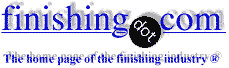
-----
Pitting corrosion on 7050-T7451 and 7451-T7351 aluminum alloys
2004
Dear Mr./Ms.
I alkaline cleaned aluminum parts 7050-T7451 and 7475-T7351 machined by the same shop and after alkaline cleaning/rinsing stages, most of them reveal pitting corrosion throughout the entire machined surfaces. These pits are blackish covered with white powdery corrosion product. They are relatively deep and cannot be removed by means of etching but machining again. After re-machining and alkaline cleaning/rinsing the parts are covered with corrosion pits all over.
Alkaline cleaning is performed in Ridolene # 53, concentration 9.685 g/l that ranges within the control limits (6.2 12 g/l) and also pH = 9.8.
I checked the coolant pH at the machining shop and found it normal 8.6. Coolant is intended for aluminum alloys, is non-corrosive, chlorine free, active sulfur 0 %, and has antioxidants to control bacteria growth but does not contain biocides, as the manufacturer of coolant informed me. The maximum allowable time for the part's surface to be in contact with the coolant is not specified in the Technical Data Sheet.
I noticed oil separation on the surface of coolant emulsion in the collecting basin of the machining unit. This contamination probably comes from the lubricant.
The real contact time of the part's surface with the coolant for this particular long parts varies between 24 hrs 5 days and includes the machining time, waiting period between machining and debarring and vibratory debarring time.
We process smaller parts of the same type of alloys and found no corrosion. Only these particular long parts reveal pitting corrosion all over.
My question is: What factor can cause corrosion on these long parts?
MIHAELA PAPADOPOL- Toronto, Ontario, Canada
That is the nature of the animal. The heat treatment has separated the zinc and the zinc is falling out in the alkaline cleaner (and later in every tank in the line).
If you are racking on titanium, you may be getting a positive voltage between the titanium and the steel tank walls or the immersion heater. Go look for some galvanic voltage and try to reverse it with an adjustable auxiliary rectifier.
Also sometimes in near neutral cleaners the chloride in the tap make-up water (especially in the presence of galvanic voltage) will chew out the zinc from the surface of the 7000's.
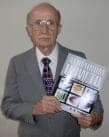
Robert H Probert
Robert H Probert Technical Services

Garner, North Carolina
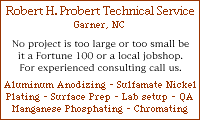
2004
Dear Robert, Thank you for your answer. I realized it is a metallurgical problem. The big dilemma is why only this big parts and not small or medium parts of the same type of alloy, heat-treated? These parts don't show any corrosion after alkaline cleaning. Probably supplier of alloy is different, I couldn't find out.
The big parts come as slabs from alloy manufacturer and than are machined for a certain time (days). The small and medium parts require a shorter machining time.
But the dilemma is bigger when we get 4 big parts very badly corroded after alkaline cleaning and 2 big parts very clean after the same process of alkaline cleaning, same time. I cannot check if these parts were machined from the same batch of raw material.
We did one test with a piece of raw material that didn't corrode after alkaline cleaning but the machined piece corroded after alkaline cleaning. This test was done in the past. I am still waiting for some samples to perform the same test. I asked a sample of raw material, one after machining, one after machining debarring to figure out when this damage of material (corrosion) takes place.
This type of alloy should be resistant to stress corrosion due to this heat treatment if it is conducted properly. Can sulfur from lubricant cause such pitting corrosion (blackish spots)? sulphates and chlorides in water as you mentioned, increase the corrosion tendency of the water and as a result the metals become very quickly corroded. But as I mentioned, after alkaline cleaning we don't have problems with smaller parts of this alloy or other alloys. Chlorides in our tap water don't exceed 30 mg/l. I take as a reference all other parts we process under the same conditions.
I immersed some samples of this alloy in the coolant and than sealed in a plastic bag. I checked them every day, meaning alkaline cleaning. After 6 days I got pits on the surface but not so big. Unfortunately, I cannot reproduce all conditions that parts are subjected to.
MIHAELA PAPADOPOL- Toronto, Ontario, Canada
2004
Dear Mr./Ms.
I too have recently experienced this same pattern of pitting or corrosion on the larger parts out of a 7050 plate. The smaller parts from the same plate have indications, but certainly not as severe as the larger parts that spend considerably more time on the fixture.
I am wondering if a cause was ever determined and whether it was coolant, material or corrosion of another nature?
We have determined this appears on multiple heat lots and mill runs.
Any information would be greatly appreciated.
- New Brighton, Minnesota
2006
A. You state that for small parts less corrosion is observed than for large parts. A reason for this could be:
- the larger part is an extrusion which usually has poor surface characteristics, or
- the large part is machined from thick plate. In this case the material properties in the core can differ considerably from those closer to the surface due to the fact that the level of deformation in the core is less than on the outer surface.
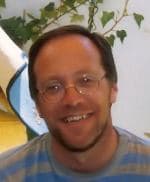
Arnold Langeveld
- Papendrecht, The Netherlands
June 22, 2012
Q, A, or Comment on THIS thread -or- Start a NEW Thread