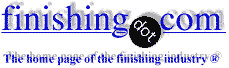
-----
How can I remove Copper plating from Zinc?
[an error occurred while processing this directive]Q. I have an antique wall thermostat, the cover of which is either cast zinc or possibly aluminum. It is copper plated with some peeling damage. I would like to find a way to remove the existing plating so that it can be replated. Does anyone have any suggestions? In a perfect world it would be a non-hazardous, non-electrical method, but beggars can't be choosers. Thanks.
Harry SkrdlaQuality Restoration - Ann Arbor, Michigan
2005
A. ferric chloride ⇦ on eBay or Amazon [affil link] , it will eat the copper off of the metal, but I cannot say what it will do to the rest of the thermostat as it is currently unknown what metal is underneath. As it is I would suggest using sandpaper to remove the rest of the copper, it's safer that possibly using a chemical that will reduce your thermostat to a puddle of goo.
Marc Banks- Elizabeth City, North Carolina
2005
2005
A. Zinc and aluminum can be immersion plated!
immersion coppering for zinc:
50 ccm ammonia
⇦ on
eBay
or
Amazon [affil link] (25%)
30 gm copper sulphate
50 gm tartaric acid
⇦ on
eBay
or
Amazon [affil link] Cold immersion,immediately after plating rinse well!
immersion coppering for aluminum:
50 gm copper tartrate
1 lit water,add ammonia to pH 3,5 ,temp. 100 °C
Good luck!
Goran Budija- Cerovski vrh Croatia
Multiple threads merged: please forgive chronology errors and repetition 🙂
Q. I manage a small shop inside a lighting company. Word got around town we had a plating line. Now we have a thriving small jobbing shop. I am the polisher and also the plater. I in the last few years have a great reputation for succeeding in plating of diecast jobs. But not without a lot of time and heartache, e.g., blisters.
One of my major problems: Is there a way of stripping acid copper from diecast (say old car exterior door handle) as you ask other platers and they won't tell their secrets as they say trial and error. Once you have a blister it is virtually impossible. Any advice would greatly be appreciated.
Regards,
Simon DonhardtPlating Shop - Mt Gambier, S.A., Australia
2004
2004
A. I wouldn't worry about stripping the acid copper. There really isn't a good method to strip copper from zinc diecast. In other places I've worked, the key to reworking diecast was to glass bead blast the entire surface with #9 glass bead at about 25-30 psi. Then polish and buff the surface and if you use a non-etch cleaner followed by a mild electrocleaner, acid salt and copper strike, you should have good adhesion. Another method for cleaning diecast is to clean with pumice ⇦ on eBay or Amazon [affil link] powder. It is very effective for removing smut prior to a soak cleaner.
Good luck
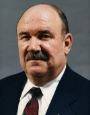
Daryl Spindler, CEF
decorative nickel-chrome plating - Greenbrier, Tennessee
Q. I came across an article recently about stripping copper plating from a zinc die-cast part. In the article, it mentioned using lime sulfur (calcium polysulfide) to strip the copper, but it never gave an exact amount (g/l) or any sort of concentration.
I am curious whether anyone has any other information about this procedure or any other copper stripping solution
- Coquitlam, British Columbia, Canada
July 8, 2016
A. Good day Bri.
I have re-worked zinc die cast automotive parts and stripped them of nickel/copper (reverse alkaline cleaner to strip chrome before this strip) ) with 750 ml/l sulfuric acid, 3% glycerin, use a lead cathode anodically.
I know it seems odd, but the stronger sulfuric concentration does not attack the zinc. This is where the glycerin comes in.
Proper PPE and chemical knowledge about mixing sulfuric with water is ESSENTIAL!
Any defects/voids in the stripped zinc can be filled with a low melting temperature solder and polished with fine grit abrasive ( finishing with 600-1200 grit)/polishing compound and ready for plating.
Hope this helps.
Regards,
Aerotek Mfg. Ltd. - Whitby, Ontario, Canada
Q. Hi Eric,
Thats great! Thank you for sending that information. How much of the 3% glycerin is needed for this?
- Coquitlam, BC, Canada
July 13, 2016
A. Good day Bri.
That would be 3% by volume of glycerin.
If you would make 1 liter of stripping solution (try it on a small lab sample first), @ 3% glycerin, you would need to add 30 mls. (minimum).
Tell us about your progress.
Regards,
Aerotek Mfg. Ltd. - Whitby, Ontario, Canada
July 14, 2016
Q. Hi,
Would you be able to provide me with a little more information in regards to this solution. For example, proper grade of Glycerin (Our supplier carries a 99.7% kosher Glycerin) Is this correct? Also, do you have any information in regards to solution maintenance (what the pH should read, will we have to dump the solution once the metal content gets higher, etc.)?
Any and all help is VERY much appreciated.
- Coquitlam, BC, Canada
July 18, 2016

Q, A, or Comment on THIS thread -or- Start a NEW Thread