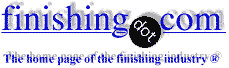
-----
How to choose the right cutting tool plating technology
Thank you for this opportunity to gather more information.
Dreaming Creek is a manufacturer of Timber Frame Homes. We operate a 5-axis CNC machine that utilizes a 40mm x 150mm long HSS or Carbide Roughing End Mill. The solid carbide end mills are very expensive $950 each and wear quickly..less than 4 hours of actual run time. Keep in mind that we are cutting into white oak, not metal. I have spoken to several plating companies that offer PVD, CVD and Composite Diamond Coating. I like the idea of the Composite Diamond Coating since the coating can be removed and the tool re-ground but I have concerns about the longevity of the coating vs. a plasma CVD for instance. The cost is more palatable for the composite coating but is it right for the job?
I freely admit that I am out of my element trying to choose the correct tool. It seems that using a good tool steel instead of the costly carbide as a base material is a better alternative. Note that the wear occurs on the first 1-1/2" of the tool. I'm told that masking doesn't make much sense for Composite Diamond Coating but may for PVD or CVD.
What would an unbiased expert suggest.
Mike GaudreauDreaming Creek Timber Frame Homes - Floyd, Virginia
2004
First of two simultaneous responses --
Go with the PVD coating. The best approach would be to discuss your application with the coating supplier, find out what coating is best. I would guess you'd want TiAlN, a very hard, tough coating. They're also offering combination coatings -- a solid lubricant coating deposited atop TiAlN or the like. More expensive, but they should work very well. All of the PVD coatings (except ZrN) can be stripped, the end mills resharpened, and then recoated.
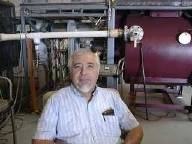
Jim Treglio - scwineryreview.com
PVD Consultant & Wine Lover
San Diego, California
2004
Second of two simultaneous responses -- 2004
I am not an expert, but I have seen tools last longer than that cutting 1" thick stainless steel. Granted you do not use cutting fluid on wood. I have a gut feeling that feeds and speeds could be part of your problem. second, all carbide is not equal. Some is poor, being not much better than a cobalt drill. I would also guess that you have a less than optimum chip relief incorporated into the bit.
I would thing that a properly designed carbide bit could be resharpened numerous times, inhouse with the proper tool sharpener and a competent employee. Running a bit or mill until it is seriously dull certainly is not cost effective. I do know that resharp bits are a waste of time if they are not sharpened identically and at a precise angle. An EN or chrome or TiN coating is more valuable for its ability to clear chips than it is for cutting ability. As stated , I am not an expert or a tool designer, just a user, but I would question the tool design and the feeds and speeds. This is a letter that might stimulate more knowledgeable people to reply.
James Watts- Navarre, Florida
Thank you gentleman for your responses. The feed speed issue is certainly one that we would love to control but cannot. The process involves cutting 6" deep mortises and we are at the mercy of the machinery/software designer. The grade of carbide is a good point, however I did intrust that to the company that makes the tool for us. I have asked the tool manufacturer for his thoughts concerning PVD or CVD coatings and he stated that they offer little to no significant increase in tool life where woodworking is concerned. We are going to look at the possiblity of manufacturing an insert bit tool rather than a solid carbide. Your responses are very much appreciated. A wonderful forum and opportunity for all participants to gain more knowledge, expertise and a business edge.
Mike Gaudreau- Floyd,VA, USA
2004
Feed and speed can be optimized by the software MFG.
Also, since you can not use coolant, a high pressure air could be rigged to point in the right area to cool the bit and to help with the chip removal. You probably have one innovative /mechanical person that could rig this up for a series of trials. Caution, chips can fly quite a distance, so excellent eye protectiion will be required.
James Watts- Navarre, Florida
2004
Many people in wood processing industries have found that cryogenic treatment of their cutting tools brings greatly extended life and improved cut quality as well. HSS tools especially benefit. I am familiar with millyards that utilize this cryogenic treatment on planar knives and saws; loggers that use it on chain saw blades and bars; cabinet makers on chisels and band saws. Each of these applications has reported great results. I have also seen chipper blades gain greatly extended life.
One of the benefits of the process is that it is a THROUGH treatment -- the metal transformation that occurs from cryogenic treatment modifies the entire piece. As a result, the benefits stay with the part AFTER re-sharpening, so it is a one time treatment. This compares favorably to coatings that wear off and have to be re-applied.
If you are looking for extended life from increased wear resistance, then I would suggest that you investigate deep cryogenic treatment (or cryogenic tempering as it is sometimes called.) It has a particularly good track record in the wood proceesing industries from my experience.
Robin RhodesWorcester, Massachusetts
2004
Q, A, or Comment on THIS thread -or- Start a NEW Thread