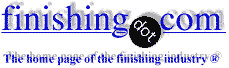
-----
PCB can plating and core materials
[an error occurred while processing this directive]2004
Questions
1) If I want something (e.g. 1" x 2" x .5" size, punched out of metal approx. 0.010" thick) that is both springy (to press against something in compression) and also solders well, and also does not oxidize for 20yrs (I want to surface to conduct electricity for 20 yrs, while the part is in a box in a factory), what should I use for the base metal and the plating?
Spring steel base?
Bright Tin plate?
something in between?
2) Is there someone that sells this material already made so that all I need to do is stamp it?
3) In another case, I am looking at making a PCB can to solder to a PCB board, using mild steel base and bright tin plate (no spring). After making the part, how long before it tarnishes to the point where it does not solder well? How can I pack these to reduce tarnishing while on shelf (vacuum sell batchs of 100 qua in plastic?)?
GL Weinrgwi - Som, Massachusetts
Personal opinion based on trying to keep customers happy. Bright tin can be soldered with no problem for a couple of weeks or so, depending on a lot of storage conditions. Matte tin will solder fairly well two months later under the same storage conditions. But the darn customers like the look of the bright tin and then bitch because there are soldering problems 3 months later. I think that a solder plate rathr than pure tin is an even better shot. As soon as the tin plated parts come out of the oven and cool down, dip them in a solution of stearic acid ⇦ on eBay or Amazon [affil link] and Xylene ⇦ on eBay or Amazon [affil link] - 2 % if my failing memory serves me at all.
Some plastic promote corrosion or oxidation. Store them in a widemouth bottle like a mason jar. If you can flow nitrogen gas to the bottom of the jar and then seal it rapidly = very little oxygen which means it will solder better for a much longer period.
We did a study for a company that had a few thousand fittings on the shelf for over 2 years and would not solder. We tried alkaline cleaning, acid cleaning , a combination of both and finally both with a very very thin strike of tin. The customer said that they all worked about the same and allowed fair soldering. All received a stearic acid ⇦ on eBay or Amazon [affil link] dip before returned to the customer.
James Watts- Navarre, Florida
2004
Q, A, or Comment on THIS thread -or- Start a NEW Thread