout) you might see a big difference.
I'm only trying to give you a different approach, since I can see that everything else has been attempted. Maybe this won't eliminate the problem but it might help you work better.
Good luck,
plating shop - Mexico City, DF, Mexico
Multiple threads merged: please forgive chronology errors and repetition 🙂
What "supporting anode" to use in electroplating zinc
Q. We have started a non-cyanide alkaline electroplating plant.
we would like to know apart from zinc anode, which material can be used as supportive anode for increasing the current density of the anode (surface area).
Partner - Goa, India
2007
A. I believe that steel can be used, Rajesh, but these plating baths can be very difficult to control unless you use a separate zinc generation tank. Does your supplier have any comment?
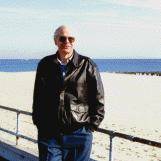
Ted Mooney, P.E.
Striving to live Aloha
(Ted can offer longterm or instant help)
finishing.com - Pine Beach, New Jersey
2007
A. Dear Rajesh,
Definitely MS (mild steel) as Ted rightly said. The supplier of additives should have advised you on this. If you do not have a Zinc Generator tanks of a sophisticated type, just have a 200 ltrs drum withs lots of (300-400 grms/ltr) of caustic soda ⇦liquid caustic soda in bulk on
Amazon [affil link]
and lots of (up to 100 kgs of Zinc metal) added in it. Leave it overnight (Do not add the mix while hot). Start adding the mix to the bath in required qnty. as per analysis.
I have seen the working of up to 13000 ltrs tanks working in this style round the clock.
Please try this method and let me know!
Regards
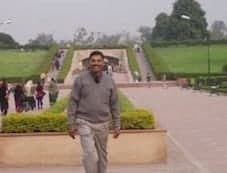
T.K. Mohan
plating process supplier - Mumbai, India
2007
Simple and interesting, TK, thanks!
Regards,
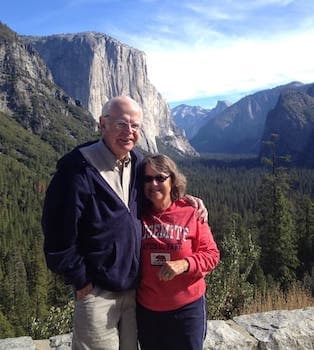
Ted Mooney, P.E. RET
Striving to live Aloha
(Ted can offer longterm or instant help)
finishing.com - Pine Beach, New Jersey
Multiple threads merged: please forgive chronology errors and repetition 🙂
Q. Guys, was following your interesting discussion.
Can you clarify one small doubt I have:
In the dissolving tank, Is it necessary to electrically isolate the zinc basket with the mild steel dissolving tank?
- Bangalore, Karnataka, India
March 3, 2014
Q, A, or Comment on THIS thread -or- Start a NEW Thread