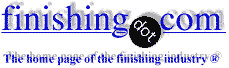
-----
Ra as compared to AA for surface finishes
I am considering quoting a job that calls for a finish of Ra125 and Ra63 and after reading your site I am wondering if these values are correctly displayed. Does this make sense to you or should they have expressed these as Ra3.2 and Ra1.6? I did not want to question them on it until I knew what I was talking about. This job is coming up soon so if you could respond as soon as possible it would be greatly appreciated.
Thanks,
David Starchermachine shop - Irving, Texas
2004
Sounds like you are confused on 2 issues. 1. the first Ra mentioned is a basically a standard surface feature which 2. you seem to try to convert to an RMS by dividing by 4., but used Ra instead again. the second Ra does seem a bit fine and needs to be clarified. I'm not sure how to advise you about this matter. One way is to try and get a sample part to match the surface.

AF Kenton
retired business owner - Hatboro, Pennsylvania
2004
2004
There are a number of technical resources you might find helpful in understanding these terms in a meaningful way.
(1) The Ra 63 and 125 terms you use are incomplete without reference to te measurement units, in your case micro-inches. The 125 micro-inch surface profile measurement is not uncommon for a machined or ground surface, 63 would usually indicate some finish machining or mass media finishing (barrel or vibratory) with ceramic media shapes and aqueous compounds.
(2) There is a fairly good discussion of surface finish measurement terminology as related to surface texture at: http://www.predev.com/smg/specification.htm, they have on this page a chart showing typical Ra values for various machining, fabricating and mechanical finishing operations.
(3) Another potential resource for technical help in this area might be the Society of Manufacturing Engineers - Debrring, Edge-Finish and Surface Conditioning Technical Group. A link to this technical group's web page would be: http://www.sme.org/cgi-bin/communities.pl?/communities/techgroups/deburring/deburring_rstr.htm&&&SME&
(4) Machinery's Handbook discusses this as well as several related topics including surface integrity.
Regards,
David A. Davidson- Spokane, Washington
Q, A, or Comment on THIS thread -or- Start a NEW Thread