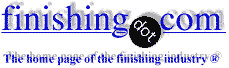
-----
Some parts aren't getting anodized
2004
We have a cast aluminum (356 T6) underwater camera housing that has a 6061 T6 aluminum latch block secured to it with interference fit aluminum 6061 T6 dowel pins. The whole assembly then gets anodized black. Well low and behold on 5 of my last 20 assemblies the latch blocks and dowel pins didn't take the anodizing. I understand that there must not have been electrical contact, but, how could that happen? It is a tight press fit after all. Has anyone else heard of this happening or seen it happen?
My boss wants me to figure out why this happened so any feasible explanations would help me greatly.
Thanks a million,
Benji
Benjamin Rappoportlight & motion - Monterey, California, USA
First of two simultaneous responses --
If you are absolutely positive of the good quality contact, then the only other option is the part was not cleaned adequately in the unanodized areas. Oil, rtv, silicone or ?. Try cleaning the parts separately prior to the press operation and check the conductivity between the parts after pressing. Was any "lubricant" used in the press step? zinc oxide ⇦ on eBay or Amazon [affil link] or silver oxide or ?
James Watts- Navarre, Florida
2004
Second of two simultaneous responses --
What tends to happen on stuff like that, is that a small amount of sulfuric can seep in between the pin, and the hole. An anodic coating is formed, that insulates the pin from the hole, and the coating stops building. I would bet that your pin has a very thin coating on it, but not enough to take the dye that makes it, and the latch, black. At least, thats my theory, when its happened to me in the past. The best way to do this would be to anodize the latch and the housing separately (thats better anyways, as its not good practice to anodize different alloys in the same batch), then attach your latch with a SS dowel pin (make sure you mask the dowel pin hole(s) prior to coating).
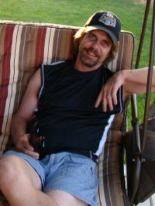
Marc Green
anodizer - Boise, Idaho
2004
2004
Thank you for your responses. We are not using any lubricant in the assembly process. I am taking to heart the response about a small pocket of sulfuric acid. I did get a visual indication of some partial anodizing. Is there anything my anodizer can do to prevent this?
If I anodize the parts separately and press them with a SS dowel pin. How am I preventing the insides of the holes from corroding? (Is the press fit in fact adequate to prevent salt water from corroding my aluminum housing?
Best Regards,
Benji
Benjamin Rappoportlight & motion - Monterey, California
First of two simultaneous responses --
Your anodizer would have to make electrical contact on both the housing, and the latch, in order to minimize the problem. You mentioned the concern about saltwater corrosion if you were to assemble after coating. The reason I suggested masking the holes for the dowel pin was to insure that you could get your pin to go in, as the anodizing will decrease your your hole diameter. If you wanted to pursue the SS pin idea, you might have to oversize your dowel pin holes, and then have them coated. However, I don't see any difference between the 2 options, as right now, you have 2 bare aluminum surfaces where the dowel pin is inside the hole, and that too, is susceptible (sp?) to corrosion.
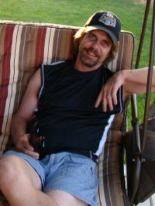
Marc Green
anodizer - Boise, Idaho
2004
Second of two simultaneous responses --
Apparently your press fit is not tight enough. Make the pins a bit bigger or the holes smaller, or roll a knurl on the pins to tighten them.
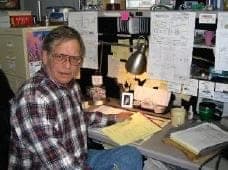
Jeffrey Holmes, CEF
Spartanburg, South Carolina
2004
Q, A, or Comment on THIS thread -or- Start a NEW Thread