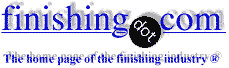
-----
Cracking of 17-4 PH after chrome plating
I would like to know if anyone has experience with chromium plating of 17-4 PH stainless, and having shallow networked surface cracks in the base metal. To explain a bit further, this is a casting, with a ground surface on a flange. The flange itself is not plated, but was masked. The part was passivated, stress relieved at 375 F, then chrome plated, no post-plate bake. Cracks were found by mag particle after plating, but were not detected by mag particle before passivating. I read in the ASM handbook that stress relief of high strength steels is recommended before chrome plating. This part was heat treated to the H1075 temper. I measured surface hardness across the ground face using a microhardness tester, and see some variation, from about 32 HRC to 39 HRC. My current theory is that the grinding was a bit aggressive, and left some significant residual stress in the surface. Exposure to the passivation (nitric) or plating bath, or some pre-plate treatment resulted in hydrogen embrittlement cracks. The cracks are transgranular, and extend approximately 0.5 mm maximum into the base material. Any thoughts?
David Christietest labs - Lansing, NY, US
2004
Hydrogen embrittlement is a boogyman like CANCER is. Now, what is your definition of hydrogen embrittlement and specifically, why do you think that you have it?
I was brought up to believe that H2 embrittlement was intergranular, not trans granular. having mounted and etched several thousand samples and several hundred for intergranular corrosion, I can tell you that it takes a darn good metallurgist to determine it. My batting average was under 500, but I am a chemist. Also, a range of 32 to 39 on the same part, but diffeent areas is very suspect to me. I suspect a hand tester (portable) that is not being employed exactly the same each time.
A point of technicality, but a microhardness tester normally reads in knoop or vickers hardness, not HRC. To the best of my knowledge, it can not be done on a part, but requires a mounted sample that is highly polished and perfectly flat. Yes, I know, picky-picky, but the real authorities need the correct information to help.
James Watts- Navarre, Florida
2004
Hi,
Thanks for the assistance. Attached is a photo of the condition I am dealing with.
test labs - Lansing, NY, US
2004
First of two simultaneous responses --
Thanks for the response. Perhaps I should clarify that the microhardness was a knoop tester, and the values I gave are conversions. More information was forthcoming from my customer, and it turns out that the part is fixtured for grinding the flange face by way of the central bore of the part. The part is then spun, lathe-fashion. The hardness variation I observed was as circumferentially oriented soft/ hard bands. I believe that the grinding operation is at fault, and imparted high tensile stresses at the surface. Exposure to passivation and/ or cleaning and/ or plating bath resulted in transgranular cracks that, I suppose, are more correctly identified as stress corrosion cracks. This is my current thinking, but again, I welcome any thoughts or other opinions. Thanks, folks.
David Christietest labs - Lansing, New York
2004
Second of two simultaneous responses -- 2004
Wow! I must have led a very sheltered life. I have never seen cracks like that, even on really hard 4140 parts with a complex geometry that got a heavy chrome layer..
I could be very wrong, but I will bet a cup of Starbucks that what you are looking at was not caused by hydrogen embrittlement. One reason is that the H2 embrittlement would manifest itself in the metal under the plate and would take months to propagate thru the part. The second reason is your part is not all that hard.
A post plate bake is normally more important than a prebake for H2 embrittlement. A prebake is normally reserved for much harder parts or ones that have been heavily machined and or cold worked and you are trying to reduce the internal/surface stresses of the parent metal..
I hope that Lee Gearhart sees this picture. He is a real metallurgist.
James Watts- Navarre, Florida
I did not dare suggust that grinding was the problem, but that was my honest guess when I saw the picture. Note how the cracks are radial from the center hole and only have some relationship to the amount of metal in back of the spoke. With the additional information, I would guess that they overheated the part. There are some tests that can check for burning or localized overheating. I do not remember exactly what they were, but at least one is non destructive.
My guess is inadequate coolant combined with the wrong sized grit in a wrong matrix resin. The wheel needs to break down more is my guess. Speeds can also be a factor, since both the part and the wheel are in motion.
James Watts- Navarre, Florida
2004
James, thanks so much for the kind words!
Dave, based on what I see here and what you've said, I'm in solid agreement with your assessment. I know that even wrought 17-4 can crack due to hydrogen embrittlement due to chromium plating- in fact, even presented it at that root cause conference that Ron Parrington dragged me to in Cleveland, May 2000. (My paper is three after yours & Ron's in the proceedings!) Normally 17-4 will be immune from hydrogen effects, but if something unusual like high stresses from abusive grinding are present, you can definitely get cracking. That the part is a casting, with the segregation inherent in cast structures (reflected in the hardness variation, I'd guess) will only make it more susceptible.
Unfortunately nital etch means of detecting grinding burn doesn't work on 17-4, since it's not a high carbon martensite structure. I think your client found the best testing method, as unhelpful as that silver lining is!

Lee Gearhart
metallurgist - E. Aurora, New York
2004
Q, A, or Comment on THIS thread -or- Start a NEW Thread