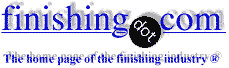
-----
Sputtering vs. plasma spraying for implants
Q. I am working on a process to implant ions in Nitinol (Ni, Ti alloy). If you have any information about that ...
Thanks a lot.
Laurent Brault- France
1998
Q. I am a writer specializing in medical devices and I have come across a process called sputtering which is used for coating products such as hip and knee implants.
I wanted to ask if sputtering is the same as (titanium) plasma spraying and if not, what the main differences are between them. In particular, I am interested in the how the coating material is bonded to the substrate and if one process creates a stronger bond.
Thanks
Tom ClarkeResearcher - London, UK
2004
A. Plasma spray and sputtering are two very different processes. Sputtering is one of several processes that are conducted under high vacuum conditions, involving formation of a vapor of metal. The vapor may be created by sputtering (banging the surface with high energy ions, with the vapor formed from atoms recoiling off the surface), arc (localized vaporization formed by intense arcing, like a spark plug), or evaporation (just heat it up high enough and you get metal vapor). For most applications you also need to create a plasma, i.e., ionize either gas of the metal vapor (preferred). You put a negative bias on the substrate, pulling ions from the plasma while you deposit the vapor, giving good adhesion and a dense coating. Add a reactive gas such as nitrogen into the mix and you deposit a very hard ceramic coating. The technique is used extensively by industry to coat metal cutting tools, piston rings, et al. You can get more information on this process from several professional societies, including the American Vacuum Society, the Society of Vacuum Coaters, and ASM International.
Plasma spray, and its sister process thermal spray, on the other hand, start with a powder of the desired coating. The powder is fed through a gun-like device where some form of combustion or arc is created to melt the powder and accelerate it to the substrate surface, where it sticks. This can be done both in air and in vacuum (low pressure plasma spray), and there are again numerous variations of the process. It is used extensively in the aerospace industry on turbine blades. More information on this process is available from the Thermal Spray Society and ASM International.
Sputtered coatings are generally thin, about one-ten thousandth of an inch, and very tightly adherent to the surface. Plasma spray coatings are much thicker -- several thousandths of an inch -- and not as well-bonded. Only in a few application areas is there an overlap, the most common being turbine blades where there is a high-rate PVD [Ed. note: PVD = physical vapor deposition] process that is used to deposit thick thermal barrier coatings in competition with thermally sprayed coatings.
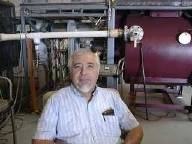
Jim Treglio - scwineryreview.com
PVD Consultant & Wine Lover
San Diego, California
A. I think Jim covered this pretty well. Both processes have found their way to implants for different reasons. The thermal spray process can be applied to produce a coarse profile for better bonding of the implant. There is also a plasma spray for HA [Ed. note: HA = hydroxyapatite] that is widely used. The PVD process is used on the socket side to minimize friction against the mating polymer end plate. Diamond like carbon (DLC) coatings is currently in use. There are also ion implantation modes that are being investigated that is another type of surface modification apart from PVD.
Joe Kubinski- Woonsocket, Rhode Island, USA
2004
A. Actually, the wear surfaces of knee and hip joints have been ion implanted in production for over 15 years. There has been some hesitation on the part of providers to PVD coat the wear joints for fear that the coating could delaminate, with the hard coating material trapping between the bone and prosthesis, or get caught between the wearing surfaces and rapidly abrade the polyethylene. Ion implantation is not a coating, so there can be no delamination, hence its early acceptance. It has proven particularly effective on prostheses where the wear surface is titanium. In fact, titanium wear surfaces don't last very long if they are not ion implanted, leading a number of companies to use cobalt-chrome alloys for the wear surfaces.
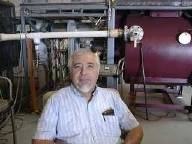
Jim Treglio - scwineryreview.com
PVD Consultant & Wine Lover
San Diego, California
2004
! Thanks for the replies. The information was very helpful and I found a good article on vacuum coating applications on the SVC website!
The weaker bond with plasma spraying seems to correspond with concerns regarding the coating coming off on orthopedic and dental implants. For dental implants, the use of HA and TPS coated products has decreased, while sand-blasted and acid etched implants have increased. Other companies have been looking at other technologies such as sputtering to achieve a roughened implant surface.
Tom Clarke- London, UK
2004
Q. The questions and discussion on the topic of medical implant coatings and surface modification was very helpful. Mr. Tom Clarke, I was wondering if you could provide some more information and/or reference to articles for reasons of decrease in interest in HA and TPS coating. I read that there is a wide scope in HA type coatings because of biocompatibility and enhanced tissue growth.
I would appreciate your response.
With Best Regards,
Pankaj GuptaMaterials Research Analyst - Baton Rouge, Louisiana
2004
A. From what I've been told, the problem with HA is that the body eats it. After a few years, the HA is gone. This sometimes leaves gaps between the bone and implant, which is very bad.
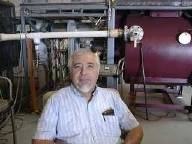
Jim Treglio - scwineryreview.com
PVD Consultant & Wine Lover
San Diego, California
2004
A. I agree that body eats HA applied on implants. However, the main aim to put HA on implants is to facilitate fast growth of bone cells for fast healing.
As mentioned in previous post Diamond like Carbon (DLC) or in layman term called as graphite coating is best coating for implants considering its benevolent properties.This coating protects the implants from wearing,prevents sticking of blood cells and is inert to body fluids. However more research is still being carried out to understand DLC. In some cases Titanium Nitride can also serve as a candidate for bio implants.
- New York, USA
March 10, 2012
A. I can only speak for dental implants, but HA coating fell out of use for two reasons: the HA would tend to fuse better to the bone than to the implant itself, and with high occlusal loads (excessive biting forces in some individuals/sites in the mouth), the HA would break off of the implant.
Secondly, HA coating is very susceptible to penetration by dental plaque, consisting of oral bacteria and their endotoxins. If the roughened HA surface of a dental implant becomes exposed due to some initial or peri-implantitis bone loss, the tendency was for further bone loss to occur because the implant surface could not be adequately cleaned or decontaminated, leading to more inflammation and eventually greater bone loss.
While TPS did not suffer from the first problem, it is considered a very rough surface for dental implants and seeing how so many mildly and moderately roughened surfaces are currently on the market and do so well in both clinical trials as well as everyday clinical dentistry, the HA and TPS surfaces fell by the wayside.
HA is making a comeback, however, in the form of HA particles either peppered along the surface of some implants (such as Biomet 3i's Nanotite surface) and perhaps in the future may be placed at the apical half or third (the portion placed most deeply into the bone) that will hardly become exposed to the oral environment before the entire implant would have to be removed anyway.
- NYC, New York, USA
March 14, 2012
Q, A, or Comment on THIS thread -or- Start a NEW Thread