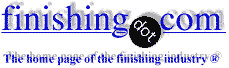
-----
Phosphating weight determination
Q. Well can any one tell me how to determine the weight of phosphate coating (Zn, Mn, or Fe)?
Husnain AhmedPOF - Wahcantt, Punjab, Pakistan
2004
A. We are appending the following extract from a Standard Specification in the hope that you will find it useful …
6.3 Test for Weight of Coating.
6.3.1. The weight of the phosphate coating should be determined by the following method, on samples which have not received any finishing treatment.
6.3.2. The phosphated panel shall be of suitable size (approximately 5 cm x 10 cm), it shall be numbered before weighing for identification and shall be thoroughly degreased in trichloroethylene vapour or clean mineral spirits ⇦ on eBay or Amazon [affil link] . The panel (after drying if necessary and cooling in a dessicator to room temperature) shall be weighed to the nearest 0.1 mg and this weight shall be recorded as "X grammes"
6.3.3. The panel shall then be immersed in a freshly prepared solution of concentrated hydrochloric acid in which antimony trioxide has been dissolved as inhibitor in the proportion of 20 grammes per 100 ml. of acid. The temperature of the stripping bath shall be maintained between 25 °C and 35 °C. When the coating has dissolved off (a period of 5 minutes is normally sufficient), the component shall be removed from the acid, washed for 30 seconds in running water, and any non-adherent matter shall be removed with a soft wet brush. The panel shall then be dried with a clean absorbent material (lambs wool), placed in a dessicator for 10 minutes and re-weighed to the nearest 0.1 mg. This weight shall be recorded as "Y grammes".
6.3.4. The steps outlined under 6.3.3. shall be repeated until two successive weighing do not differ by more than 0.5 mg. The final weight Y grammes shall be used to calculate coating weight in accordance with the formulae given under 6.3.6.
6.3.5. The total panel area shall include both sides of the panel, if both are coated
6.3.6. The coating weight in g/m2 shall be calculated from the formulae:
Coating weight+ X Ž Y ¤¤¤¤¤¤¤¤¤¤ X 10000 Total coated panel area (cm3)
Where X = initial weight in g, and Y = final weight in g.
----
Ed. note: this formula did not survive the conversions between keyboards, e-mail packages, etc. We believe that it is supposed to read:
(X - Y) * 10000 / Total coated panel area (cm3)
6.3.7. A "control" panel having the same metal composition and of the same dimensions, shall be used and the weight loss of the panel should be applied as correction factor in the coating weight.
S. MEENAKSHISUNDARAM- CHENNAI, TAMIL NADU, INDIA
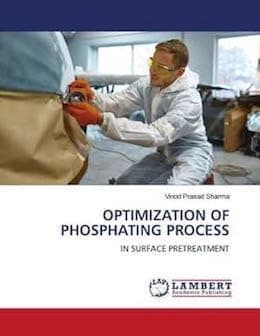
avail from AbeBooks, or Amazon
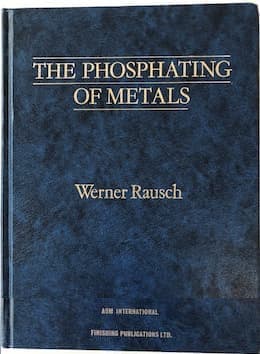
avail from eBay, AbeBooks, or Amazon
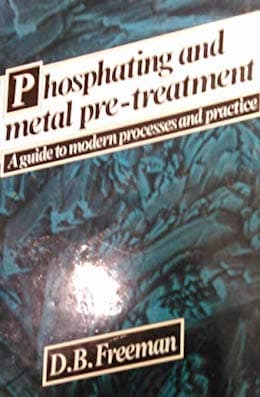
avail from eBay, AbeBooks, or Amazon
(as an Amazon Associate & eBay Partner, we earn from qualifying purchases)
How many microns should phosphate coatings be, and how to check?
Q. Hi, I've a doubt in zinc and iron phosphating process --
How microns should be maintained in zinc & iron phosphating parts before powder coating and how to check it. Please send me the checking method.
Employee - Coimbatore, Tamilnadu, India
September 2, 2018
A. Hi Manoj. Zinc and iron phosphate coatings are usually designated by weight rather than thickness. There is no single proper weight or thickness -- it depends on what specification you are processing in accordance with.
But we have appended your inquiry to a thread which answers your question about the checking method. Good luck.
Regards,
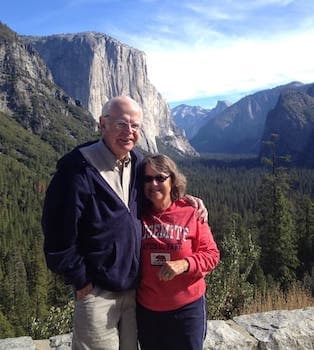
Ted Mooney, P.E. RET
Striving to live Aloha
(Ted can offer longterm or instant help)
finishing.com - Pine Beach, New Jersey
September 2018
A. Hi Manoj,
There are no straight answers when it comes to metal finishing! There are no standard thickness or standard solutions ;)
I agree obviously with Ted, and would only add that our local plater tends to say it's about 8-10 µm in terms of thickness when they use it as a base for painting.
As to how you'd check that, they have an x-ray machine but you probably just weigh it and divide it by the surface area?
Bronte Precision Engineering - Bradford, West Yorkshire, UK
September 5, 2018
A. I'm not familiar with iron phosphate, but am quite familiar with zinc phosphate. Get yourself a 1 liter bottle of ammonium hydroxide solution and add 44 grams of ammonium chromium crystals to it. This is the stripping solution.
Make a sample of known size, coupon, disc and weigh it. Completely immerse the coupon or disc in a small container of the stripping solution for about five minutes. Rinse, dry, and weigh. Automotive usually requires 200 to 250 mg/foot squared. Coil coater's prefer 120 to 180 mg/foot squared.
Don't forget that the coupon, disc has two sides, common mistake.
Coil Coating - Brampton, Ontario, Canada
September 11, 2018
Q, A, or Comment on THIS thread -or- Start a NEW Thread