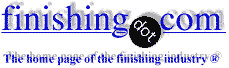
-----
Localized activity between silicated cleaners and phosphating on EG
2004
A meta-silicated cleaner is used as part of a pre-treatment facility at an automotive assembly plant. The cleaner is used to remove pressing lubricants prior to phosphating. The phosphating stage is preceded by rinsing and activation stages.
A pin-hole problem is encountered on electro-galvanised sheet that is processed through this plant. SEM/EDAX analysis showed the presence of meta-silicate residues on the surface with a different phosphate structure(compared to the adjacent areas) beneath it. Furthermore, the electro-galvanised coating has been eroded up to the steel base. The size of the defect is approximately 20 micrometer in diameter. It is believed that the meta-silicate surface residues from the cleaning section are resulting into a localised activity in the phosphating step.
Did anybody encountered a similar phenomenon with silicated cleaners? What remedies can be proposed?
Koos Greylingsteel producer - Vanderbijlpark, Gauteng, South Africa
Hi Koos,
All residues need to be removed from the metal surface before the parts can be phosphated properly. Your results indicate that silicate may be one of these residues. The problem may lie in the rinse stage following cleaning. The rinsing may be inadequate or residues are building in the rinse tank and are being carried over to the phosphating stage. Increasing the rate of overflow in the rinse stage and increasing the frequency of dumping of the rinse tank may help the situation. If this is a spray application, the nozzles should be inspected to make sure that the rinsing action is optimized.
George Gorecki- Naperville, Illinois
2004
Silicates are great detergent builders, and meta-silicate is probably the most common one of them. They are also notoriously poor rinsing materials.
You need to limit the amount of silicate in your cleaning, filter the tank if necessary to keep the solids low. Also attack your rinse stages as George said above.
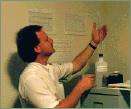
Jeff Watson
- Pearland, Texas
2004
Q, A, or Comment on THIS thread -or- Start a NEW Thread