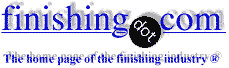
-----
Coating peel off / high enamel rating on 3 piece cans
2004
Q. Dear Sir/ Madam:
I am a quality controller in a can manufacturing plant (for tuna and sardines) with no strong experience on can making yet.
We are using the electrolytic tinplate for our 3-piece cans (603); we have our own coating line but we export our tinplates from either Japan or Taiwan. We use gold and alum lacquers on the internal side and just plain outside.
Our lacquered tinplates passed all the required standard specifications but after production, specifically after passing the beader machine, problems such as these arise;
1. Very high enamel rating
2. Coating peel-off on the flange area
These problems occur only to some skids of the tinplates, while some skids are passable.
We are checking all possible causes like the temper, coating dry film weight, presence of oxides, warming up the beader before full operation; but until now, we don't find the cause and solution to our problem yet. I hope you could give me some information and advice regarding this matter. It would be greatly appreciated.
Thank you.
I would greatly appreciate it.
Ann Aballecan manufacturing plant - Canlubang, Laguna, Philippines
A. Dear Anne,
I have come across problems like this in the past (as we are a coating supplier); there could be a number of causes for this problem, one of them could be tinplate, the coating especially if it's overbaked, flexibility and Film Weight of the coating.
I would need to know some more details but I am not sure how you can contact me.
With kind regards,
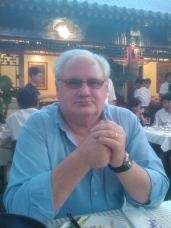
Doug Dr.Rasik
product designer - Bangkok,Thailand May 19, 2010
Ed. note: Thank you, Dr. Doug. This forum is for public discussion, not private contact, and I'm sure many readers will profit from your reply even if Anne isn't currently frequenting the forum 6 years later. Think "Dear Abby" or "Hints from Heloise". Thanks again!
December 30, 2011
A. Ann,
The causes of high enamel rater values, leading to de-tinning or under-film corrosion are as follows:
1. The lacquer coating is not flexible enough and this out over the expansion rings of the ends or on the body beads. This leads to increased porosity.
2.The lacquer is under-cured leading to incomplete polymerisation and therefore, in the presence of high acid or corrosive products, allows the acid fumes to penetrate by osmosis and causes under film corrosion.
3. The coating has pores or is scratched during manufacture of the can.
4. The base epoxy used for the coating contains impurities which will show up as black spots under magnification>=60x. These are potentially weak spots in the coating and will lead to corrosion.
5. The processing parameters such as product fill temperature and headspace may be wrong, leading to loss of vacuum. Also high storage temperatures will lead to internal corrosion.
Hope this helps
Padu
Can Making Specialist - Bangalore,Karnataka, India
April 30, 2013
Q. Dear Forum,
We are into Mango pulp exports, and we are coming across the following issues:
1. Peel off of lacquer outside (on the seaming area) as well as inside (at embossed area in the top lid as well as in the bottom lid corners). Due to this, sometimes the health authorities are rejecting the consignments at the receiving end.
2. The cans are locally sourced (.28 mm cans) A10 size. We use GL/Pl, GL/ARL, GL/white laq cans.
3. The flattened cans are reformed and beaded at processing unit and then filled with mango pulp with 85-90 degree temp and then retorted and cooled.
4. Is there any way to get rid of this issues like rusting, paneling etc. Please provide some tips and why such things are happening; it's difficult to hold can mfrs. responsible. Often they escape blaming on processor due to poor GMP. But my question: how the canning is so successful in Thailand, are they using flattened cans or using built-up cans?
Thanks
Sharav.v
- Chennai, Tamilnadu, India
Q. Dear Sir,
I am QC Supervisor in can manufacturing co., we coat, print and manufacture the can. Recently we are receiving complete of rust on top and peel off buff lacquer for 20 ltr. drum. As we tested from our side, we no found any problem of curing, nor any temp. issue and all lab test scratch, cross test, and impact test are ok. But customer complaint peel off and rusty issue that too after more then year. Can you help me to understand what else to be done to avoid such complaint.
Thanks
- SHJ , UAE
January 29, 2019
A. Hello friends,
I am a can manufacturer and we make millions of OTS cans.
Lacquer scuffing/peel off, is the cancer to the canning industries. Day in and out there are attempts being made to tackle or overcome the issue but no actual success. The main reason behind this is the typical seaming operation that is associated with canning. It's a frictional operation, hence generates max peel off issues over the ends being seamed. The only way is to control the peel-off by putting stringent check after the seaming operations. Lacquering peeling can be easily observed before and after the seaming process by performing a simple CUSO4 (copper sulphate) test.
Thanks
Can Manufacturer - Vadodara, Gujarat, India
June 25, 2019
Q, A, or Comment on THIS thread -or- Start a NEW Thread