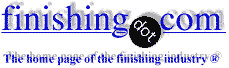
-----
Current density recommended for 7075 in sulfuric acid
2004
I am trying to anodize 7075 aluminum pieces with 10dm^2 surface area and all the conditions that I've tried don't seem to work. I need 15-25 micron layer thickness.
My standard conditions are 15% sulfuric acid
8 g/L aluminum
50 °F
16V (draws about 20Amps)
20 minutes
All I get is 2-5 microns thickness that once its dyed leeches out in seconds when taken out from the dyeing bath. I think that the pores are too big and therefore the color streaks. I understand that I need higher current density to obtain smaller pores. I am unfortunately limited by my power supply since it maxes out at about 20-25 amps.
20 amps is 2A/dm^2 current density. Is this too low? what current density should I be applying?
Ive tried 12% to 18% sulfuric acid, lowering the temperature to 30 °F, and all this does reduce the current when I fix the voltage at 16 or 17V.
The pieces have threads that are becoming looser and looser every time I etch them. What should I try next?
Diego Benitezstudent/hobbyist - Woodland Hills, California, USA
2 amps / dm2 is 20 ASF which should work. You mention nothing on the surface preparation. 7075 has a high copper content as well as other alloy metals which makes it quite hard to get a good coating. Surface prep is important. That could have a bearing. You might not have an adequate lead to the anode & cathode and part of your amps could be going up in line loss/heat. 18 volts will get you more coating in a given period of time. Can you do less parts at one time to increase thickness? You may have to go a longer period of time than the 20 min.
James Watts- Navarre, Florida
2004
Q, A, or Comment on THIS thread -or- Start a NEW Thread