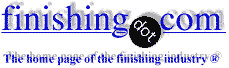
-----
Plating problem in thread of M3 screws
2004
We use M3, M4 etc type of 8.8 grade M.S screws in our products.
M3 screws have very fine pitch of 0.5 mm. These screws are heat treated (Hardened and tempered ) to make 8.8 grade. then they are Zn plated (with yellow passivation). We are facing plating problems in these screws. Plating is achieved on head and tail but not on threads. This may be due to improper cleaning. We have alkaline bath for zinc plating. Pickling is done in HCl. If pickling time is increased then threads become minus.
We would like to seek guidance regarding proper cleaning media / method.
Zankar DesaiElectronics - Vadodara, Gujarat, India
Dear sir
Regarding your problem my view is that you are not properly cleaning the scales of the hardened steel. I propose permanganate with caustic 1;5 ratio with temp 60 to 80 c dip time 10 to 15 minutes followed by HCl pickleing w ith good inhibiterin HCl will clean properly.
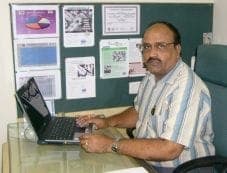
P. Gurumoorthi
electroplating process chemicals - Chennai, Tamilnadu, India
2004
Dear Mr Desai,
Change your Heat treatment method to a non-scaling process such as vacuum furnace method. Precede this with thorough cleaning before heat treatment also preferably followed by a mild zinc phosphate process. Absolutely clean parts should be sent for Heat treatment.
No amount of oxidising or pickling will clean the kind of scale that you are talking about. You will have to sell your screws as nails if you try pickling them like this!
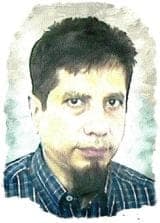
Khozem Vahaanwala
Saify Ind

Bengaluru, Karnataka, India
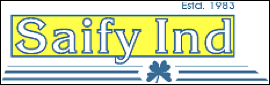
2004
2004
Dear Mr. P. Gurumoorti,
This is with reference to my inquiry letter No: 32392 for which you suggested to use KMnO4:Caustic ratio of 1:5. Can you tell us how much gm/litre maximum can we use in this ratio. What is ideal concentration. What is the replenishment value of KMnO4 and caustic in the solution.
We tried 20 Gm/litre of KMnO4 and 100 Gm/litre of caustic solution. We have obtained desired results in 1st trial lot but effect becomes less after 3rd trial in the same bath.
Requesting your response.
Zankar Desai- Vadodara, Gujarat, India
Q, A, or Comment on THIS thread -or- Start a NEW Thread